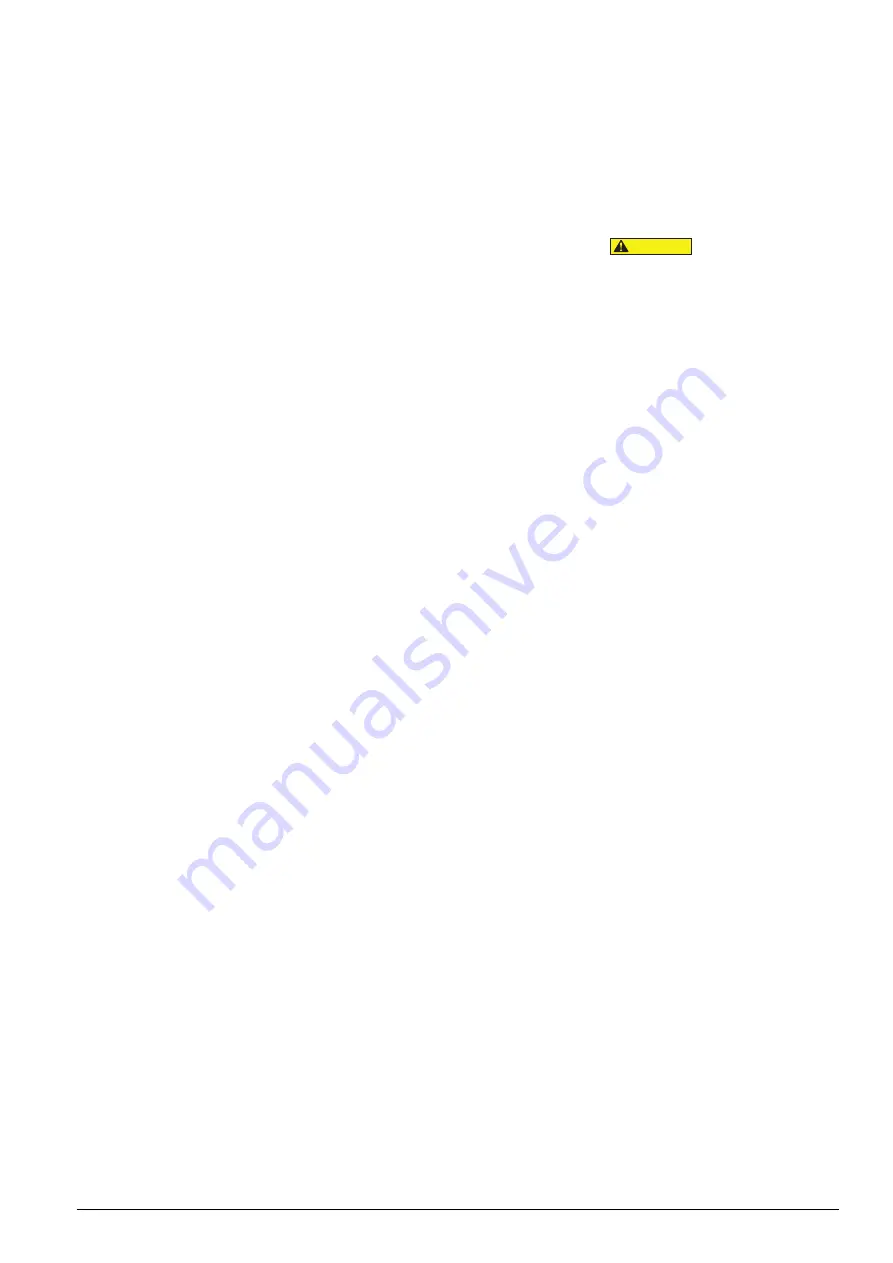
Doc
L4540
_a
5
• Loose or cross threaded fittings can be potentially
dangerous if pressurized. Never stand directly in line
with any hydraulic connection while pressurizing.
• Never strike the equipment while it is pressurized
or moving load. Components under tension may
become dislodged, allowing them to become
dangerous projectiles. Uncontrolled release of
pressurized hydraulic oil could also occur.
• Avoid striking the equipment at any time, even when
it is not pressurized or moving load. Striking the
tools could cause permanent damage to system
components and may affect its functioning.
• Be certain that no persons are working on or near
any tool before moving of the load begins. Alert all
personnel in advance that the procedure is about
to occur.
• Always maintain communication with the operator
during procedure to avoid accidents. Use hand
signals, two- way radios or other appropriate forms
of communication (as required by applicable laws and
regulations) if the load is not visible to the operator.
• Operate Pum per Point Lift System (EVOP) as
required to ensure that the load is moved evenly
and at a controlled rate.
• Closely watch the load at all times during operation.
Stop work immediately if the load becomes
unstable or appears to be moving unsteadily.
• Immediately replace worn or damaged parts.
Use only genuine Enerpac parts from approved
distributors or service centers. Standard grade
parts will break causing personal injury and
property damage. ENERPAC parts are designed to
fit properly and withstand high loads.
• To minimize risk of personal injury keep hands
and feet away from the tool and workpiece during
operation.
• High voltage is present inside the pump even when
motor is off. Always be certain that the pump is
stopped and disconnected from AC power supply
before performing any inspection, maintenance or
repair procedures.
• Do not leave the pump unattended in the workplace
when connected to AC power supply. Take all
reasonable precautions to avoid unauthorized use.
• Take precautions so that the pump is not switched
on accidentally.
• If it is not possible to unplug the pump power
cord from the AC power outlet, the power must be
turned off and locked out at the AC power supply.
• Always disconnect the pump from AC power
supply before transporting it.
• Do not unplug the pump by pulling on the cord. To
unplug, grasp the plug, not the cord.
• If the cord and/or plug are damaged, do not
connect the pump to a live electrical outlet. Repair
or replace the damaged items as required and be
sure the grounding conductor is properly wired
before reconnecting the pump to the outlet. Consult
a qualified electrician if grounding conductor
wiring procedures are not completely understood
or if there is any doubt as to whether the pump is
properly grounded.
• Do not modify the plug provided with the pump.
If the plug will not fit in the outlet, have a proper
outlet installed by a qualified electrician.
• If the pump must be reconnected for use on a
different type of electric circuit, the reconnection
should be made by a qualified electrician. After
the reconnection, the pump should comply with all
local codes and ordinances.
Failure to observe and comply with the following
precautions could result in minor or moderate
personal injury. Property damage could also occur.
• Ensure components are protected from external
sources of damage, such as moving machine parts,
sharp edges, weld spatter, corrosive chemicals
and excessive heat or flame.
• Keep hydraulic equipment away from flames and
heat. Excessive heat will soften packings and
seals, resulting in fluid leaks. Heat also weakens
hose materials and packings.
• For optimum performance, do not expose hydraulic
equipment to temperatures of 150˚F [65˚C] or
higher. Protect all hydraulic equipment from weld
spatter.
• To prevent damage to pump electric motor, check
specifications. Use of incorrect power source will
damage the motor.
• Do not use electric pumps in an explosive
atmosphere. Adhere to all local and national
electrical codes. A qualified electrician must do
installation and modification
• Protect hoses and cylinders from weld spatter.
• Avoid damaging the hydraulic hose. Avoid sharp
bends and kinks when routing hydraulic hoses.
Using a bent or kinked hose will cause severe
backpressure. Sharp bends and kinks will internally
damage the hose leading to premature hose failure.
• Do not drop heavy objects on hose. A sharp impact
may cause internal damage to hose wire strands.
Applying pressure to a damaged hose may cause
it to rupture.
• Do not lift hydraulic equipment by the hose or
couplers. Use the lifting handles provided on
cylinders and clamp assemblies.
• Do not pull on a hose that is connected. If pulling
forces are exerted on a hydraulic coupling the hose
and coupling interface will weaken which may
result in the hose bursting out of the coupling.
• Always lift a hose by the hose itself, whilst
supporting the coupling.
• Do not handle pressurized hoses. Escaping oil
under pressure can penetrate the skin, causing
serious injury. If oil is injected under the skin, see a
doctor immediately.
• During assembly the hose must be supported by
necessary use bend guides to prevent twisting of
the hose.
• Change worn or damaged hoses immediately.
• Do not use dirty or corroded couplings.
CAUTION