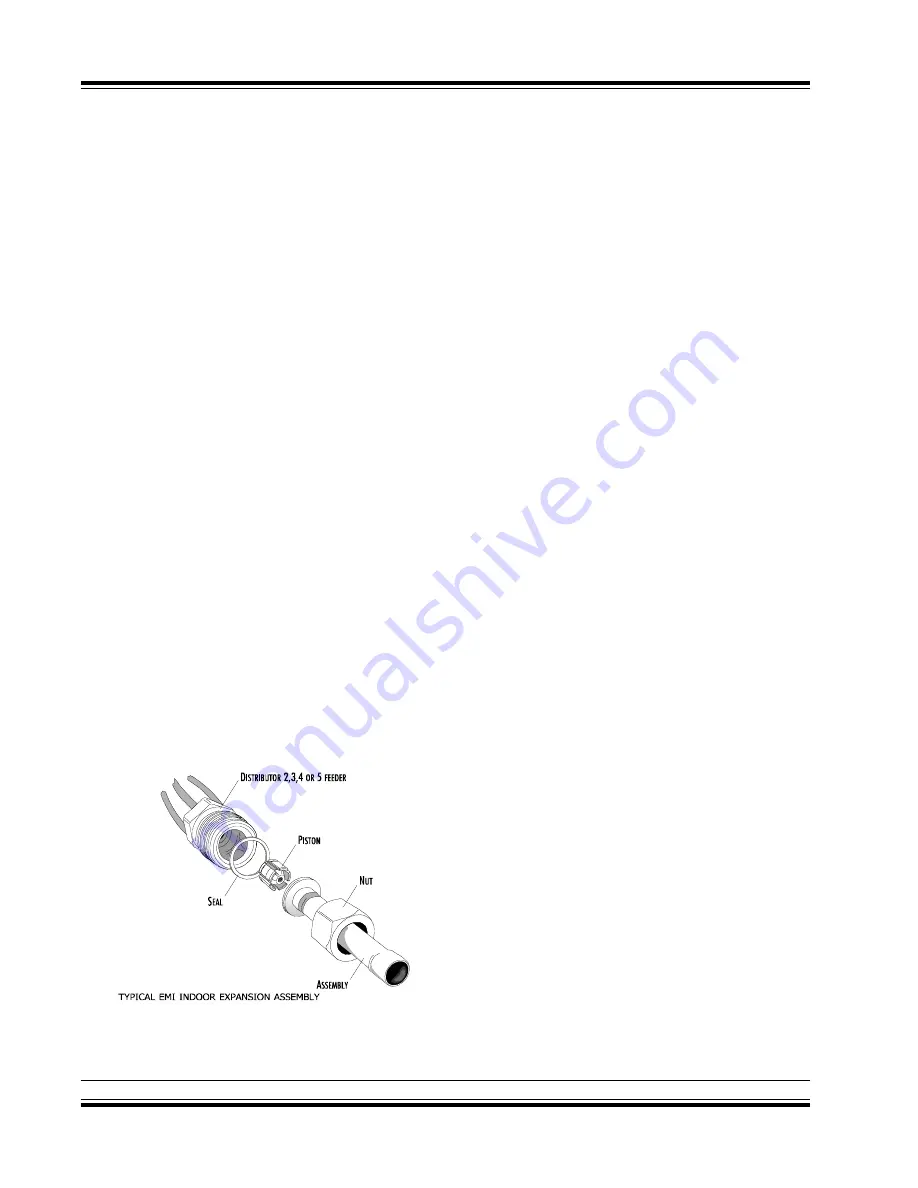
6
EMI Products are subject to ongoing development.
Products & Specifications may change without notice.
COMPRESSOR REPLACEMENT
Before replacing the compressor, test it to make sure
it is defective. Check the complete electrical system to the
compressor and its internal electrical system to be sure that
it is not out on internal overload. Reset the manual high pres-
sure switch (if equipped with one).
A complete evacuation of the system must be made
whenever you have a defective compressor or suspect it may
be. If the compressor has been operating for some time, a
careful analysis must be made to determine why the com-
pressor failed.
Many compressor failures are caused by the fol-
lowing conditions:
Poor initial installation of the system.
Changes to the system after installation.
Improper airflow over the evaporator.
Overcharged refrigerant system causing liquid to be
returned to the compressor.
Restricted refrigerant system.
Lack of lubrication (horizontal and excess tubing
must be sloped towards the compressor).
Lack of p-traps in risers.
Liquid refrigerant returning to compressor causing
oil to be washed out of bearings.
Non-condensables such as air and moisture in the
system. Moisture is extremely destructive to a refrig-
erant system.
Acid present in a sealed system.
R
ECOMMENDED
P
ROCEDURE
FOR
C
OMPRESSOR
R
EPLACEMENT
Perform all necessary electrical and refrigeration tests
to be sure the compressor is actually defective before
replacing the compressor.
Be sure power source is off and disconnect all wir-
ing at compressor.
Capture (reclaim) all refrigerant.
After all refrigerant has been captured, disconnect
suction as discharge lines from the compressor and
remove compressor. Be certain to have both suction
and liquid line gauge ports and/or process tube open
to atmosphere.
Disconnect both liquid and suction line connections
at the unit and inspect inside the fittings for any for-
eign particles that may have collected there. (The for-
eign particles can consist of pieces of valves, wind-
ings, or thermal overload particles, and other related
items normally located within the compressor shell.)
If any foreign particles are present, they must be re-
moved.
Carefully capture a small amount of oil from the de-
fective compressor by pouring from the compressor.
NOTE:
It is not possible to pour oil from a
rotary type compressor. On rotary compressor
systems, oil must be collected from the system
tubing after properly recapturing refrigerant.
Use an acid test kit (one-shot or conventional kit) to
test the oil for acid content according to the instruc-
tions with the kit.
If any evidence of a burnout is found, no matter how
slight, the system should be flushed with nitrogen.
Replace the liquid line filter drier if you have a com-
pressor burnout. It is recommended that the next larger
filter drier be installed and a suction filter drier be
added, following instructions in the filter drier sec-
tion.
REMEMBER:
Remove the suction line drier
after a few days of continuous operation.
Install the replacement compressor.
Pressurize with nitrogen and leak test all connec-
tions with a leak detection fluid (i.e., soap). Discharge
nitrogen and repair any leaks found. Repeat until all
leaks are repaired.
Evacuate the system with a vacuum pump capable
of a final vacuum of 200 microns. The system should
be evacuated through both liquid and suction lines and
gauge ports. While the unit is being evacuated, seal
all openings on the defective compressor. Compres-
sor manufacturers will void warranties on received
units that are not properly sealed. Do not distort the
manufacturers tube connections.
Recharge the system with the correct amount of re-
frigerant. Use an accurate measuring device, such as
a charging cylinder, electronic scales, or similar de-
vice, if necessary. It is necessary to add additional re-
frigerant to compensate for the volume of the driers
for a basic system charge. See Charging the System
in this manual.