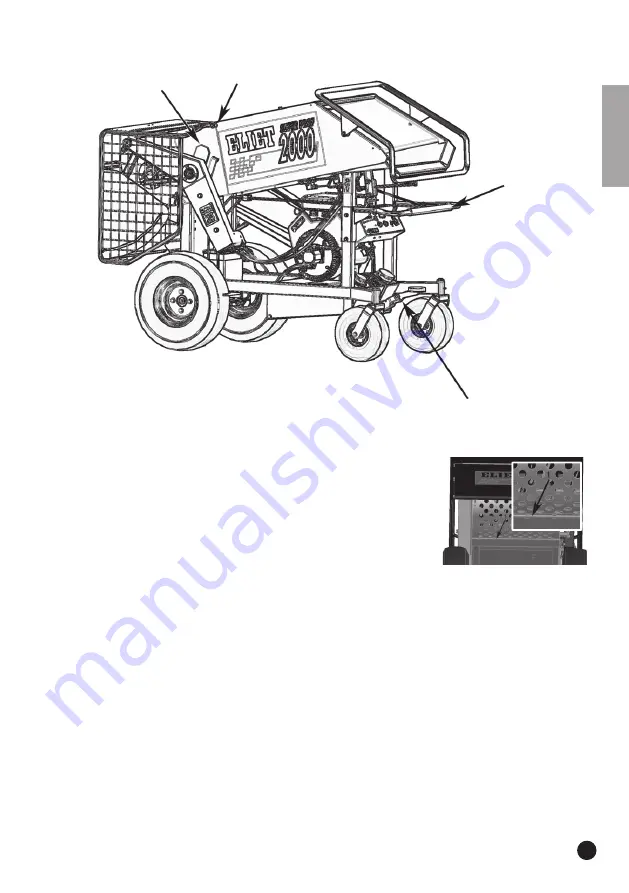
45
English
A. Lubrication of pivot points and friction surfaces
This group includes the following locations on the machine:
Ground drive control pivot points
Ball joints of the hydraulic valves
Nylon sealing plates for the feed roller guides
Throttle control lever pivot point
Choke lever
Quick-closing sieve screening system
Screen locking pin
Pivot points of the safety guard
Wheel drive brake guide
Parking brake foot pedal
Use the following procedure :
• Whenever possible, disassemble the hinge or the joint.
• Spray some penetrating oil containing molybdenum disulphide onto the frictions surfaces and
allow the oil to penetrate.
• Wipe away all traces of old lubricant and dirt.
• In the event of some parts not being accessible, use compressed air to remove all traces of old
lubricant and dirt (e.g. in the joints of pivot points).
• When the pivot points are clean, apply new lubricant.
• ELIET recommends Novatio Clearlube as a lubricant for pivot points and ball joints. ELIET would
recommend Novatio PFT grease for friction surfaces.
• Wipe away any excess lubricant.
Summary of Contents for MA 006 010 113
Page 1: ...Superprof M A N U A L...
Page 2: ...2 English...