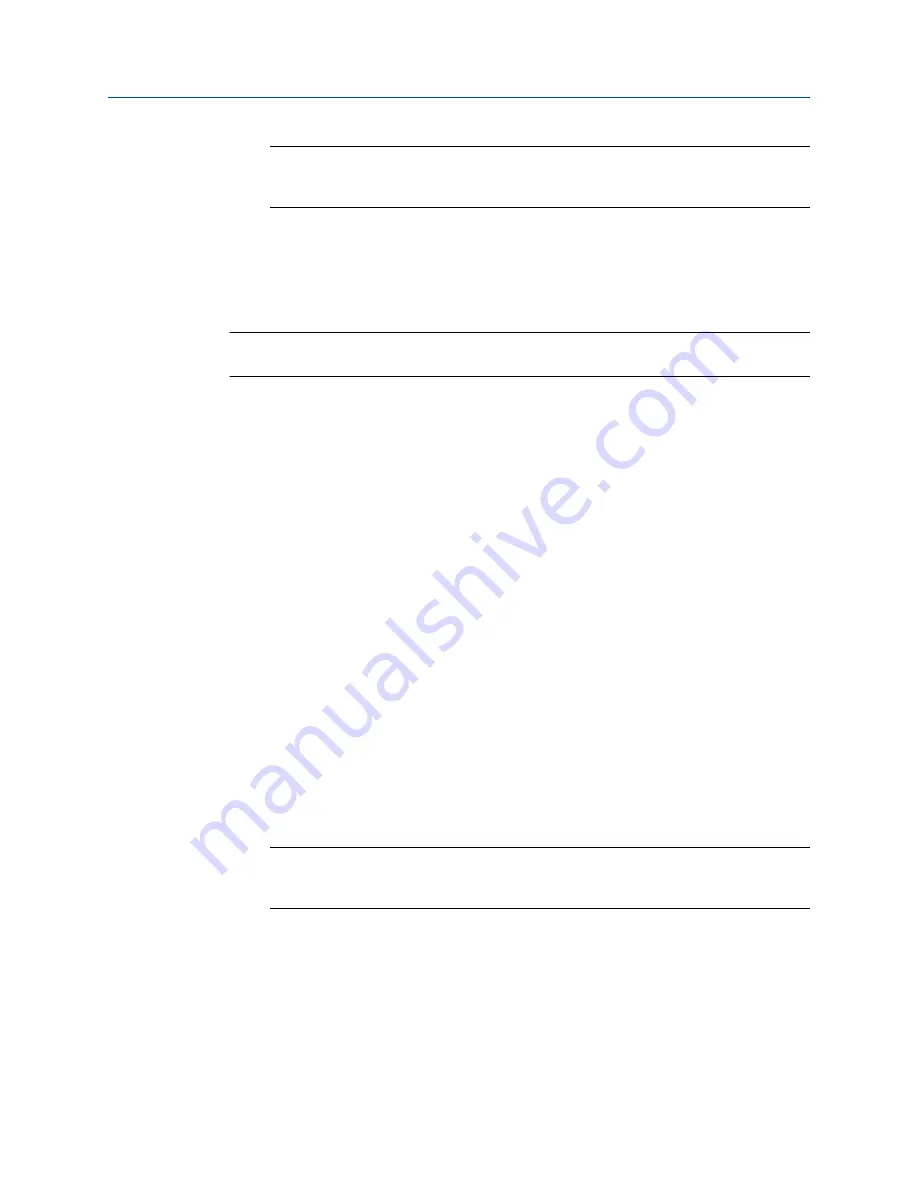
Important
When the menu system has been entered, the current output will change to 3 mA. Ensure
that external systems are bypassed, as required, prior to entering the menu system.
4.3.1
Zero
If at any time the background particulate levels change, the transmitter may be zeroed to
the new levels. Zeroing is recommended every 3 months.
Important
After initial power-up, allow the unit to warm up for 2-4 hours before zeroing.
If the sensor has been in operation for a period of time it is recommended that the window
is cleaned as outlined in
Section 5.2
.
Be sure the APM is energized up and is not indicating a fault; e.g. the display reads
Clear
,
and the status LED is blinking green, and the current output is 4.0 mA.
Prior to beginning the zeroing procedure the air surrounding the APM should be clean and
free of particulate or at the accepted background level for the specific application.
The following steps outline the procedure to perform a zero of the APM sensor.
Procedure
1.
Press and hold the Setup button or the magnet to the Reed switch to enter the main
menu; wait for the countdown, from 10 to 0, to end.
2.
Release the Setup button or remove the magnet from the Reed switch.
The current output will move to 3.0 mA.
3.
When
Set Zero
and then
YES?
is displayed press the Setup button or use the
Reed switch to select this option.
4.
A flashing
YES
will confirm your selection.
The APM has now been zeroed meaning that the existing level of air contamination
is considered normal.
Tip
If your application has a constant level of particulate present that is required to be ignored by
the APM you can set the zero level with the known particulate present as shown in
Figure 4-1
.
To further fine tune the APM response for your requirements the sensitivity settings
can be adjusted accordingly. Refer to
Section 4.3.2
.
Programming
28
Summary of Contents for Net Safety Millennium
Page 4: ......
Page 8: ...Contents iv ...
Page 14: ...Transmitter Dimensions Figure 2 3 Junction Box Sensor Dimensions Figure 2 4 Installation 6 ...
Page 34: ...Operation 26 ...
Page 42: ...Programming flowchart Figure 4 2 Programming 34 ...
Page 46: ...Maintenance 38 ...
Page 48: ...Electrostatic sensitive device 40 ...
Page 50: ...Wire resistance table 42 ...
Page 54: ...Specifications 46 ...
Page 60: ...Ordering information 52 ...
Page 61: ...Ordering information 53 ...
Page 62: ...Ordering information 54 ...
Page 63: ...Ordering information 55 ...