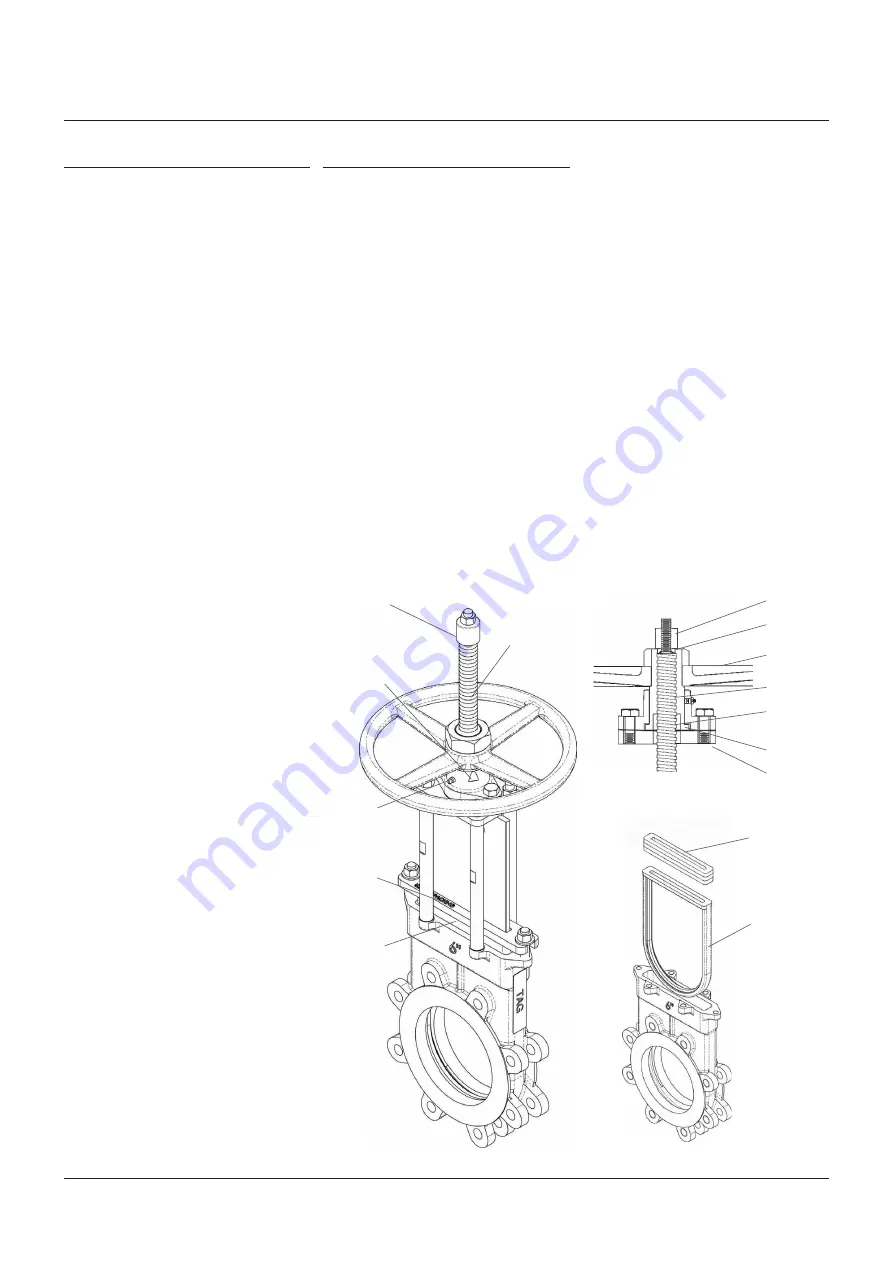
4
GENERAL MAINTENANCE
We recommend that all Keystone PCS17 knife
gates be inspected at least every 60 days.
The following points should be examined and
corrected as required (Figure 4):
1. Exterior overview: As piping system
components are subject to certain levels of
erosion and corrosion, periodic inspections
should be made as valves/components
may wear over time. Regular inspection
of the valve body and gate should be
performed, check for general signs of
corrosion, component wear and/or damage
caused by process media, i.e. wire draw,
steam cutting. If possible, check body wall
and gate thicknesses using calibrated
measuring devices such as micrometers
and/or ultrasonic thickness gauges.
Severe applications may require additional
inspection types and/or frequency.
2. Valve spindles, extension spindles, and
spindle nut: Look for excessive corrosion,
galling or lack of lubrication. If valve
spindle requires lubrication, utilize the
grease fitting provided and pump standard
bearing grease through the yoke hub
to lubricate the spindle and spindle nut
assembly. Additional lubrication may be
applied directly onto spindle or spindle
threads. (Use material which meets
ASTM 4950 GBLB.)
3. Stop nut adjustment (manual valves):
Check tightness of stop nut on valve spindle
4. Packing gland: Check for leaks or worn
packing. If leakage is occurring around the
packing gland, tighten the packing gland
bolts, being careful not to overstress the
bolting. If the valve requires repacking,
you may use any standard square braided
packing as suitable for your service.
See additional instructions for repacking
on page 5.
5. If possible stroke the valve through the full
open and closed position to make sure it is
functioning properly.
KEYSTONE
FIGURE PCS17 KNIFE GATE VALVES
INSTRUCTION, OPERATION AND MAINTENANCE MANUAL
NOTES
1. Stop all small packing or seat leaks as soon as
possible as considerable damage can be done
to the valve and the surrounding area if leakage
is allowed to continue to grow.
2. Replacement parts including handwheel and yoke
assemblies, gates, packing glands, seats and
packing can be provided from our factory.
SPARE PARTS
The following spare parts are recommended:
Cylinder operator (if applicable)
1 - Repair kit
Valves
1 - Replacement seat (Figure 6)
1 - Replacement packing set.
1. When ordering replacement parts for a
Keystone product or cylinder operator,
please include valve or cylinder size
and complete description including
serial number with your request.
2. Additional replacement parts such as
handwheels, spindle nut assemblies,
retainers, yoke posts, spindles, packing
glands, and gates are available from factory.
Again, please provide complete description
with serial number when ordering.
Seat
FIGURE 6
FIGURE 5
Stop nut
Spindle
assembly
Retaining nut
Handwheel
Spindle nut
Retainer
Retainer bolt
Packing
Stop nut
Spindle nut
(under retainer)
Spindle
Grease fitting
Packing gland
Packing
FIGURE 4