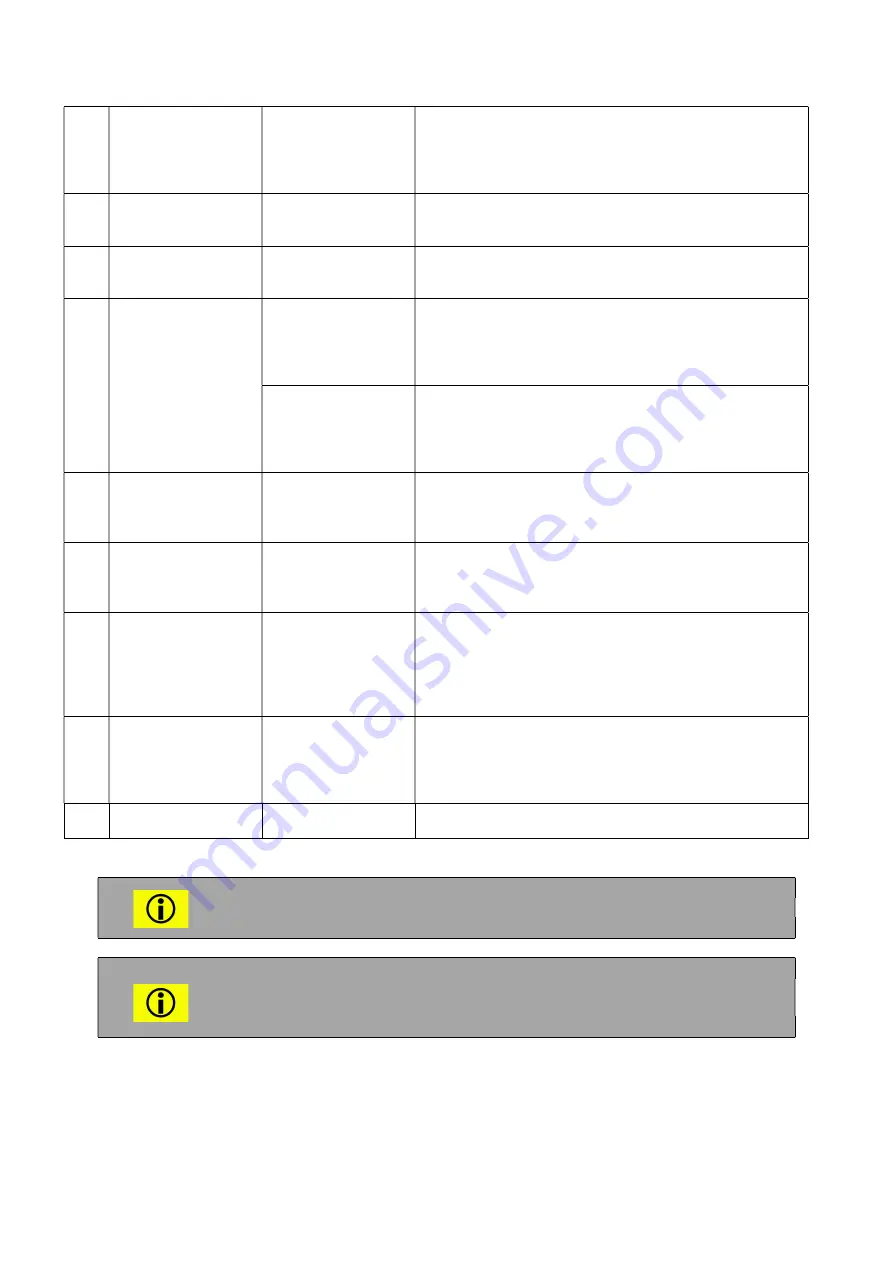
Pellet burner GP xx sc 39
temperature sticker,
positioned on the
pellets inlet pipe of
the burner
temperature in this
pipe, which in most
cases is caused by
hot gasses passing
through it
check the pellet burner condition - to be performed by
specialist.
16.
Dirty and/or melted
photic sensor
Improper stopping of
the burner’s
operation
It is necessary to clean the photic sensor’s surface or to
replace it with new one. The burner’s stopping procedure,
as presented in this manual book, must be observed.
17.
Presence of
unburned fuel in the
ash tray
Inefficient fuel
combustion
It is necessary to adjust the appliance’s operational
parameters – ask authorized servicing technicians for
consultation and/or to perform adjustments.
18.
Too many slag
deposits in the
burner’s combustion
chamber (melted
mineral mass)
The used fuel is with
high ash content and
does not comply with
the requirements of
the appliance
Change the fuel with type which complies with the
requirements for reliable operation of the burner.
The burner operates
in a mode with
heating output higher
than its nominal
output
Decrease the heating output of the burner by changing its
output level.
19.
A failure code,
indicated on the
controller’s display
panel
Trouble in the
operation of the
burner
Check the meaning of the indicated failure code in the
next table. If necessary look for consultation/intervention
by servicing technician.
20.
The
burner
has
stopped, but after a
new start it operates
again
The photic sensor
submits faulty
information to the
controller
Check the fuel quantity over the fire-grate. Look for
assistance or consultation by servicing technician.
21.
High temperature of
the flue gas (if a
thermometer is
installed)
Dirty heat
exchanging surfaces,
depending on the
consuming appliance
type and the
operation modes
It is necessary to clean the appliance’s heat exchanging
surfaces.
22.
Smoke in the boiler
room after a certain
period of operation
Dirty or clogged from
dust flue extraction
tract of the heat
energy consuming
appliance
Clean the heat energy consuming appliance from the ash
deposits.
23.
Another, not
described failures
Ask for assistance by servicing specialist or company.
* The heating of the pellets inlet pipe in most cases is caused by
contamination of the heat exchanging surfaces of the appliance, to which
the pellet burner is mounted;
** In case of insufficient chimney draught it is recommended to look for
servicing assistance in order to solve the problem – cleaning or change of the
chimney might be required, as well as installation of additional flue extraction
fan or another solution.