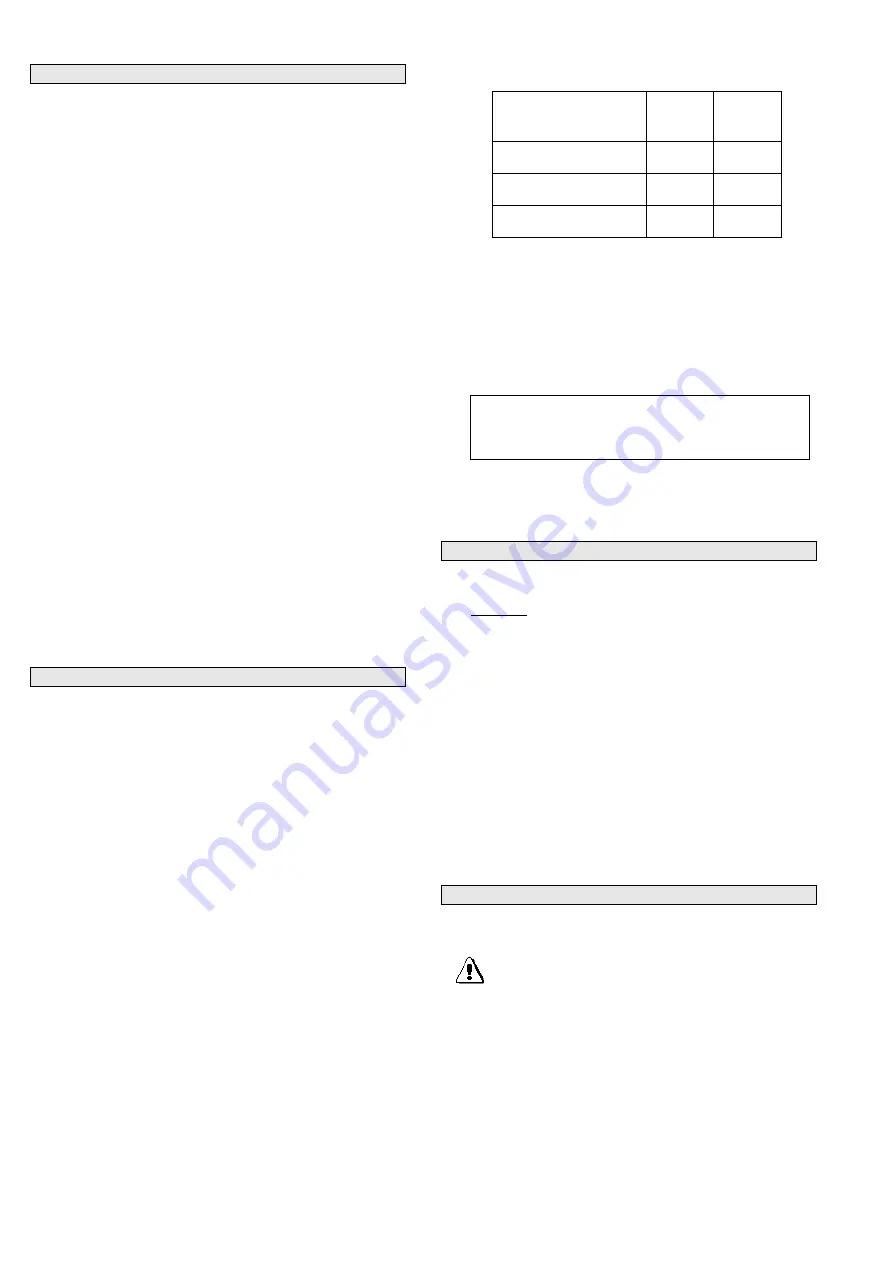
6
4.2.2 Pump
1. Remove dust caps from drive end and inspection end
bearing housings.
2. Remove lockwashers and locknuts from both inspection
end and drive end of shaft.
3. Remove both bearing housings. (To remove bearing
housing, screw two of the bearing housing setscrews into
the tapped holes provided in the bearing housing. Evenly
tighten the setscrews to withdraw the bearing housing.)
Take care not to damage the mechanical seal faces.
4. Press out the ball bearings from the bearing housings.
5. Remove the bearing dampening O-Rings from the shaft
then carefully remove the mechanical seal components
from both the bearing housings and from the rotor/shaft
assembly.
6. Remove body covers and wearplates (To remove body
cover, screw four of the bearing housing setscrews into
the tapped extraction holes provided in the body cover.
Evenly tighten the setscrews to withdraw the body cover.)
7. Withdraw the rotor/shaft/vane assembly from the body
taking care to support the vanes as the assembly is
withdrawn.
8. Remove vanes and pushrods from the rotor (note the
orientation of the vanes relative to the direction of
rotation)
9. Remove liner from body (note the orientation of the liner
relative to the inlet and discharge ports of the body.
10. Remove grease nipples and pressure release plugs from
the bearing housings.
11. Remove oil seal from drive end dust cap.
4.3
INSPECTION
NOTE:
Optimum
performance
is
achieved
by
maintaining
the
pump
within
the
following
guidelines.
Adequate performance may still be achieved
dependent on application parameters
.
1. Inspect rotor/shaft assembly and liner. If damage or
excessive wear is evident, it is recommended to replace
both components. Scoring in the seal zones of the liner is
detrimental to optimum performance.
NB:
The rotor is permanently attached to the shaft.
2. Inspect both mechanical seals. Replace mechanical seal
assembly if components are worn or damaged
3. Inspect vane pushrods for wear, damage and
straightness. Replace the pushrods if they show signs of
physical damage, wear or distortion e.g. mushroomed,
rounded or tapered ends, scoring on flanks, bending,
etc.
4. Inspect vanes for wear or damage. Replace if damaged
or excessive wear is evident. Check for scoring on vane
tips.
Recommended Minimum
Worn Vane Sizes
Vane
Length
Vane
Height
V2000
74.62mm
27.00mm
V3000
89.62mm
28.00mm
V3010
89.62mm
28.00mm
5. Inspect pressure relief valve assembly and components
for wear or damage. Replace or refurbish as required.
6. It is recommended that all O-Rings and lip seals be
replaced at every overhaul.
7. Inspect both ball bearings for wear. It is recommended
on major overhauls that ball bearings be replaced.
8.
Ensure pressure relief ducts in bearing housings are not
obstructed
.
4.4
SPARE PARTS
1. When ordering spare parts, to ensure a minimum of
delay and correct replacement to original specification,
ALWAYS quote the pump Serial Number located on the
nameplate of the pump.
2. Advise the name, Cat # and quantity required. Refer
Section 5
– Parts Designation.
3. Advise complete delivery instructions, transportation,
etc.
NOTE:
Substitute or so-
called ‘equivalent’ item/spare
parts are not recommended for use.
Compliance, safe operation and pump performance
may be severely compromised if incorrect or substitute
spare parts
– including Fasteners, O-Rings, Ball
Bearings, etc
– are used.
Only use genuine Ebsray spare parts.
4.5
REASSEMBLY - PRELIMINARY
1. Ensure all parts are clean and deburred before
assembly.
At all times when handling and
installing mechanical seals,
care must be taken to ensure lapped faces and seats
are not damaged. Particular attention must be given to
carbon seats to prevent marking or chipping.
2. Lubricate all O-Rings and lapped faces of mechanical
seals with a good quality, compatible, detergent-free
light oil before assembly.
3. Pack Ball Bearings with a good quality, suitable grease.
4. Ensure correct orientation of components relative to
pump rotation/handing .
CAUTION
DANGER
Ball Bearing Replacement interval should not exceed
V2000
10,000 operational hours
V3000
5,000 operational hours
V3010
5,000 operational hours
Summary of Contents for V Series
Page 9: ...9...
Page 12: ...12 NOTES...