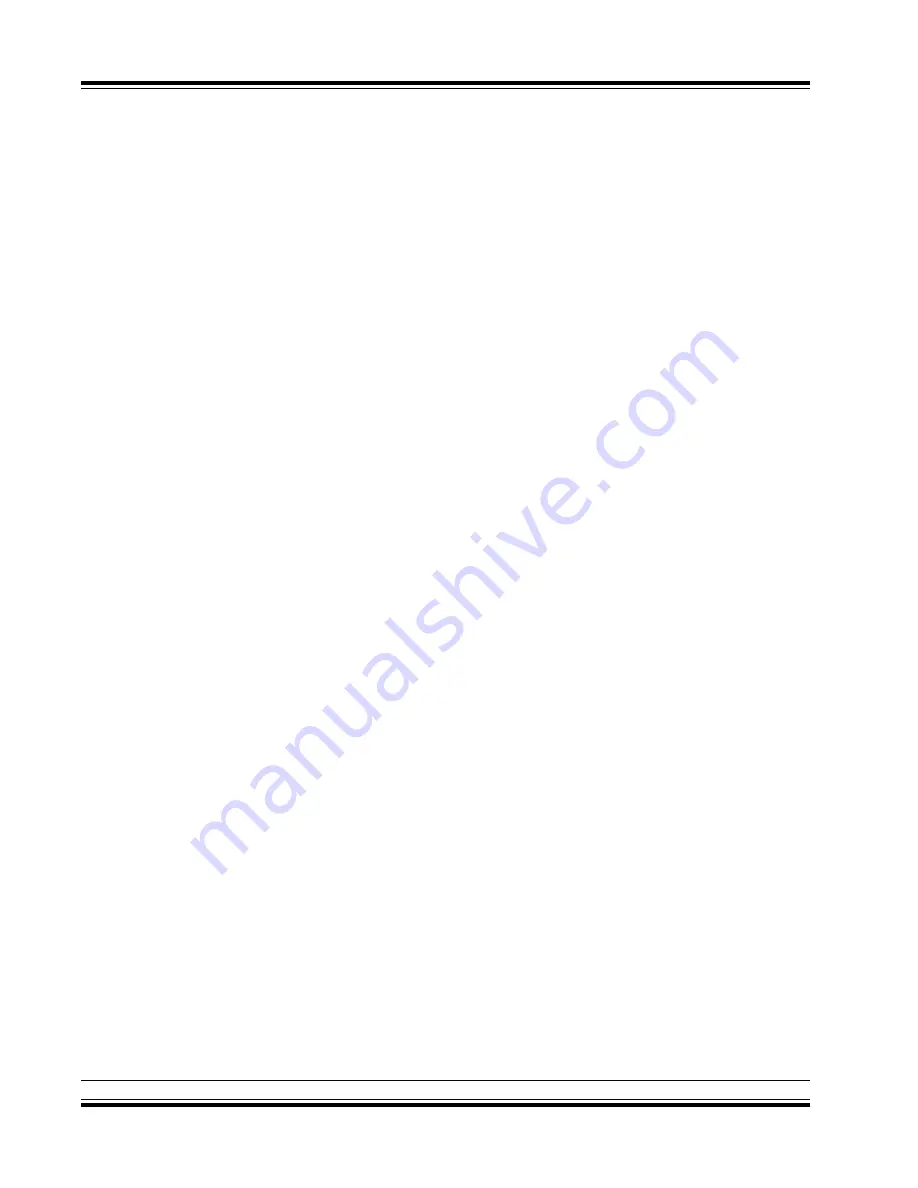
2
EMI Products are subject to ongoing development.
Products & Specifications may change without notice.
tween multiple condensers for ease of service and to
ensure adequate air flow to each unit. Air recircula-
tion can cause high system pressure that could lead to
compressor failure.
Adequate clearance between units is important. If
units are installed too close together, air flow is re-
stricted and this can result in premature compressor
operation or performance problems and failure.
Heat pump models will produce condensate in the
heating mode that will cause water to drain from the
base. When temperatures are below freezing, this wa-
ter becomes ice.
Consider possible icing when installing unit(s) near
sidewalks or walkways.
Heat pumps require airflow clearance in the winter
for heat mode and should be mounted above the level
of maximum anticipated snowfall.
MAXIMUM RANGE VS. LIMITED RANGE
HEAT PUMPS
EMI manufactures 2 types of heat pumps that have
different operating characteristics.
A maximum range heat pump is a standard unitary
industry-style heat pump that utilizes hot gas defrost (reverse
cycle) for continuous heating operation at low ambient
temperatures. Utilization of a solid state defrost board,
defrost termination switch, and an outdoor ambient sensor
assists the EMI maximum range heat pump to operate as
designed and tested in mechanical heating mode.
The EMI SHC 09-36 & CHD 42/48 single zone
series are the maximum range heat pump units that are
presently produced.
The SHC/CHD condenser utilizes a reversing valve
to provide reverse cycle operation. This means that the out-
door unit can act either as a condenser or an evaporator,
thereby providing either comfort cooling or heating to the
indoor space. The reversing valve is energized in cooling.
Therefore, should the valve fail to actuate, the system will
still provide indoor heat.
To check for reversing valve operation, place a jumper
wire across terminals R and O. You should hear a
click to verify that the solenoid is energizing and ac-
tuating the valve.
To check for compressor and condenser fan opera-
tion, place a jumper wire across terminals R and
Y. This will energize the contactor, providing power
to the compressor and condenser fan.
NOTE:
If the SHC condenser is equipped with
low ambient
fan control for cooling, The fan
will remain off (while in cooling mode) until
the condenser pressure reaches 275psi. The
fan will then energize and run until the
condenser pressure falls below 210psi. This
will happen only in the cooling mode (or when
the reversing valve is energized). In heating
(reversing valve not energized), the fan will
run continuously so long as the connection is
made between R and Y.
D
EFROST
C
ONTROLS
WITH
S
HORT
C
YCLE
P
ROTECTION
The SHC condenser is equipped with a logic control
circuit designed to keep the system operating at peek effi-
ciency. The 24v circuit provides control to the indoor and
outdoor systems along with 3 minute anti-short cycle com-
pressor protection.
The defrost control circuit is designed to keep the con-
denser coil free from ice and frost during heating mode. This
is accomplished through the precise switching of the out-
door fan, reversing valve, and indoor auxiliary heater.
D
EFROST
I
NITIATION
The defrost-sensor is located on either the end plate
or the return bend of the condenser coil. A defrost cycle will
initiate after the sensor closes (approx. 20° F) and remains
closed for the length of time selected on the control board
(Factory setting is 60 minutes for SHC 36 or 90 minutes for
SHC 9-30).
During defrost, the condenser will cycle the reversing
valve and enter a cooling mode. The condenser fan will also
switch off, allowing pressure and temperature to build in
the condenser coil, thereby melting off any ice buildup. At
the same time, the indoor electric heat will energize to
dampen the cold air being discharged from the evaporator
unit. This will continue until either the defrost-sensor opens
(approx. 60° F) or 10 minutes has elapsed. Defrost times
will vary depending on outdoor temperature and moisture
conditions. When defrost is complete the unit will resume
heating.
T
ESTING
D
EFROST
O
PERATION
USING
TEST
PINS
Defrost operation can be checked using the test pins
located on the circuit board of the condensing unit. Defrost
Test Operation will be a time-compressed version of the
actual defrost cycle.
With the system off and using two small alligator
clips, jumper the following sets of test pins:
R and DF2
and
DFT TST
Place the indoor unit in heating mode with the set point
temperature well above room temperature to ensure that the
condenser remains on during the entire defrost test operation.
The condenser will operate in heating for