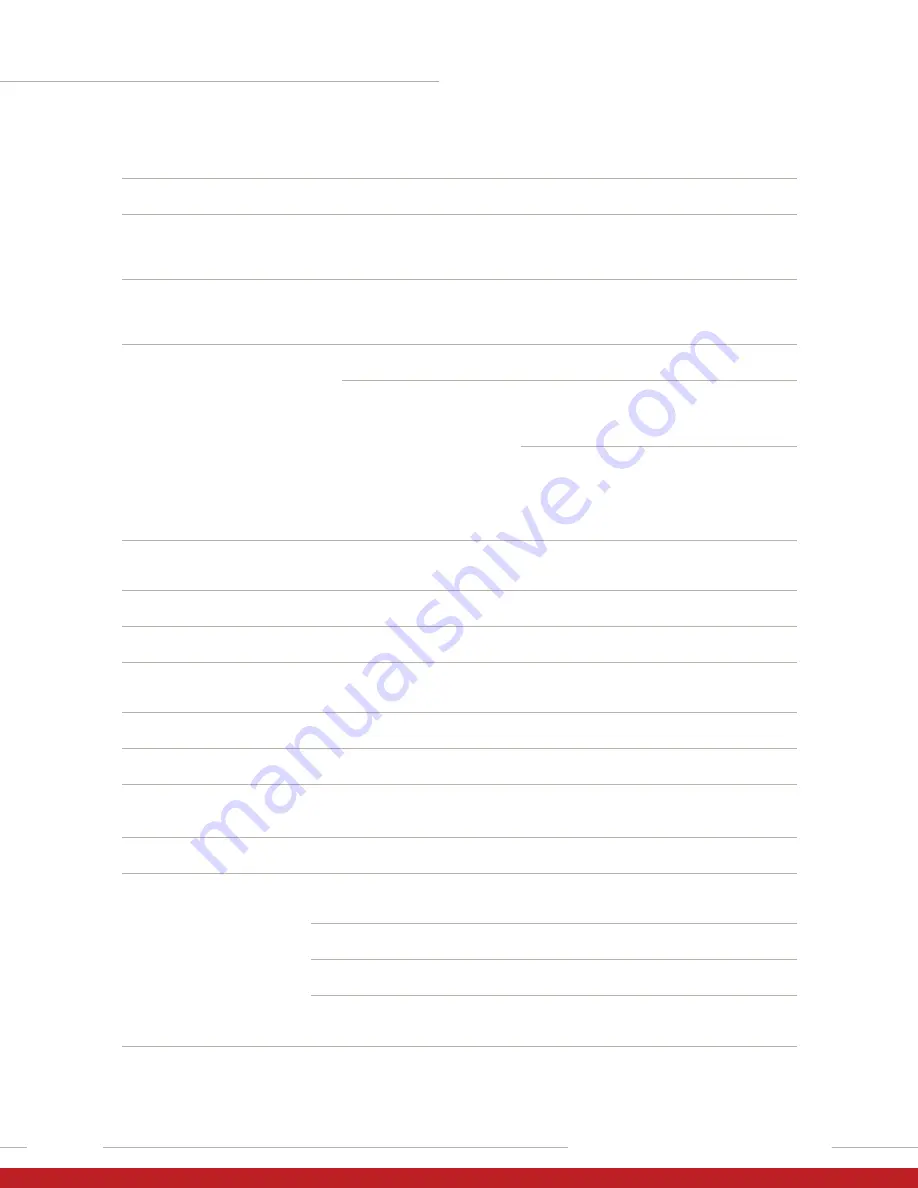
36
INTELLIGEN LV DISPENSE SYSTEM
Installation and Use Manual | Entegris, Inc.
Poor End of Dispense
SYMPTOM
PROBLEM
SOLUTION
Droplet hangs down or drips
External stop valve closing
too late or parameters require
adjustment
Close the valve earlier using the Outlet
Valve Control or suckback settings on
the Recipe page.
Fluid cuts off too high in the nozzle
External stop valve closing
too quickly
Close the valve later using the Outlet
Valve Control or suckback settings on
the Recipe page.
No suckback
Bubbles in dispense line
Ensure no bubbles in dispense line.
Inappropriate suckback
Ensure there is time for the chemical to
flow back. Higher viscosity chemicals
require longer time.
For new system start-up, start with the low
suckback rate and high suckback volume.
For example: 0.05 cc/s and 0.5 cc respectively.
This gives the chemical 10s to flow back.
Optimize the parameters accordingly.
High Particle Counts on Wafer
PROBLEM
SOLUTION
Filter media is too open
Use smaller pore size filter.
Filter not being fully wetted during
installation or priming
Perform multiple purge cycles using higher than normal filtration
to completely wet the filter.
Filter lifetime exceeded
Replace filter.
Contaminated or old photoresist
Drain, flush, and clean the entire system and fluid path.
Resist Thickness
SYMPTOM
PROBLEM
SOLUTION
Resist thickness non-uniform
Delay between end of dispense
and the final wafer spin
Correct wafer spin timing.
Nozzle not centered above wafer
Center nozzle.
Dried chemical on nozzle
Clean nozzle.
Nozzle too high or too low
above wafer
Adjust nozzle height. (Typically 6 to 9 mm
above wafer. Fluid viscosity dependent.)