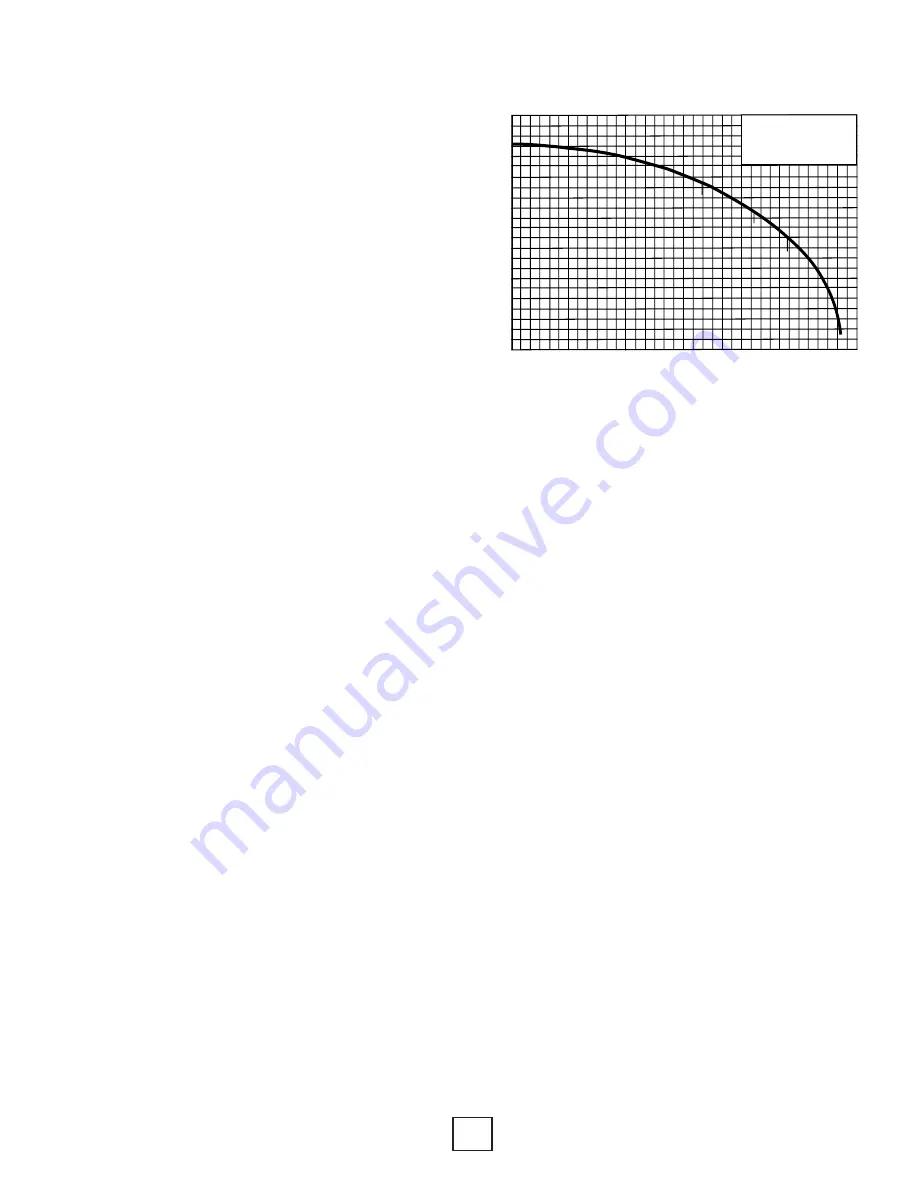
33
IOM, BS/BT Models
Enertech Global
•
It may be necessary to add some water into
the reservoir to keep the water level above the
return tee so that the solution does not foam.
•
The system must be run for 3 to 4 hours to mix
the antifreeze and water in the reservoir. The
fluid will not mix inside the loop.
•
Check the antifreeze level every so often to
insure that the proper amount was added to the
system (see antifreeze charging section).
Step 4: Final Pressurization of System
Once all of the air and debris has been removed,
and the antifreeze has been added and mixed, the
system is ready for final pressurization.
•
Turn one of the 3-way valves so that it is open
to all 3 ports, the unit, loop, and flush port. Turn
the other valve so it is only open to the loop and
flush port (pressure is also applied to the hose
kit in this arrangement).
•
Turn the flush cart pump on and allow the
system to start circulating.
•
With the pump running, turn the return line ball
valve to the off position on the flush cart, “dead
heading” the pump.
•
There should be a maximum of 1” to 2” inches of
drop in the water level in the reservoir. This only
takes about 3-5 seconds.
•
Next, turn the supply line ball valve to the off
position on the flush cart (isolates the flow
center from the flush cart).
•
Now that the system is isolated from the
reservoir the pump can be turned off. Do not
open the main flush cart ball valves yet.
•
Connect the water supply back to the discharge
line hose connection, and open the ball valve.
Turn on the water supply and leave it on for 20
to 30 minutes. This will stretch the pipe properly
to insure that the system will not have a “flat”
loop during cooling operation.
•
Once the loop is pressured (recommended
pressure on initial start up is 50 to 70 psi), turn
the water supply off. Turn off the discharge line
ball valve, and disconnect the water supply.
Maximum pressure should never
exceed 100
psi under any circumstance!
Section 6: Unit Piping Installation
0 10 20 30 40 50 60 70 80 90
CAPACITY - U.S. GPM
120
110
100
90
80
70
60
50
40
30
20
10
Total H
ead in F
eet
SUCTION LIFT
25’
20’
15’
Meyers QP-15
1-1/2 HP Self-Priming
Centrifugal Pump
Figure 19: Flush Cart Pump Curve
•
Turn the 3-way valves on the flow center back
to the normal operation mode, which closes the
flush port connections.
•
Open the ball valves on the flush cart to relieve
pressure on the hoses. Disconnect the hoses
from the flow center.
Note:
Pressurized flow centers and Grundfos UP
series pumps need a minimum of 3psi on the
suction side of the pump to operate. Maximum
operating pressure is 100 psi.
Loop static pressure will fluctuate with the
seasons. Pressures will be higher in the winter
months than during the summer months. In
the cooling mode the heat pump is rejecting
heat, which relaxes the pipe. This fluctuation
is normal and needs to be considered when
charging and pressuring the system initially.
Typical operating pressures of an earth loop are
15 to 50 psi.