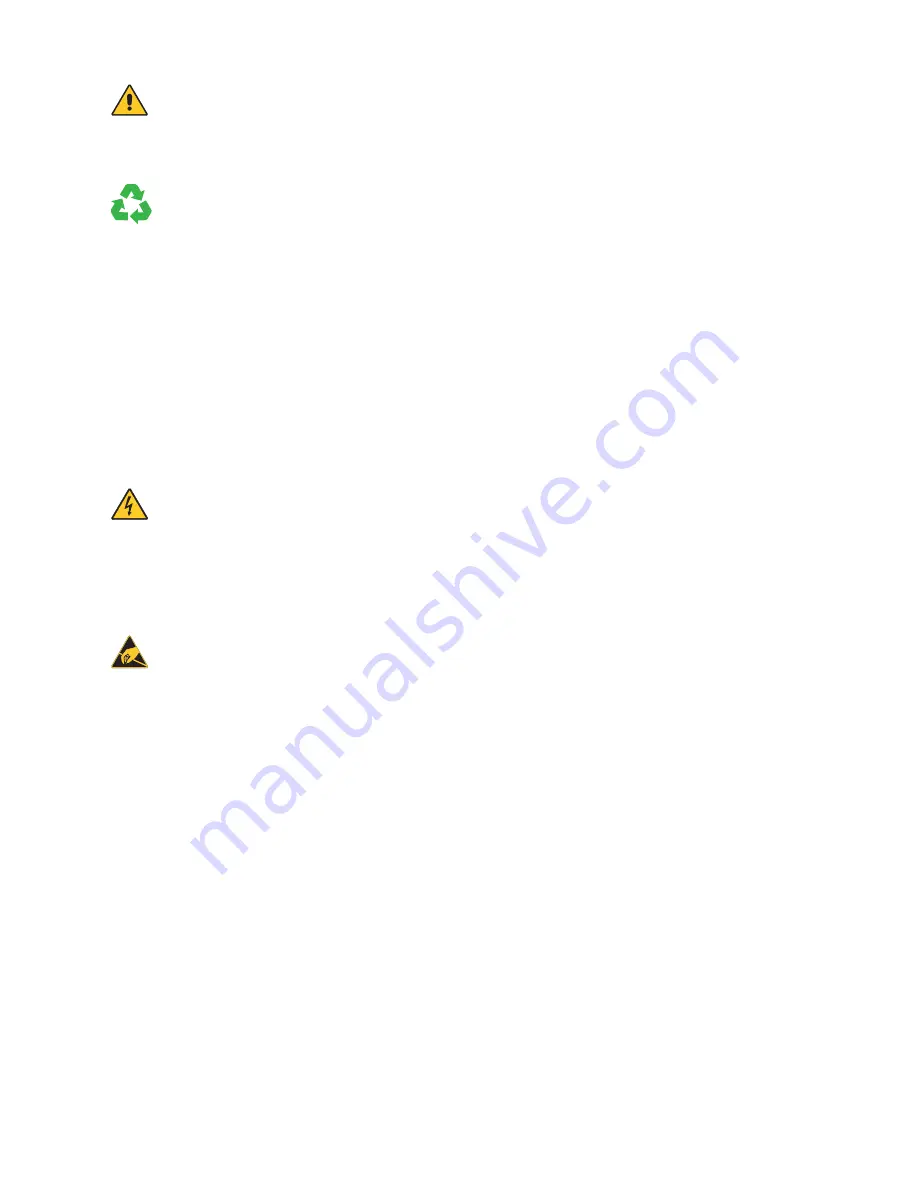
3
IP2159EN - 2017-06-12
1. General safety precautions
This installation manual is intended for qualified personnel only.
Installation, electrical connections and adjustments must be performed in accordance with
Good Working Methods and in compliance with the present standards. Read the instructions
carefully before installing the product.
Incorrect installation could be dangerous.
The packaging materials (plastic, polystyrene, etc.) should not be discarded in the envi-
ronment or left within reach of children, as they are a potential source of danger. Before
installing the product, make sure it is in perfect condition.
Do not install the product in explosive areas and atmospheres: the presence of inflammable gas
or fumes represents a serious safety hazard.
Before installing the motorisation device, make all the necessary structural modifications to
create safety clearance and to guard or isolate all the crushing, shearing, trapping and general
hazardous areas.
Make sure the existing structure is up to standard in terms of strength and stability. The mo-
torisation device manufacturer is not responsible for failure to observe Good Working Methods
when building the frames to be motorised, or for any deformations during use.
The safety devices (photocells, safety edges, emergency stops, etc.) must be installed taking
into account the applicable laws and directives, Good Working Methods, installation premises,
system operating logic and the forces developed by the motorised door.
The safety devices must protect the crushing, shearing, trapping and general hazardous
areas of the motorised door. Display the signs required by law to identify hazardous areas.
Each installation must bear a visible indication of the data identifying the motorised door.
When requested, connect the motorised door to an effective earthing system that complies with
current safety standards. During installation, maintenance and repair operations, cut off the
power supply before opening the cover to access the electrical parts.
The automation protection casing must be removed by qualified personnel only.
The electronic parts must be handled using earthed antistatic conductive arms. The manu-
facturer of the motorisation declines all responsibility if component parts not compatible
with safe and correct operation are fitted.
Only use original spare parts when repairing or replacing products.
The installer must supply all information on the automatic, manual and emergency operation of
the motorised door, and must provide the user with the operating instructions.
All the rights concerning this material are the exclusive property of Entrematic Group AB.
Although the contents of this publication have been drawn up with the greatest care, Entrematic Group AB cannot be held responsible in any way for any dam-
age caused by mistakes or omissions in this publication. We reserve the right to make changes without prior notice. Copying, scanning or changing in any way is
expressly forbidden unless authorised in writing by Entrematic Group AB.