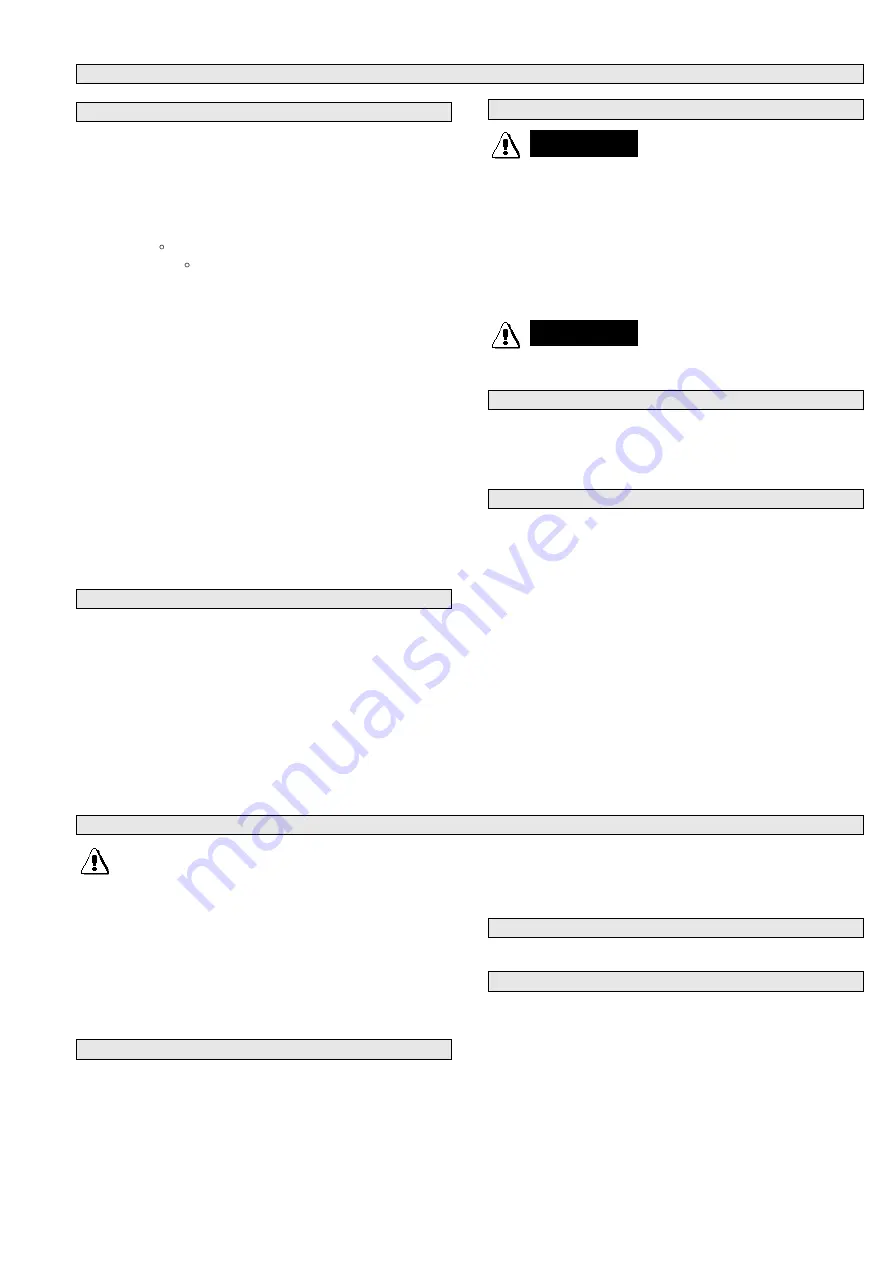
5
WARNING
ER
SECTION 3
– OPERATION
3.1
DESCRIPTION
The EBSRAY Models V2000, V3000 & V3010 are positive
displacement Sliding Vane Pumps, primarily intended for the
transfer of LPG and other low to medium viscosity liquids. All
models are of identical internal design and construction
however the V3000 is mounted via the top inlet port flange
and has bottom discharge. The V3000 also offers an
alternate 45 inlet port. The V2000 and V3010 are foot
mounted with 90 porting and top discharge. All Models are
available with single or double ended drive shafts. Model
V3010 is available with an aluminium body
– application
dependant (not for LPG or Anhydrous Ammonia).
In all models, the Rotor/Shaft assembly rotates within a cam-
form Liner and between two replaceable Wearplates.
Mechanical Seals, located outside the wearplates, isolate the
Drive End and Inspection End Ball Bearings from the
pumpage. These grease packed heavy duty Double Row
Deep Groove Ball Bearings provide positive radial and axial
positioning of the pump rotor. A lip seal is fitted to the Drive
End Cover to minimise the ingress of dust/dirt along the
shaft.
The pump is protected from excessive pressure rise by an
internal pressure relief valve with tamperproof adjustment.
The V2000, V3000 and V3010 Pumps are designed to
provide trouble-free & safe operation and must be operated
in accordance with the following recommendations.
3.2
LUBRICATION
Periodic ball bearing lubrication is required via grease nipples
fitted to the bearing housings at approximately every 500
hours of operation. Ebsray recommends the use of a lithium
complex NLGI Grade 2 grease with an ISO VG220 viscosity
rating.
3.3
PRE-STARTUP CHECKLIST
Do not run Pump dry. Do not
start Pump against closed
Discharge Valve unless external bypass protection is
fitted. Severe internal damage to the Pump will result,
voiding Warranty.
►
Lubricate as required.
►
Check alignment of couplings.
►
Ensure freedom of rotation of shaft.
►
Check direction of rotation
►
Open inlet and discharge valves
To prevent damage to pump or
system,
disengage
coupling
before checking direction of rotation.
3.4
OPERATIONAL CHECKS
Inspect pump frequently during the first few hours of
operation for such conditions as excessive heating of ball
bearings, vibration or unusual noises etc.
3.5
PERIODIC INSPECTION
Periodic Inspection of the Pump, Pump System and
Ancillary Equipment is required to maintain safety,
conformity, operational functionality and reliability. Ebsray
recommends a maximum interval of three months or 500
hours operation between routine periodic maintenance
inspections (More frequent inspections may be necessary
dependent upon usage, site conditions, operation etc).
If any abnormal condition is discovered, cease operation of
pump immediately and take action to rectify the problem.
For safe operation, the following items should be included in
the routine periodic inspection:
a.
Inspect the Pump for leaks, vibration, abnormal noises,
signs of overheating, discolouration, etc.
b.
Inspect Coupling Assembly for signs of wear,
overheating, discolouration, etc.
c.
Check Pump differential pressure
SECTION 4
– MAINTENANCE
Prior to any system disassembly
or
service,
verify
that
all
requirements of statutory Directives, Standards, Codes
and Regulations, are met and that specific site
requirements etc are satisfied
Some minor maintenance tasks and inspections can be
performed with the pump ‘in line’ so long as complete
isolation, depressurising and purging procedures have been
completed. However for major maintenance it is
recommended that the pump be removed from the
installation
4.1
PREPARATION FOR DISASSEMBLY
1. Obtain the appropriate Work Permit if required.
2. Isolate power supply to motor
– if fitted.
3. Isolate pump from liquids in suction and discharge lines,
depressurise and purge out any toxic, flammable,
corrosive or air hardening liquids (if present).
4. Disconnect porting connections.
5. Remove pump from installation.
4.2
DISASSEMBLY
Refer to the Parts Designation drawings in Section 5
4.2.1 Pressure Relief Valve
1. Remove flush plug from valve cover.
2. Using a 6mm allen wrench, turn the adjusting screw
clockwise to
reduce
spring tension.
3. Remove valve cover and O-Ring together with spring
cap, spring and valve.
4. Remove spring cap from valve cover and remove O-Ring
from spring cap.
WARNING
ER
CAUTION
DANGER
Summary of Contents for V Series
Page 9: ...9...
Page 12: ...12 NOTES...