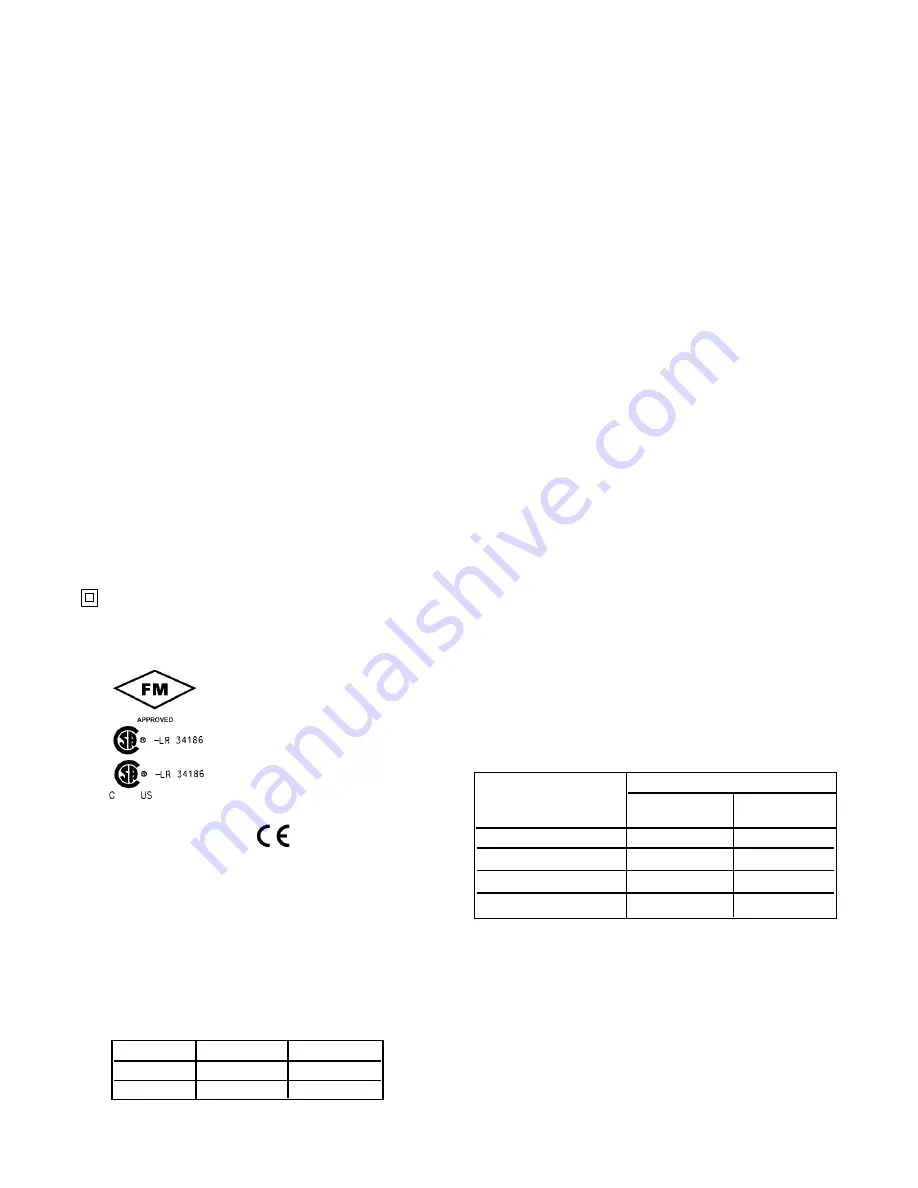
2
MODEL CLARITY II
SECTION 1.0
DESCRIPTION AND SPECIFICATIONS
1.2 SPECIFICATIONS — ANALYZER
Enclosure:
ABS (panel mount), polycarbonate (pipe/wall
mount); NEMA 4X/CSA 4 (IP65)
Dimensions:
Panel mount version: 6.10 X 6.10 X 3.72 in (155 X 155 X
94.5 mm)
Pipe/ Wall mount version: 6.23 X 6.23 X 3.23 in (158 X 158 X
82 mm)
Conduit openings:
Accepts PG 13.5 or ½-in fittings.
Display:
Two line, 16-character back lit display. Character
height 4.8 mm. Display can be customized to meet individ-
ual requirements.
Security Code:
3-digit code prevents accidental or unautho-
rized changes in instrument settings and
calibration.
Languages:
English, German, Spanish, Italian, French,
Portuguese
Units:
Turbidity (NTU, FTU, or FNU); total suspended solids
(mg/L, ppm, or no units)
Display resolution-turbidity:
4 digits; decimal point moves
from x.xxx to xxx.x
Display resolution-TSS:
4 digits; decimal point moves from
x.xxx to xxxx
Calibration methods:
user-prepared standard, commercially
prepared standard, or grab sample. For total suspended
solids user must provide a linear calibration equation.
Ambient temperature and humidity:
0 to 50°C, (32 to 122°F);
RH 10 to 90% (non-condensing)
Power:
85 to 265 Vac, 47.5 to 65.0 Hz. Maximum current with-
out option -60 alarm board: 1.0 amp, with option -60 alarm
board: 1.3 amp.
Equipment protected by double insulation.
Hazardous Location:
Class I, Div. 2, Groups A, B, C, & D: T3C Tamb 0°-50°C
Suitable for use in Class II and III, Division 2, Groups E, F
and G. Enclosure Type 4/4X
Install in accordance with control drawing
no. 1400311 or 1400312 (FM).
Install in accordance with control drawing
no. 1400313 or 1400314 (CSA).
(Ordinary Location only)
Inputs:
Choice of single or dual input
RFI/EMI:
EN-61326
LVD:
EN-61010-1
Outputs:
Single input analyzer has single output. Dual input
analyzer has dual outputs. Outputs are 0-20 mA or 4-20
mA isolated. Maximum load is 600 ohms. Output dampen-
ing with 5 sec time constant is user-selectable.
Output Accuracy:
0.05 mA
Alarms:
Optional alarm relay board includes three alarms.
Alarm 3 can be configured as a fault alarm in-stead of a
process alarm. Each relay can be configured independent-
ly. Alarm logic (low or high) and dead band are user-pro-
grammable.
Relays:
Form C, single pole, double throw, epoxy sealed.
Alarm Board Ratings:
Field wiring terminals:
removable terminal blocks for power,
analog outputs, and sensors
SPECIFICATIONS — SENSOR
Method:
EPA 180.1 or ISO 7027 (using 860 nm LED source).
Must be specified when ordering.
Incandescent lamp life:
two years
LED life:
five years
Wetted materials:
Delrin1, glass, EPDM
Accuracy after calibration at 20.0 NTU:
0 - 1 NTU: ±2% of reading or ±0.015 NTU, whichever is
greater.
0 - 20 NTU: ±2% of reading
Cable:
20 ft (6.1 m) or 50 ft (15.2 m). Maximum 50 ft
(15.2 m). Connector is IP65.
Maximum Pressure:
30 psig (308 kPa abs)
Temperature:
40 - 95°F (5 - 35°C)
1
Delrin is a registered trademark of DuPont Performance Elastomers.
SPECIFICATIONS — DEBUBBLER AND
FLOW CHAMBER
Dimensions:
18.1 in. x 4.1 in. diam. (460 mm x 104 mm diam.)
(approx.)
Wetted materials:
ABS, EPDM
Inlet:
compression fitting accepts 1/4 in. OD tubing; fitting can
be removed to provide 1/4 in. FNPT
Drain:
barbed fitting accepts 3/8 in. ID tubing; fitting can be
removed to provide 1/4 in. FNPT. Must drain to atmos-
phere.
Sample temperature:
40 - 95°F (5 - 35°C)
Minimum inlet pressure :
3.5 psig (125 kPa abs). 3.5 psig will
provide about 250 mL/min sample flow.
Maximum inlet pressure:
30 psig (308 kPa abs). Do not block
drain tube.
Recommended sample flow:
250 - 750 mL/min
Response Time:
The table shows the time in minutes to per-
cent of final value following a step change in turbidity.
SPECIFICATIONS — MISCELLANEOUS
Weight/shipping weight:
Sensor: 1 lb/2 lb (0.5 kg/1.0 kg)
Analyzer: 2 lb/3 lb (1.0 kg/1.5 kg)
Debubbler: 3 lb/4 lb (1.5 kg/2.0 kg)
(rounded to the nearest lb or 0.5 kg)
Specifications subject to change without notice.
Resistive
Inductive
115 Vac
5.0 A
3.0 A
230 Vac
5.0 A
1.5 A
reponse time (minutes)
% response following
4 gph
12 gph
step change
(250 mL/min)
(750 mL/min)
10
2.0
0.5
50
2.5
1.0
90
4.5
2.5
99
7.0
4.0