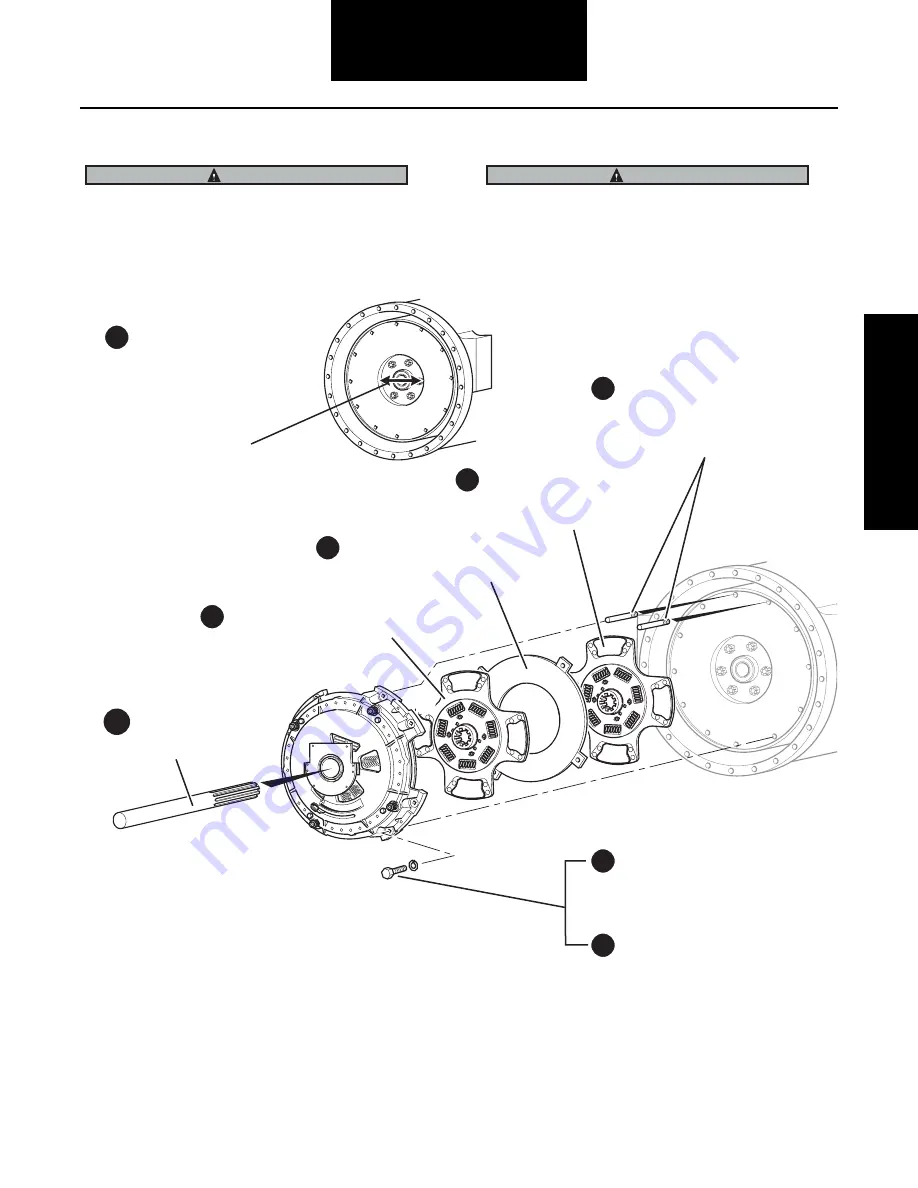
3
Solo Advantage
Self-Adjusting Clutches
Install
Install Clutch to Flywheel
U
s
e the Eato
n
Cl
u
tch
S
electo
r
G
u
ide (CL
S
L1511)
to make
sur
e yo
u
have the
r
ight cl
u
tch.
A
n
a
ss
embled cl
u
tch weigh
s
abo
u
t 150 lb
s
(68 kg).
Avoid the
r
i
s
k of i
n
j
ur
y. U
s
e p
r
ope
r
eq
u
ipme
n
t
whe
n
lifti
n
g a cl
u
tch.
P
r
og
r
e
ss
ively tighte
n
mo
un
ti
n
g bolt
s
i
n
a c
r
i
ss
c
r
o
ss
patte
rn
s
ta
r
ti
n
g with the
lowe
r
left bolt (1, 2, 3, 4, 5, 6, 7, 8).
To
r
q
u
e to 40-50 lb-ft (54-68 N•m).
Fail
ur
e to do thi
s
co
u
ld
r
e
su
lt i
n
imp
r
ope
r
piloti
n
g of the cl
u
tch
a
n
d ca
us
e cl
u
tch damage.
8
I
ns
tall lock wa
s
he
rs
a
n
d mo
un
ti
n
g
bolt
s
(7/16" x 14 UNC x 2-1/4"
g
r
ade 5) fi
n
ge
r
tight. Replace
s
t
u
d
s
with lock wa
s
he
rs
a
n
d bolt
s
.
7
I
ns
tall
s
eco
n
d di
s
c o
n
to alig
n
i
n
g
tool. Follow the o
r
ie
n
tatio
n
i
ns
t
ru
ctio
ns
o
n
the di
s
c.
5
I
ns
tall i
n
te
r
mediate plate i
n
to
s
lot
s
o
n
the cl
u
tch cove
r
. Flywheel
s
ide
m
us
t face the flywheel.
4
I
ns
tall di
s
c o
n
to alig
n
i
n
g tool.
Follow the o
r
ie
n
tatio
n
i
ns
t
ru
ctio
ns
o
n
the di
s
c.
3
I
ns
e
r
t alig
n
i
n
g tool
th
r
o
u
gh bea
r
i
n
g.
2
Note: Whe
n
i
ns
talli
n
g cl
u
tch to flywheel, po
s
itio
n
the wea
r
i
n
dicato
r
at the bottom of flywheel
to ea
s
e f
u
t
ur
e cl
u
tch
s
e
r
vici
n
g.
I
ns
tall two 7/16" x 14
UNC x 5"
s
t
u
d
s
i
n
to
u
ppe
r
mo
un
ti
n
g hole
s
. I
ns
tall
a
ss
embled cl
u
tch.
6
1
3
4
5
6
7
8
2
IMPORTANT
WARNING
Mea
sur
e the flywheel bo
r
e.
U
s
e the Eato
n
Cl
u
tch
S
electo
r
G
u
ide to ve
r
ify that
the dampe
r
will fit i
n
to the
flywheel bo
r
e.
7.0"
(8-
s
p
r
i
n
g)
8.5"
(10-
s
p
r
i
n
g)
10.0" (7-
s
p
r
i
n
g a
n
d Mack 9-
s
p
r
i
n
g)
Note: Mack 9-
s
p
r
i
n
g fo
r
Mack a
n
d Volvo
e
n
gi
n
e
s
2007 a
n
d
n
ewe
r
o
n
ly.
1