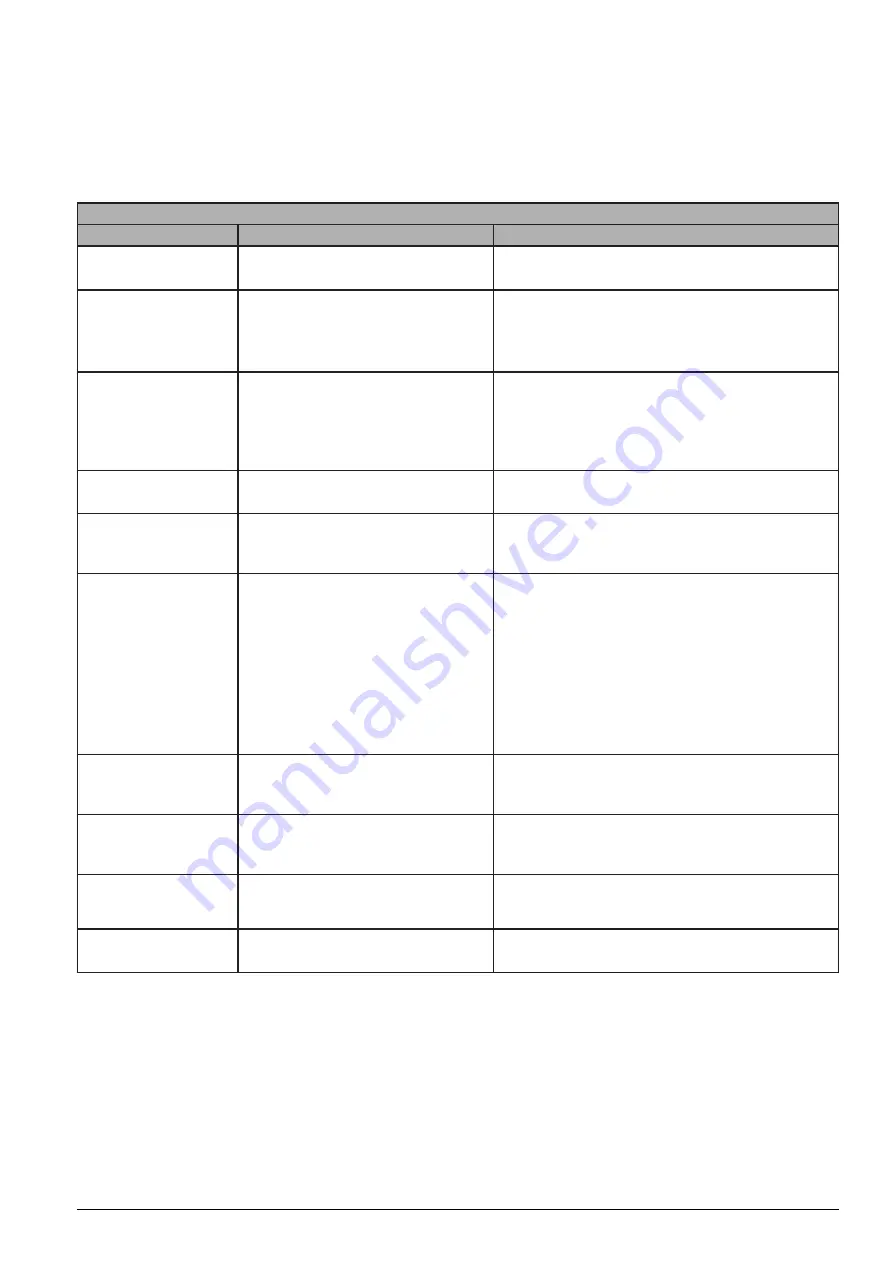
Doc
L4540
_a
25
11. ALARM GUIDE
Only qualified hydraulic technicians should service the
pump or system components. To determine the cause
of the problem, the complete system must be included
in any diagnostic procedure.
Refer to the alarm chart for a list of alarms and possible
causes. The alarm chart is not all-inclusive, and should
be considered only as an aid to help diagnose the most
common problems. For repair service, contact your
local Authorized Enerpac Service Center.
ALARMS CHART
ALARM
POSSIBLE CAUSE
SOLUTION
Safety Stop: Control
Cabinet
• Safety Stop is activated.
• Deactivate Safety Stop button.
• Reset alarm.
Stop Tolerance
Exceeded. Reset
Relative Positions
• The difference between Relative
Positions of selected cylinders
is bigger than “Work Tolerance”
parameter.
• Review the Relative Positions of selected
cylinders.
• Reset the Relative Positions.
• Reset alarm.
Maximum Total Load
• The system has reached to the
parameter typed Maximum Total
Load.
• Check if the Maximum Total Load parameter is set
correctly.
• Check if the Load is blocked in the motion.
• When the root cause has been checked and
solved, reset alarm.
Motor OFF.
• The motor is switched off when is
trying to carry on a movement.
• Switch On the motor on the EVOP electric cabinet.
• Reset alarm.
Impossible To Start Tilt-
ing. All Values Must Be
Others Than 0
• The value typed in the delta
position of each cylinder is zero.
• Type a delta position different than zero or deselect
the cylinder to be moved.
• Reset alarm.
Maximum Cylinder Load
• The pressure of the cylinder has
exceeded the value entered in
the “Maximum Cylinder Load”
parameter.
• Check the parameter, considering the load weight
and the cylinder characteristics. If it is incorrect,
change it.
• Check “Effective Area” and “Pressure” spans. If
one of them is incorrect, change it.
• Reset alarm. The alarm can only be reset by
adjusting the load alarm parameter or by reducing
the actual load on the cylinder using manual
mode. Take care when using manual mode to
avoid injury or death.
Cylinder Stroke Signal
Failure
• The stroke sensor signal of the
cylinder is not reaching to the PLC.
• Visually check the position transducer and the
cable.
• Reset alarm.
Cylinder Absolute Sen-
sor Position Value Below
Lowest Admissible Limit
• The stroke sensor associated to
the cylinder is not extended or
connected to the load or the plunger.
• Extend the stroke sensor wire and connect it to
the element to be moved.
• Reset alarm.
Cylinder Pressure Signal
Failure
• The pressure transducer signal
of the cylinder is not reaching the
PLC.
• Visually check the pressure transducer and cable.
• Reset alarm.
Safety Stop: Single Syn-
chro Control
• Safety Stop is activated
• Deactivate Safety Stop button.
• Reset alarm.