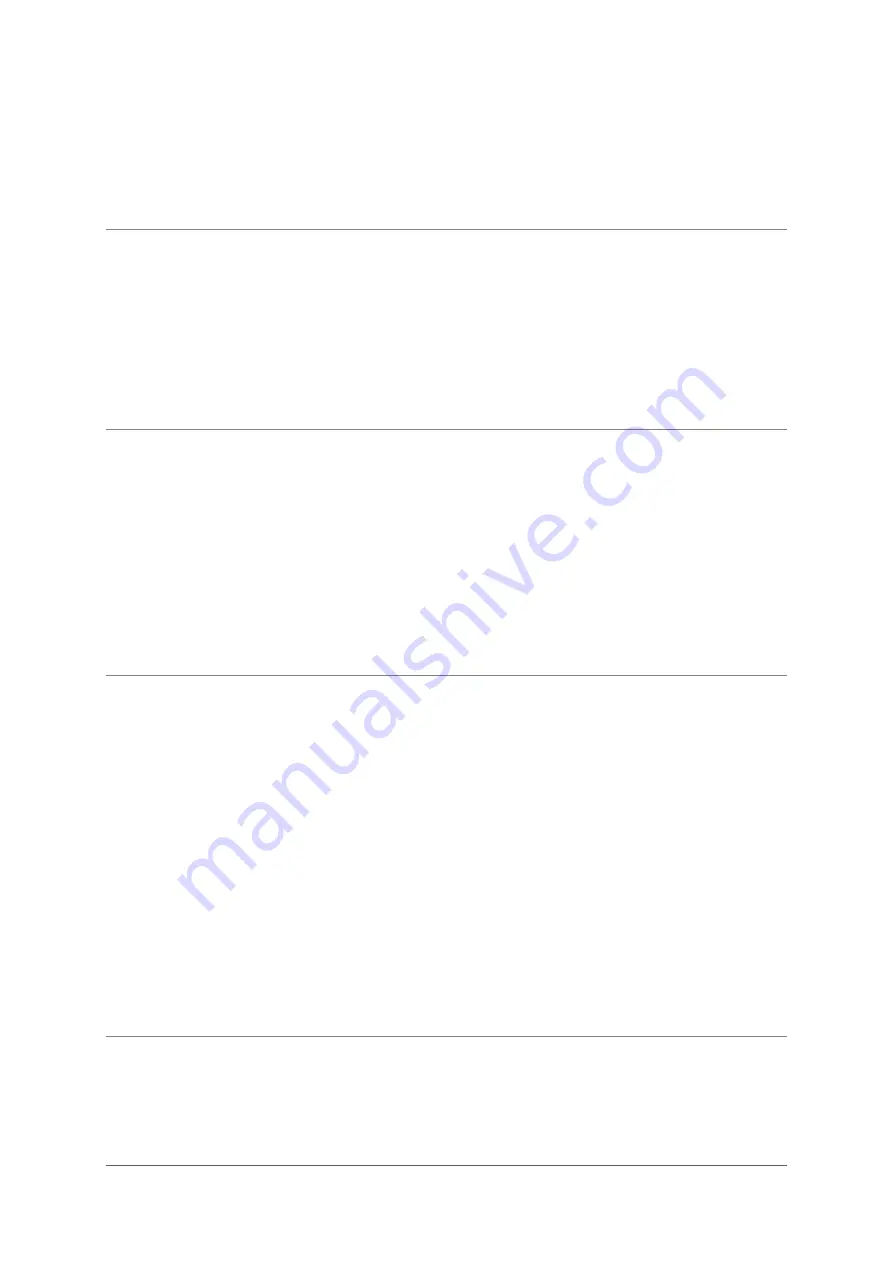
Addendum to User’s Manual
EDI-53 Series Digital Indicator
Page
| 1
Addendum
Model EDI-53S-350 Digital Indicator for 350 Ohms Quarter Bridge Resistance
Strain Gage type sensor
1
INTRODUCTION
The EDI-53S-350 is a modified version of Encardio-rite’s EDI-53L indicator. It contains internal bridge
completion network for measurement of 350 Ohms foil resistance strain gauge output in a quarter
bridge configuration. Except for the differences described below, the EDI-53 Series Digital Indicator
User’s Manual [ER document No. WI-6002.67 Rev. 0] is valid for all other operations and technical
specifications of this indicator. The section numbers given below refer to the original section numbers
of the User’s Manual.
2
TRANSDUCERS
The EDI-53S-350 is designed for measurement of strain using two wire 350 Ohms resistance strain
gages in a quarter bridge circuit. The other 3 precision 350 Ohms bridge completion resistors are
provided inside the indicator.
Quarter bridge measurement technique introduces a non-linearity error that increases with the
measured value. Although the indicator can work with strain gages of any gauge factor, its calibration
is optimised to work with strain gages with a gage factor of around 2 and a measurement range of
±
3000 micro strain to minimize non-linearity errors. The indicator, however, is suitable for
measurement of up to
±
5000 micro strain at a nominal gage factor of 2.
3
MEASUREMENT OF TRANSDUCER OUTPUT
The 350 Ohms measurement bridge formed by the external strain gage and the three internal 350
Ohms resistors is excited using a 5 V excitation supply. The strain gage value (output) can be
displayed either as bridge voltage output multiplied by 100 in Volts or in engineering units if the gage
factor and the initial offset values have been programmed using one of the available channels in
setup. The symbol for micro strain cannot be displayed on the display, so the units position remains
blank.
3.1
Calculation of parameter value in engineering units
The EDI-53S-350 uses the following equation to calculate the strain value sensed by the strain gage.
S = Vop
×
(8000
÷
G)
[Eqn. 3.3.4]
where, S is measured strain value in micro strain, G is gage factor as supplied by the strain gage
manufacturer, and Vop is the bridge output voltage as indicated by the EDI-53S-350 indicator in
‘VOLTS’ mode.
4
TAKING MEASUREMENTS
As the EDI-53S-350 is intended for use with two wire resistance strain gages, only the red and black
input signal leads terminated with yellow clips are used for measurement. The signal leads are
polarity insensitive so any input lead can be connected to any of the two strain gage terminals.