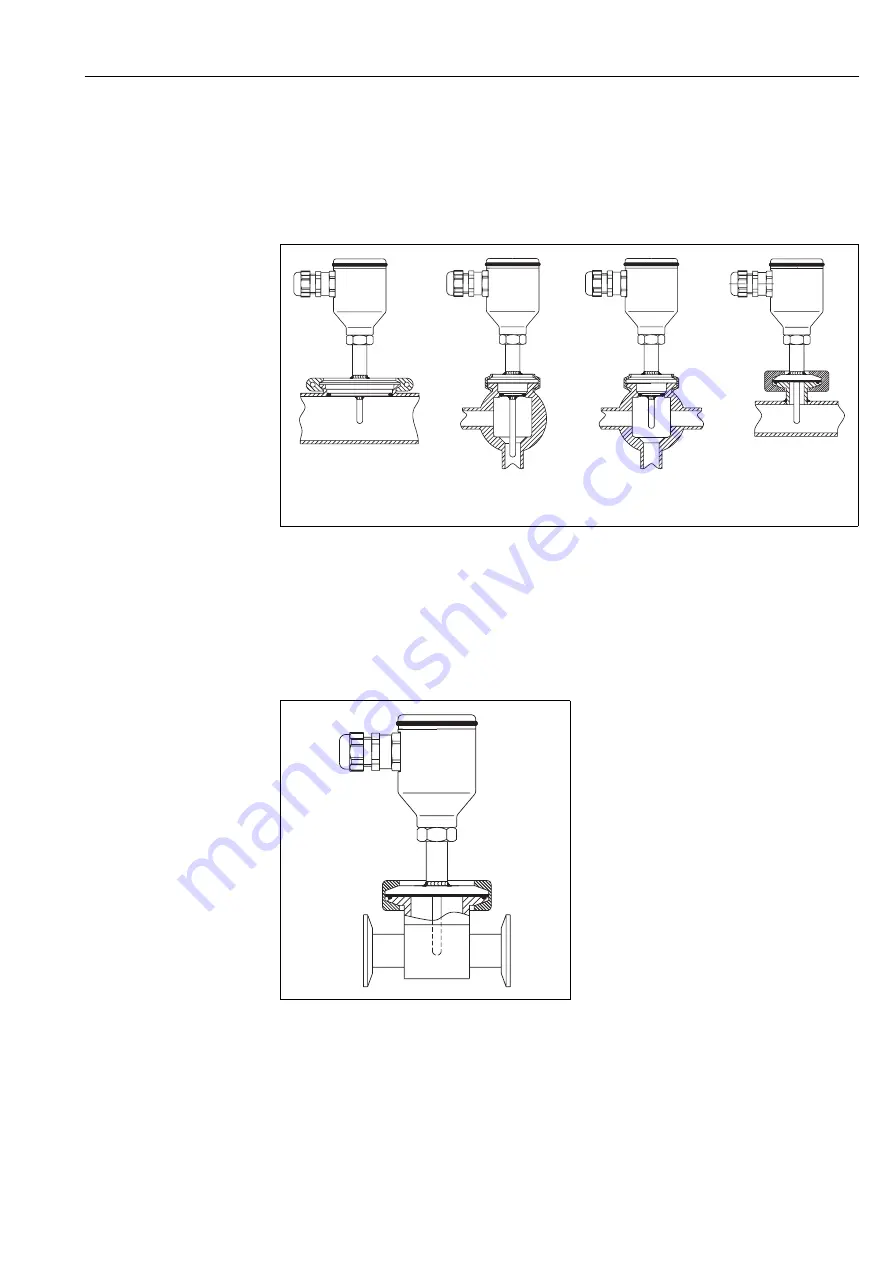
omnigrad MTR 44, TR 45
Hauser
5
Suitable solutions for the installation of the sensors in small pipes are shown in figure 3.
In hygienic applications, a good, strict, installation rule consists in not to leave any dead spaces along the flow
of the process fluid.
The required flush-mounting can be achieved by the connection Varivent
®
, G1" Liquiphant M type (+ purpose
built adaptor).
The clamp flanges can also partly fulfil this requirement, if the Tri-Clamp
®
components 7IMPS or TL7IWWMS
(Instrument Tees) are used (see the related figure 4).
Fig. 3:
Installation solutions in small pipes
For other connection arrangements, the diagram in figure 2 should be followed [h <= d/2].
For weld-in connections, care should be taken by the user in the execution of the welding on the process side
(suitable weld material, welding radius > 3 mm, absence of pits, folds, crevices, …).
The use of purely threaded, Ingold and metal-to-metal joints is not recommended by some hygienic design
standards (i.e. 3-A
®
Standard 74-02 and Document 8 from EHEDG). This is the reason why E+H Temperature
division doesn't suggest those solutions in "sanitary" applications. Moreover often metal-to-metal couplings can
only be used effectively once.
Regarding corrosion, the basic material of the wetted
parts (SS 316L/1.4435) is capable to tolerate com-
mon corrosive media up to high temperatures.
When disassembling the sensors, new gaskets equiv-
alent to the originals and specific torques must be
employed for the re-assembling procedure. This will
ensure the stated IP (Ingress Protection) grade of the
enclosures.
To avoid problems due to condensation when the
ambient has a high humidity rate and the process is at
a low temperature, a plastic housing (i.e. model
TA20B) can be an effective choice.
Fig. 4:
Installation with the Tri-Clamp
®
component 7IMPS
Varivent D=50 mm
for pipes DN25
Varivent D=31 mm
for pipes DN10/15
Microclamp
or miniclamp