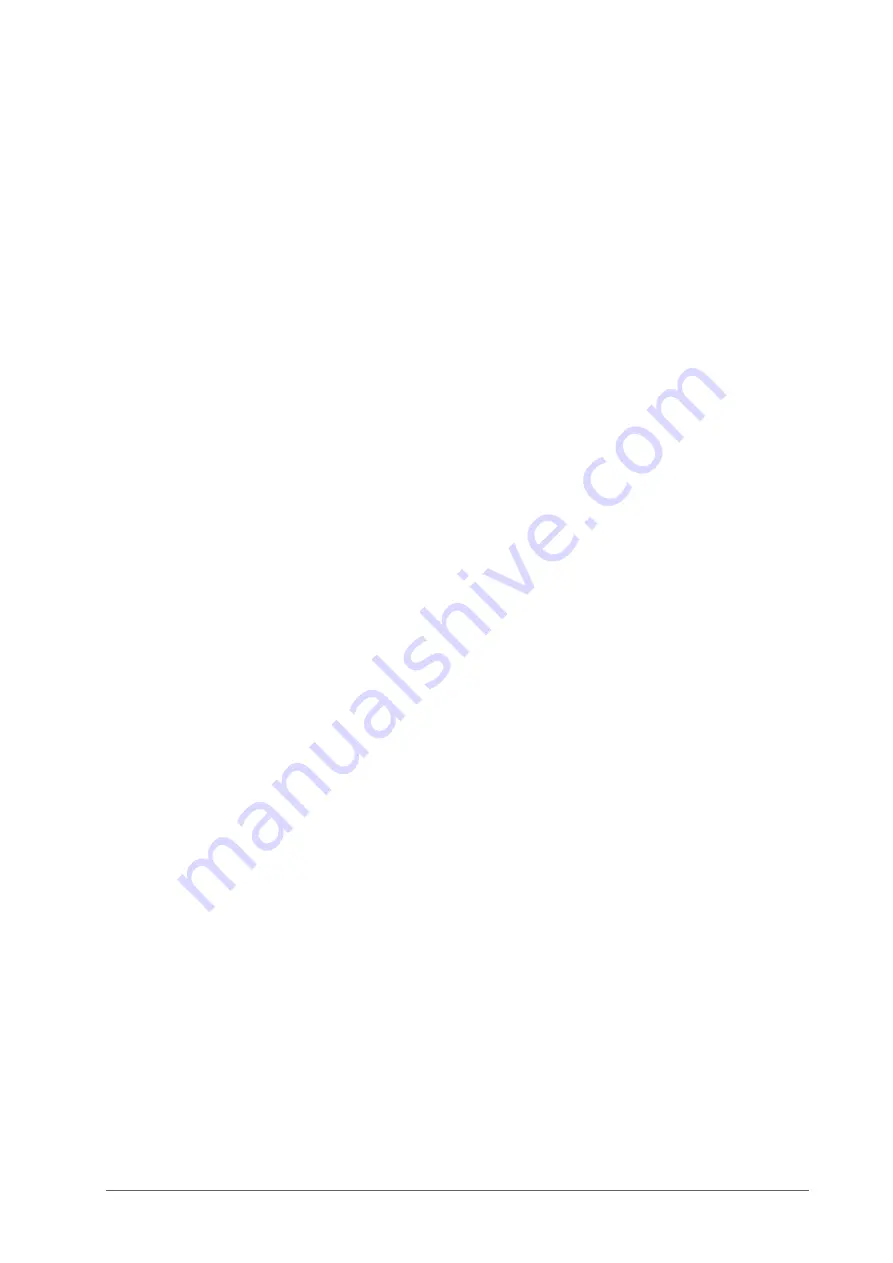
Users’ Manual
EDI-53 Series Digital Indicator
Page
|
8
signal with a resolution of 0.1 mV or 100 micro volts.
The EDI-53P measures the output of potentiometric displacement transducers which is of the order of 2
V at full scale.
The EDI-53I measures the output of 4 – 20 mA current loop output transducers. The transducer current is
changed to a corresponding voltage using a precision input resistor of 50.0 ohms. The resistor converts
the 4 – 20 mA signal to a corresponding 0.2 – 1.0 V signal that is then measured by the ADC.
The EDI-53L measures the output of the load cells which have an output rating of 1 mV/V to 3 mV/V at
rated load. As the EDI-53L provides an excitation voltage of 5 V, the load cell output correspondingly is
between 5 mV to 15 mV at full load. This voltage is very small to be reliably measured by the ADC
directly. A precision low drift preamplifier with a gain of 100 is used to amplify the load cell output signal
100 times before it is measured by the ADC. ADC input correspondingly sees a signal between 0.5 V to
1.5 V DC at its input.
3.3
Calculation of parameter value in engineering units.
In the ‘VOLTS’ mode, the ADC in the EDI-53 indicator displays the value of the voltage present at its
input directly in volts on the display. This value is then used to calculate the value of the measured
parameter in proper engineering units. Although the EDI-53 can do the required calculation automatically,
it requires some additional information for each transducer for which it has to calculate the parameter
value in engineering units.
For most transducers the transducer manufacturer will normally provide a figure called the gage factor of
the transducer. The gauge factor is used to convert the measured transducer output value to
corresponding transducer input value in engineering units.
Most transducers that will be used with the EDI-53 will have a non-zero output with zero input (i.e. when
the value of the measured physical parameter is zero). This is known as the zero or offset reading of that
particular transducer. This value is supplied by the manufacturer of the transducer in the transducer
calibration sheet or can often be easily determined at the time of installation.
The gage factor and the offset value for each transducer that will be monitored by the indicator has to be
entered in the memory of the EDI-53 indicator before it can display the measured value in engineering
units. This process is called ‘setup’ and is discussed in more detail in section 5 on setup.
The EDI-53 uses the following equation to calculate the value of the measured parameter in applicable
engineering units.
Y = G (R
1
– R
0
) [Eqn. 3.3.1]
Where, Y is the value of the measured parameter in engineering units, G is the gage factor of the
transducer, R
0
is the reading in volts shown on EDI-53 display with zero input, and R
1
is the current
reading (reading during measurement) in volts on the indicator display. The gauge factor G may be
different from the gage factor supplied by the manufacturer and may need to be recalculated as
explained below.
EDI-53P
: For model EDI-53P the gauge factor G is specified as mm/Volts. If the gauge factor is specified
by the manufacturer in terms of V/mm the inverse of the gauge factor should be used.
EDI-53L
: Model EDI-53L indicator is for use with load cells. The load cell rated output, M, is generally
specified in terms of mV/V for rated capacity L. The value of G should be calculated as
G = 2L / M
[Eqn. 3.3.2]
EDI-53I
: For Model EDI-53I the calculation of gauge factor is more involved. 4 – 20 mA output
transducers have a non-zero output (4 mA) with zero input. Sometimes the transducers are provided with
Rev. 1a