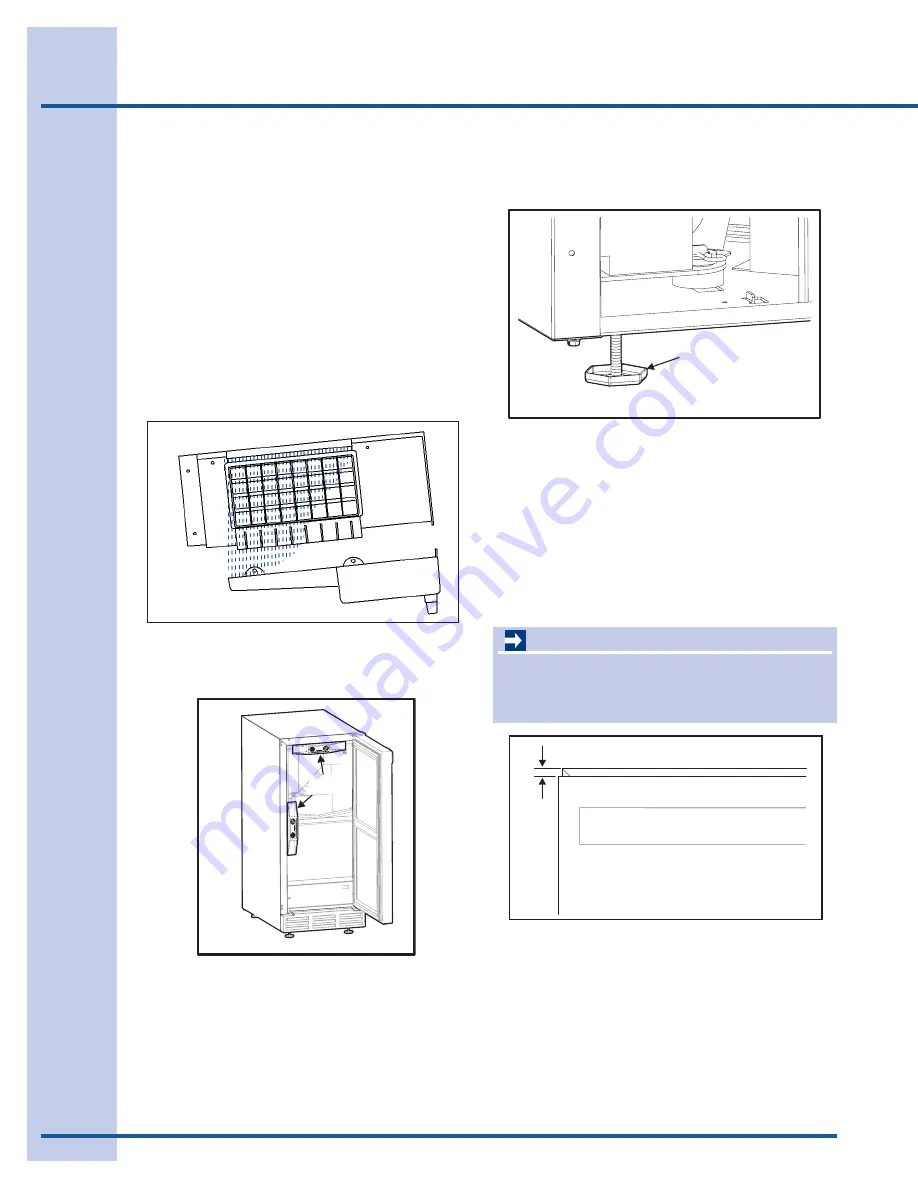
4
Installation
Leveling
It is extremely important that the unit is level for
maximum protection.
If it is not:
• Doors and/or drawers will not work properly.
• Uneven sized cubes will be formed. Ice
production will be reduced and water spilling
into the storage area can occur, causing
the ice in the bin to melt prematurely.
See
Figure1.
Remember, floors surrounding a drain have a
tendency to slope toward the drain.
IMPORTANT
Properly aligned, the door should be 1/8” below
the top of the unit’s cabinet, NOT flush with the
top.
See Figure 4.
Adjusting Door
Checking Door Alignmemt
The unit’s door is aligned at the foctory before
shipment. However, its alignment could have been
disturbed during shipment or during door panel
installation.
1
Compare the top edge of the door to the top
edge of the cabinet.
2
If the door edge is 1/8 inch below and
parallel to the top of the cabinet, it is adjusted
correctly. If it is not, note whether the side
oposite the hinge needs to be moved UP or
DOWN, and use the following procedure:
1. Use a level to check the unit from front to
back and from side to side.
See Figure 2.
Figure 1
CHECK
LEVEL
Figure 2
TURN FOOT TO ADJUST
Figure 3
2. If the unit is not level, adjust the feet on the
corner as necessary.
See Figure 3.
Rotating
the feet clockwise raises the unit.
3. Check after each adjustment. Repeat the
previous steps as necessary until the unit is
level.
1/8”
Figure 4
Summary of Contents for E15IM60GPS
Page 47: ......