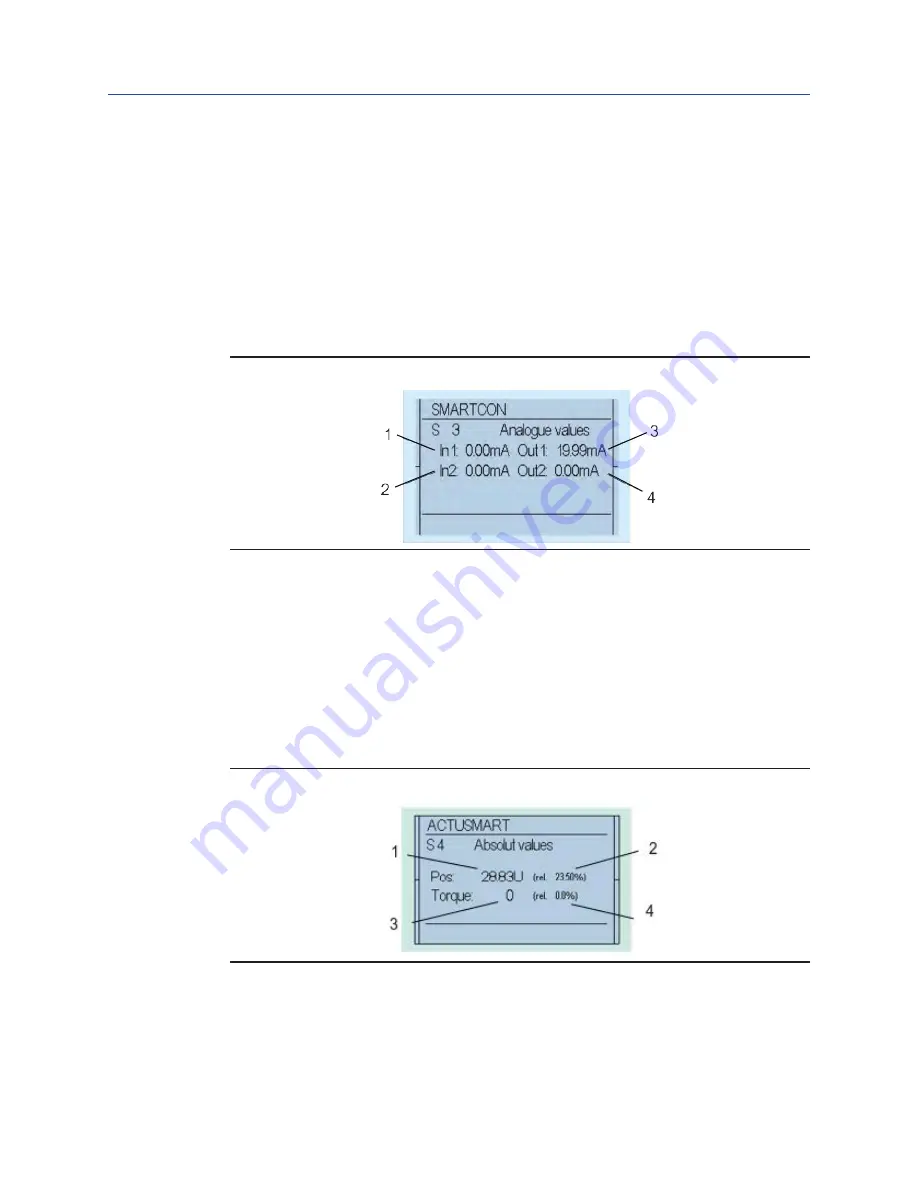
User Instructions
MAN-02-04-60-0350-EN Rev. 3
February 2019
62
Section 8: Status Area
Status Area
Display Overview:
1.
Input Number
2.
Signal (0 = Low; 1 = High)
8.1.3
Status – Analogue values
Display of analogue values: Input 1 (In1) is used by the positioner as the setpoint;
Input 2 (In2) serves as an external value for the optional PID controler. In the
analogue output (out), only the control signal is shown, regardless of whether the
output current actually flows or not (interruption of the current loop).
Figure 57
Analogue Status Display
Display Overview:
1.
Input 1
2.
Input 2
3.
Output
4.
All values in mA
8.1.4
Status – Absolute values
This status displays the absolute position of the actuator.
Figure 58
Absolute Value Display
Display Overview:
1.
Absolute value of the position unit
2.
Relative value of the position unit
3.
Absolute value of the torque unit
4.
Relative value of the position unit (calibrated in factory)