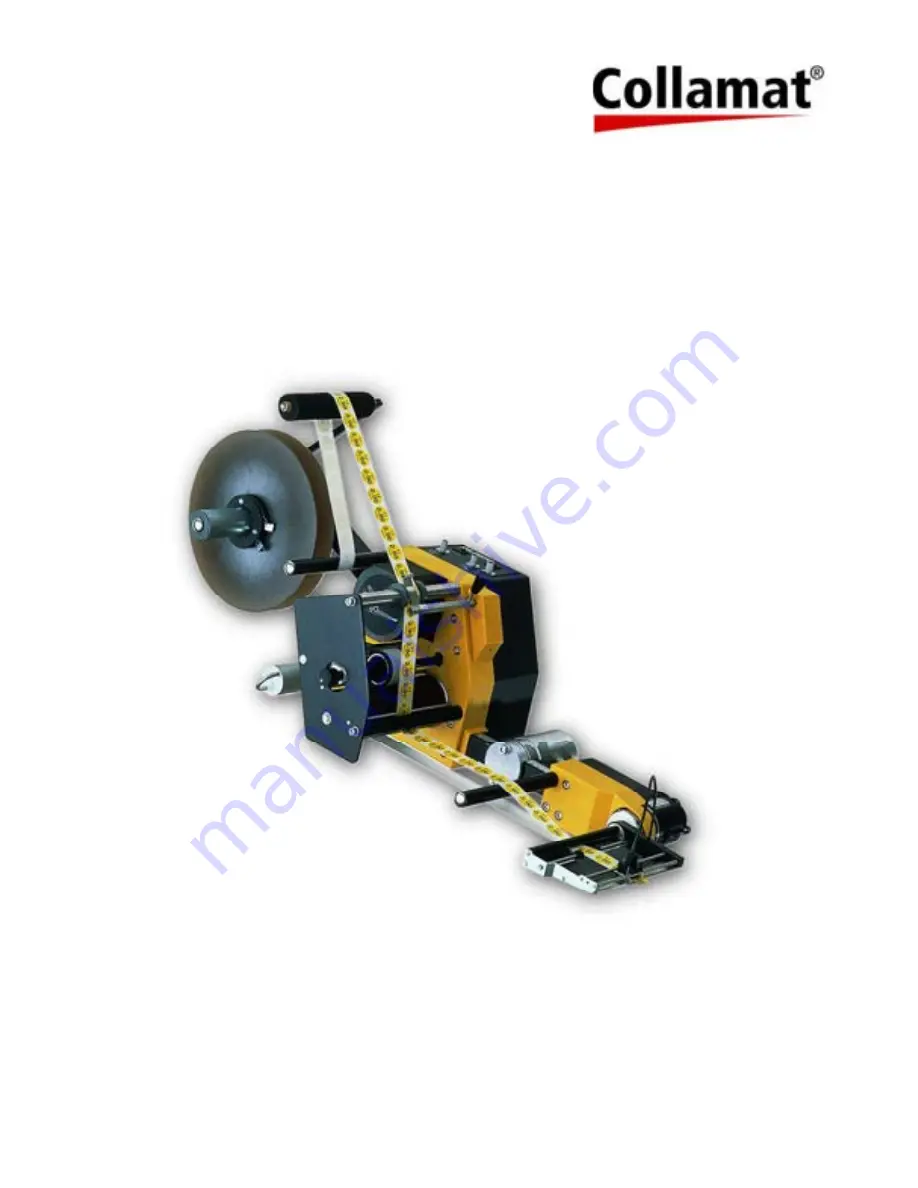
Contents
Technical Handbook
Collamat C4300- / C7300- Series
Doc-ID: TH-C4300-C7300-EN
Release: 1.00/01/2013
This manual is a translated English version. The only mandatory
Technical Handbook for this product is the German version – signed
as the Original-/Reference-Version.
These Operating Instructions and the Technical Handbook have to be read before start up, and before any work
are done on the machine.