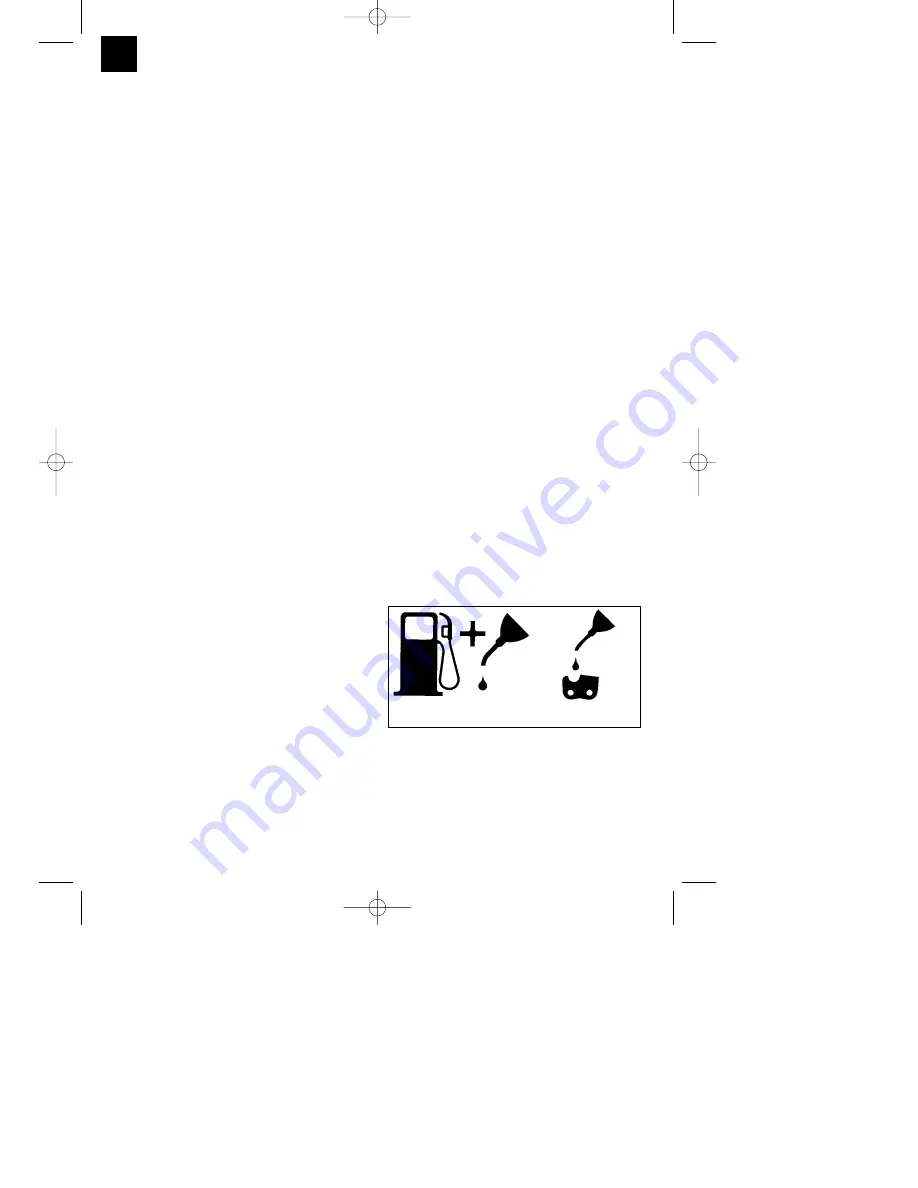
Warning:
Always wear heavy duty gloves when
handling saw chain or making saw chain adjustments.
1.
Hold nose of guide bar up and turn adjustment
screw (D) CLOCKWISE to increase chain
tension. Turning screw COUNTERCLOCKWISE
will decrease amount of tension on chain. Ensure
the chain fits snugly all the way around the guide
bar (Fig. 5).
2.
After making adjustment, and while still holding
nose of bar in the uppermost position, tighten the
bar retaining nuts securely. Chain has proper
tension when it has a snug fit all around and can
be pulled around by gloved hand.
NOTE:
If chain is difficult to rotate on guide bar or if it
binds, too much tension has been applied. This
requires minor adjustment as follows:
A.
Loosen the bar retaining nut so they are finger
tight. Decrease tension by turning the bar
adjustment screw COUNTERCLOCKWISE
slowly. Move chain back and forth on bar.
Continue to adjust until chain rotates freely, but
fits snugly. Increase tension by turning bar
adjustment screw CLOCKWISE.
B.
When saw chain has proper tension, hold nose of
bar in the uppermost position and tighten the bar
retaining nut securely.
Caution:
A new saw chain stretches, requiring
adjustment after as few as 5 cuts. This is normal with
a new chain, and the interval between future
adjustments will lengthen quickly.
Caution:
If the saw chain is TOO LOOSE or TOO
TAUT, the drive wheel, chain bar, chain and crank
shaft bearing will suffer premature wear. Fig. 6 shows
the correct tension A (when cold) and tension B
(when warm). Fig. C shows a chain that is too loose.
5.4 Chain break mechanical test
Your chain saw is equipped with a Chain brake that
reduces possibility of injury due to kickback. The
brake is activated if pressure is applied against brake
lever when, as in the event of kickback, operator’s
hand strikes the lever. When the brake is actuated,
chain movement stops abruptly.
Warning:
The purpose of the chain brake is to
reduce the possibility of injury due to kickback;
however, it cannot provide the intended measure of
protection if the saw is operated carelessly. Always
test the chain brake before using your saw and
periodically while on the job.
To test chain brake
1.
The Chain brake is DISENGAGED (chain can
move) when BRAKE LEVER IS PULLED BACK
AND LOCKED (Fig. 7A).
2.
The chain brake is ENGAGED (the chain is
locked) when the brake lever is pulled forward
and the mechanism (Fig. 7B/Item A) can be
seen. It should not be possible to move the chain
(Fig. 7B).
NOTE:
The brake lever should snap into both
positions. If strong resistance is felt, or lever does not
move into either position, do not use your saw. Take it
immediately to a professional Service Center for
repair.
5.5 Fuel and lubrication
Fuel
Use regular grade unleaded gasoline mixed with
25:1 custom 2-cycle engine oil for best results.
Mixing fuel
Mix fuel with 2 cycle oil in an approved container.
Shake container to ensure thorough mix.
Warning:
Never use straight gasoline in your
unit. This will cause permanent engine damage and
void the manufacturer’s warranty for that product.
Never use a fuel mixture that has been stored for over
90 days.
Warning:
If 2-cycle lubricant is to be used, it
must be a premium grade oil for 2-cycle air cooled
engines mixed at a 25:1 ratio. Do not use any 2-cycle
oil product with a recommended mixing ratio of
100:1. If insufficient lubrication is the cause of engine
damage, it voids the manufacturer’s engine warranty
for that occurrence.
Recommended fuels
Some conventional gasolines are being blended with
oxygenates such as alcohol or an ether compound to
meet clean air standards. Your engine is designed to
operate satisfactorily on any gasoline intended for
automotive use including oxygenated gasolines. It is
recommended to use unleaded petrol as fuel.
22
GB
Gasoline and Oil Mix 25:1
Oil Only
Anleitung_RBK_4645_SPK1:_ 14.12.2009 15:18 Uhr Seite 22
Summary of Contents for BT-LS 810 D
Page 5: ...5 15 16 17 14 19 14 H L 18 21 14 Anleitung_BT_LS_810_D_SPK7 _ 05 09 2007 12 58 Uhr Seite 5 ...
Page 47: ...7 24 23 25 26 A Anleitung_RBK_4645_SPK1 _ 14 12 2009 15 18 Uhr Seite 7 ...
Page 161: ...121 Anleitung_RBK_4645_SPK1 _ 14 12 2009 15 19 Uhr Seite 121 ...
Page 174: ...2 1 2 5 4 3 2 5 1 3a 6 Anleitung_BG_SH_1_SPK1 _ 24 11 2009 14 19 Uhr Seite 2 ...
Page 175: ...3 3b 3c 3d 3e 3f 3g Anleitung_BG_SH_1_SPK1 _ 24 11 2009 14 19 Uhr Seite 3 ...
Page 176: ...4 4b 4c 5 8 6 4a 3h A B C Anleitung_BG_SH_1_SPK1 _ 24 11 2009 14 20 Uhr Seite 4 ...
Page 177: ...5 7 8 9 10 F D G H J K I L M Anleitung_BG_SH_1_SPK1 _ 24 11 2009 14 20 Uhr Seite 5 ...
Page 224: ...4 15 16 13 14 2 1 Anleitung_BG_CS_85_E_SPK1 _ 05 06 2008 14 21 Uhr Seite 4 ...