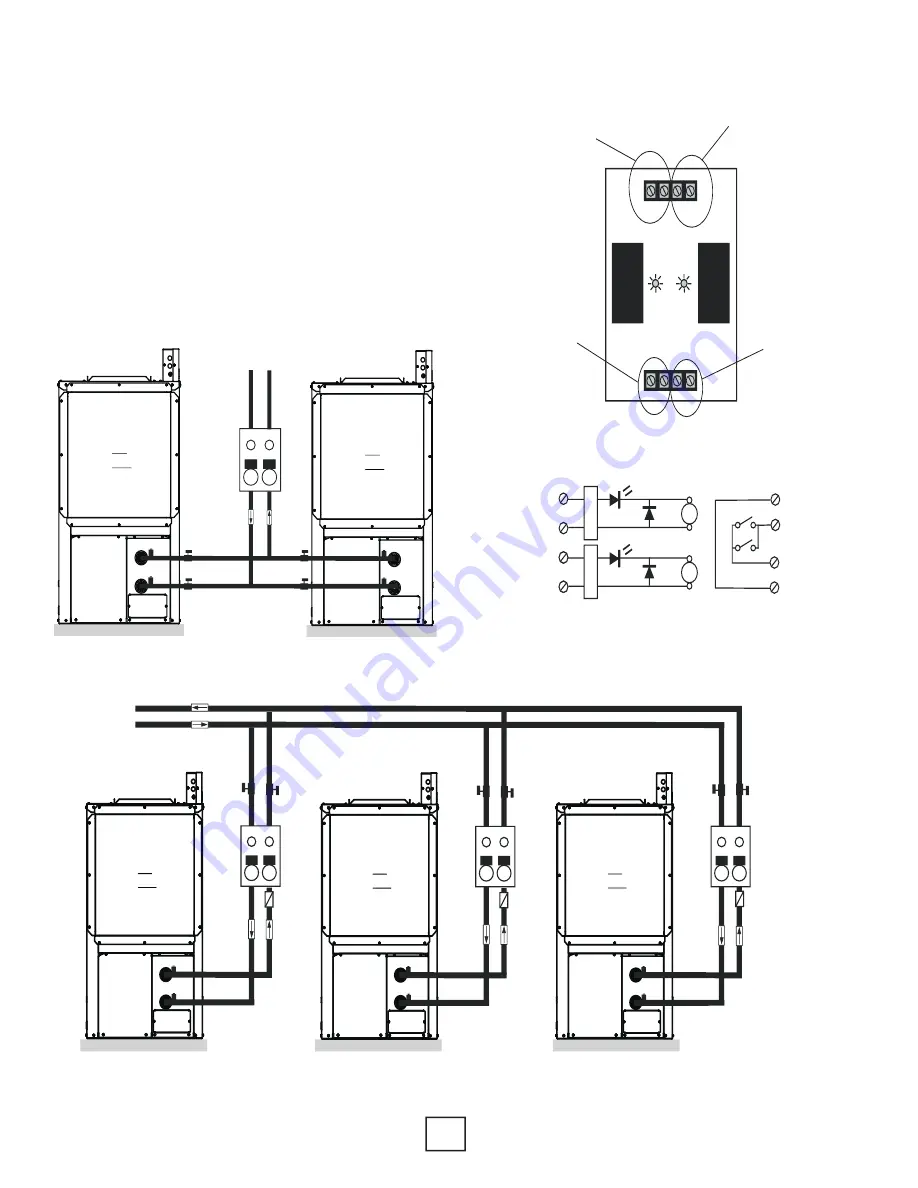
36
Enertech Global
IOM, BS/BT Models
Section 6: Unit Piping Installation
APSMA Pump Sharing Module
The pump sharing module, part number
APSMA, is designed to allow two units to share
one flow center. With the APSMA module,
either unit can energize the pump(s). Connect
the units and flow center as shown in the example
below. Figure 21 includes a schematic of the board.
The module must be mounted in a NEMA enclosure
or inside the unit control box.
Local code supersedes any recommendations
in this document.
Flow
Center
Hose
Kit
Loop Field
P/T Ports
air
coil
Source Out
Source In
P/T Ports
P/T Ports
air
coil
Source Out
Source In
P/T Ports
~
~
Shut O
ff
Valves
Shut O
ff
Valves
Equipment Pad
2” Polyethylene Foam
Equipment Pad
2” Polyethylene Foam
Single Shared Flow Center. Dual Unit Piping
Example:
Flow
Center
Loop Field
P/T Ports
air
coil
Source Out
Source In
P/T Ports
~
Shut O
ff
Valves
Flow
Center
P/T Ports
air
coil
Source Out
Source In
P/T Ports
Shut O
ff
Valves
Flow
Center
P/T Ports
air
coil
Source Out
Source In
P/T Ports
Shut O
ff
Valves
~
Check
Valve
Direction
of Flow
Check
Valve
Check
Valve
Direction
of Flow
Direction
of Flow
of Flow
Equipment Pad
2” Polyethylene Foam
Equipment Pad
2” Polyethylene Foam
Single Shared Loop Field, Individual Flow Center and Unit Piping Example
Drawing represents typical unit installation, connection location, type and appearance may differ per other
models
+
-
DC
Bridge
LED
Diode
RY1
24VAC input
from unit #1
+
-
Diode
RY2
24VAC input
from unit #2
RY1
RY2
240VAC input
240VAC to pump(s)
24VAC 24VAC
Figure 2: Board Schematic
240V IN 240V OUT
Relay
Relay
240VAC
Power Source
240VAC
to Pump(s)
24VAC
connection
to unit #2
(Y1 & C From Thermostat)
24VAC
connection
to unit #1
(Y1 & C From Thermostat)
Figure 21: APSMA Module Layout
Figure 22: APSMA Module Wiring Schematic