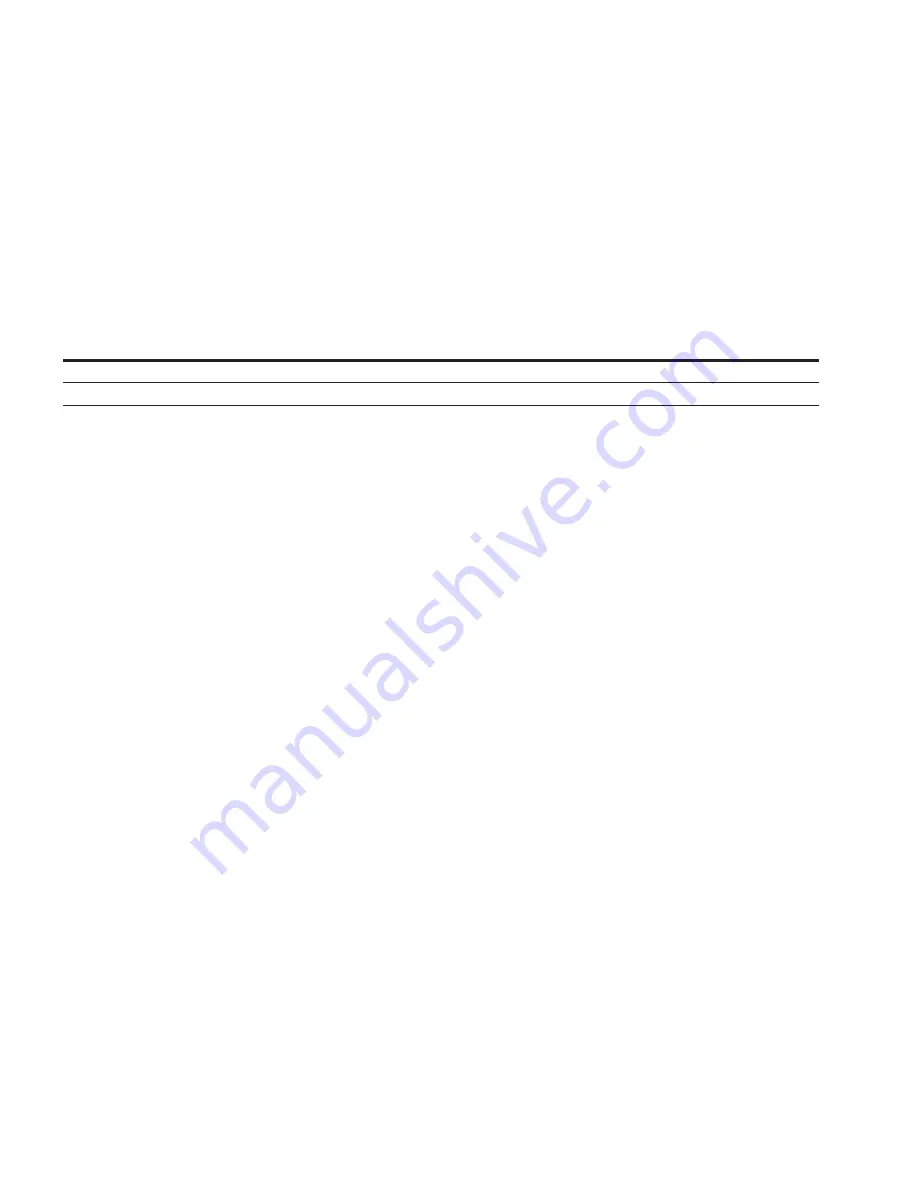
12
CMA USER MANUAL
E-VLMB-TT005-E April 2019 www.eaton.com
CMA User Manual
5.2 Electronic load sensing
Typically a variable displacement CV controls the pump
pressure via a load sensing hydraulic line connected to
the variable displacement pump. For some machines,
however, it is desirable that the variable displacement CV
does not hydraulically control the pump. Instead the CV
provides the desired pump pressure to the application via
the network and the application controls the pump. This
electronic load sensing capability can be enabled by setting
eLS_output = 1. The pressure demand can then be read
from Debug_2. Note, this will override what was selected
to be sent over Debug 2 using Press_Debug_Switch2.
Additionally, the application can command the CV to Zero
PWM mode to prevent the CV from attempting to control
its load sensing port.
The table below summarizes the OD parameters used for
electronic load sensing:
6 Pilot valve setup
The majority of this document focuses on the setup of
each pilot (work section). In the following sections, the
user will learn what parameters are configurable and
what their function is.
6.1 Application settings
6.1.1 Load sense setup
Independent of the control mode selected, you will need
to set the load sense margin (LS margin) as well as the
load sense standby pressure demand. The following
describe each of these parameters and when they are
applied in detail.
6.1.1.1 Load sense margin
The LS margin setting is added to the load pressure and is
sent to the CV as the load sense demand while there is a
flow or pressure demand. For single spool modes, the load
sense demand that is requested is based on the direction
of flow. If you are requesting flow from supply to port, then
the LS margin is added to the port pressure and sent off as
a supply pressure request. If you are requesting flow from
port to tank, then the LS demand is zero. For twin spool
modes, refer to the twin spool controller description for
how the supply pressure demand is handled.
You want to minimize your LS margin pressure to make
the system as efficient as possible. The lower the margin
the less overhead the service has for inrush flow which
can reduce responsiveness. As mentioned above, the LS
demand from the service is transmitted to the CV. The CV
then takes the maximum LS demand and adds the CV
margin. Therefore the CV margin and the LS margin make
up the total margin when metering from supply to service.
otee:
N
In order to get the full rated flow out of the valve,
the total margin from supply to service needs to
be at least 14 bar.
Note that the LS margin suggested default value is 0.
The reason for this is because the suggested CV margin
is 1000 cbar, which means that there will always be a
minimum of 10 bar margin between supply and the highest
load pressure. If additional margin is needed for a specific
section, the LS margin can be increased for that
PV exclusively.
6.1.1.2 Load sense standby pressure
If the flow demand is zero the load sense standby pressure
setting will be sent to the CV as the load sense request for
that respective service. Increasing the LS standby pressure
parameter can give you quicker response times from
that service but obviously requires higher supply standby
pressures and is less efficient.
6.1.1.3 Load sense filtering
In some applications, it may be useful to add a filter or a
rate limit to the load sense demand that is coming from
an individual PV to try to prevent interaction between the
inlet controller, the PV controller, and an oscillatory load.
The filter provides both a bandwidth limit and an increasing
and decreasing Rate of Change limit. The structure of the
filter is the same as what is described in section 5.1 for the
inlet controller. One trick that can be helpful for eliminating
oscillations with the pump is to have a small Decreasing
Rate of Change limit on the load sense demand. This may
keep the pump slightly higher than it needs to be for a short
time, but it can prevent the pump from chasing fluctuations
in the load pressure and triggering an oscillation. The default
settings for this filter will have it fast enough to not limit the
load sense demand. The equation for tuning the bandwidth
of the filter is (repeated from section 5.1):
Trajectory_bandwidth = (1-e^(-2*pi*Fc*.0015))*2^16,
where Fc is the low pass filter cutoff frequency.
Table 9 .
Object dictionary name
J1939 section index
CANOpen object
Value to set/read
Units
eLS_output
641
0x3281
1
unitless
Debug_2
516
0x3204
Read for desired pressure
bar