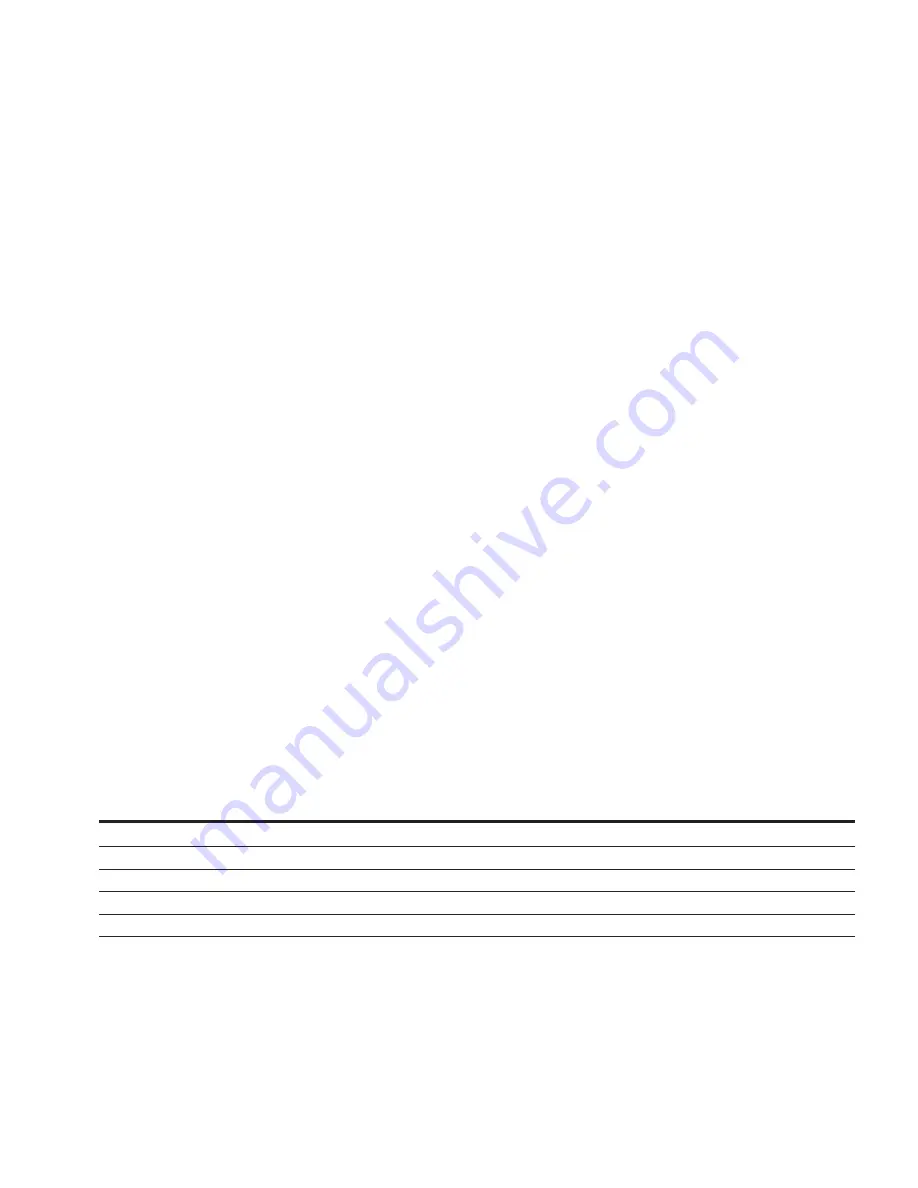
31
CMA USER MANUAL
E-VLMB-TT005-E April 2019 www.eaton.com
CMA User Manual
6.6.1 Enter options
There are several different options for how the valve will
respond once a fault is detected. There is an OD parameter
called “Logged Fault” that is used to store the detected
fault. This OD entry is written to by the Fault Handler, but
without a Write Finalize command (which resets the PV), it
will not be saved for the next power cycle. If a Write Finalize
is desired, the command can either be issued automatically
by the valve, or initiated by the user. The options are:
0 (Bit 28=0 Bit 29=0): Do not enter any Limp Modes and go
directly to a Safe State (PWM OFF)
1 (Bit 28=1 Bit 29=0): Automatically enter Limp Mode
without a Write Finalize. In this case the fault will not be
saved across resets unless the user initiates a Write Finalize
2 (Bit 28=0 Bit 29=1): The valve will automatically issue a
Write Finalize command and reset itself. On starting back
up, the fault will be written in Logged Fault, and the valve
will enter the Limp Modes. In order to clear the fault, a 0
needs to be written to the Logged Fault parameter location.
3 (Bit 28=1 Bit 29=1): Wait for the user to issue a Write
Finalize command. While waiting, the valve will set the
PWM to 0 (disable the valve) and issue periodic Warning
messages to the user that the valve is waiting for a Write
Finalize
Fault information is stored in the Logged Fault OD entry
using the following list:
0: All clear, no fault
1: Fault on position sensor 1
2: Fault on position sensor 2
3: Fault on pressure sensor 1
4: Fault on pressure sensor 2
7: Unknown fault or multiple faults resulting in PWM OFF
Writing these values to Logged Fault can be used to test
the FOP modes.
6.6.2 Exit options
There are currently only two exit options:
0 (bit 30=0): automatically exit Limp Modes when the valve
no longer detects a fault
1 (bit 30=1): do not exit Limp Modes, but issue a Warning
message that the fault condition is gone.
Note if a 1 is written to bit 31, the system will default to not
exit Limp Modes and not issue a notification that the fault
is gone.
6.6.3 Limp mode parameter tuning
There are different Fail Operational modes for each of the
4 possible sensor failures. Most modes have PID gains that
can be tuned, as well as a filter on the derivative term to
reduce the effect of noise. It should be noted that some
degradation of performance should be expected when
operating in the limp modes. In particular, there may be
delays in starting motion and some jerks when motions
starts. The machine will also likely be less efficient as the
back pressure may be higher in some cases. For failed
pressure sensors, the controller will attempt to learn the
missing sensor information as the service moves. There
are parameters that specify an initial guess for the pressure
on each work port. In order to prevent services from falling,
the largest expected load on that service should be entered.
If there is no danger of a falling load, this estimate can
be set lower, which might speed up the start of motion.
Most of the modes work by trying to maintain a constant
pressure on the non-load-holding side. The desired pressure
is a parameter, the suggested value is for this to be at
least 15 bar.
Table 33 .
Object dictionary name
J1939 section index
CANOpen object
Suggested default value
Units
Fault Handler Configuration (bit map)
602
0x425A
Application Specific
Bit mask
Off-side Pressure Demand
648
0x4288
1500
cbar
Max Load Estimate WP1
649
0x4289
30000
cbar
Max Load Estimate WP2
650
0x428A
30000
cbar
Logged Fault
989
0x43DD
0
enum