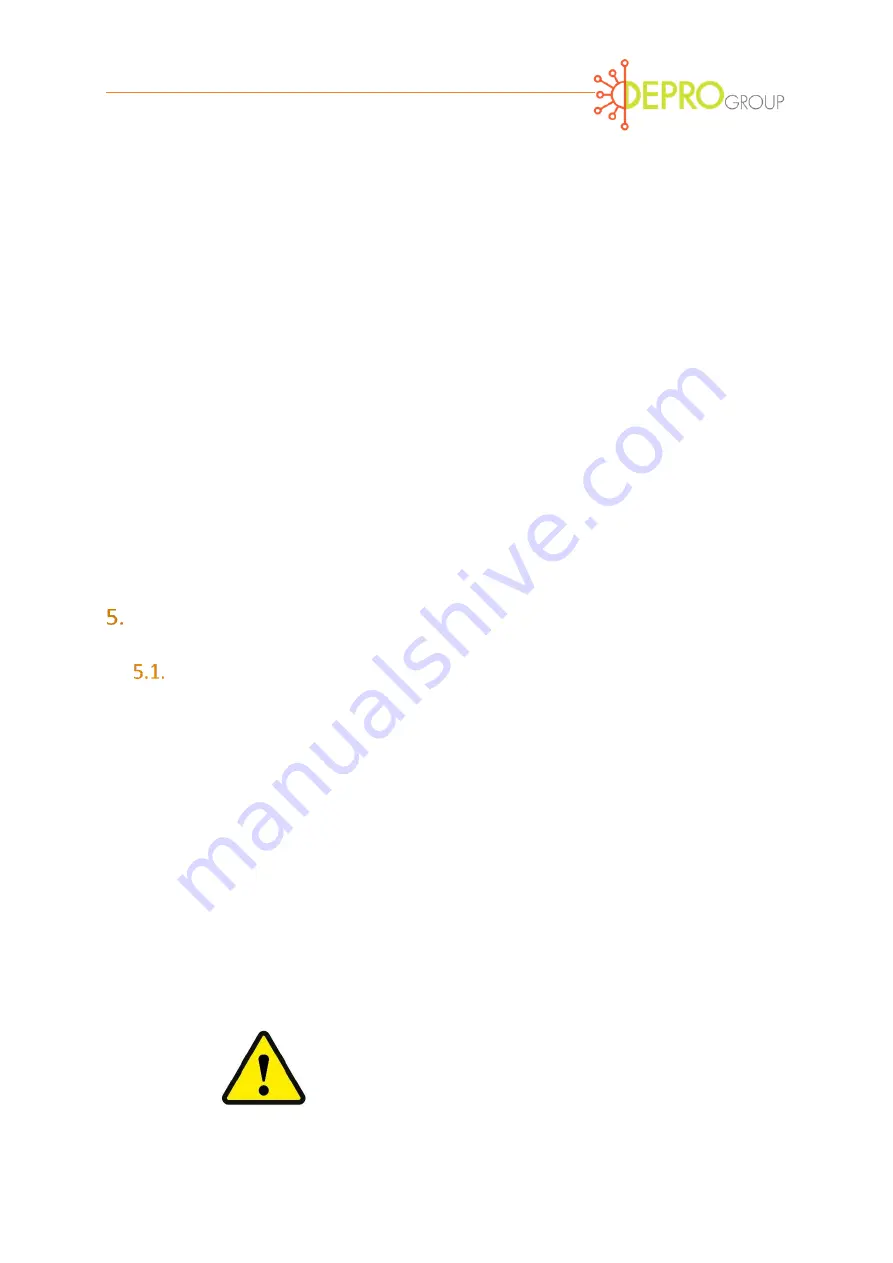
Check the function of each supply line independently via the manual overrides or the system
PLC. Ensure FIGURE 9 HOLDER AND BLADE INSTALLATION FIGURE 10 STANDARD HOLDER AND
BLADE THAT MAKE UP THE MILLING TOOL8
An air steam is present within the milling unit on both sides, diagonally above the
milling tool as well as at the end of the exhaust pipe.
The electric drive has the correct direction of rotation (clockwise from the top of the
gearbox).
The machine is not designed for continuous operation and as a result it is
recommended that subroutine be developed in the PLC run-time limiting run time to
a maximum 30 seconds.
In the system PLC, the rotation signal exists while in operation. One version presents a LED
with a fast pulsing signal. An optional version with integrated speed evaluation (3 LED), has a
continuous signal delivered with the correct milling speed.
Process flow welding-milling exchanging:
General process flow:
The process Flow consists of several steps, each of which is set up and optimized for the
number of spot welds before each milling process which depends wear caused by the welding
task. In general, electrodes are to be reshaped after 50-200 weld spots based on optimum
running conditions. Reshaping of electrode pairs may be repeated approximately 20-50 times
before electrodes are replaced.
The general process flow is shown in Figure 6 For a better indication of cutter or blade life it is
recommended that milling be performed before replacing electrodes to in order to measure
the difference in weld face size can electrode quality. The process chain should be followed
for program routine of the PLC device and the robot controller.
Make sure there is no welding current flow during the
milling and electrode replacement cycles. It may damage
the device or components!