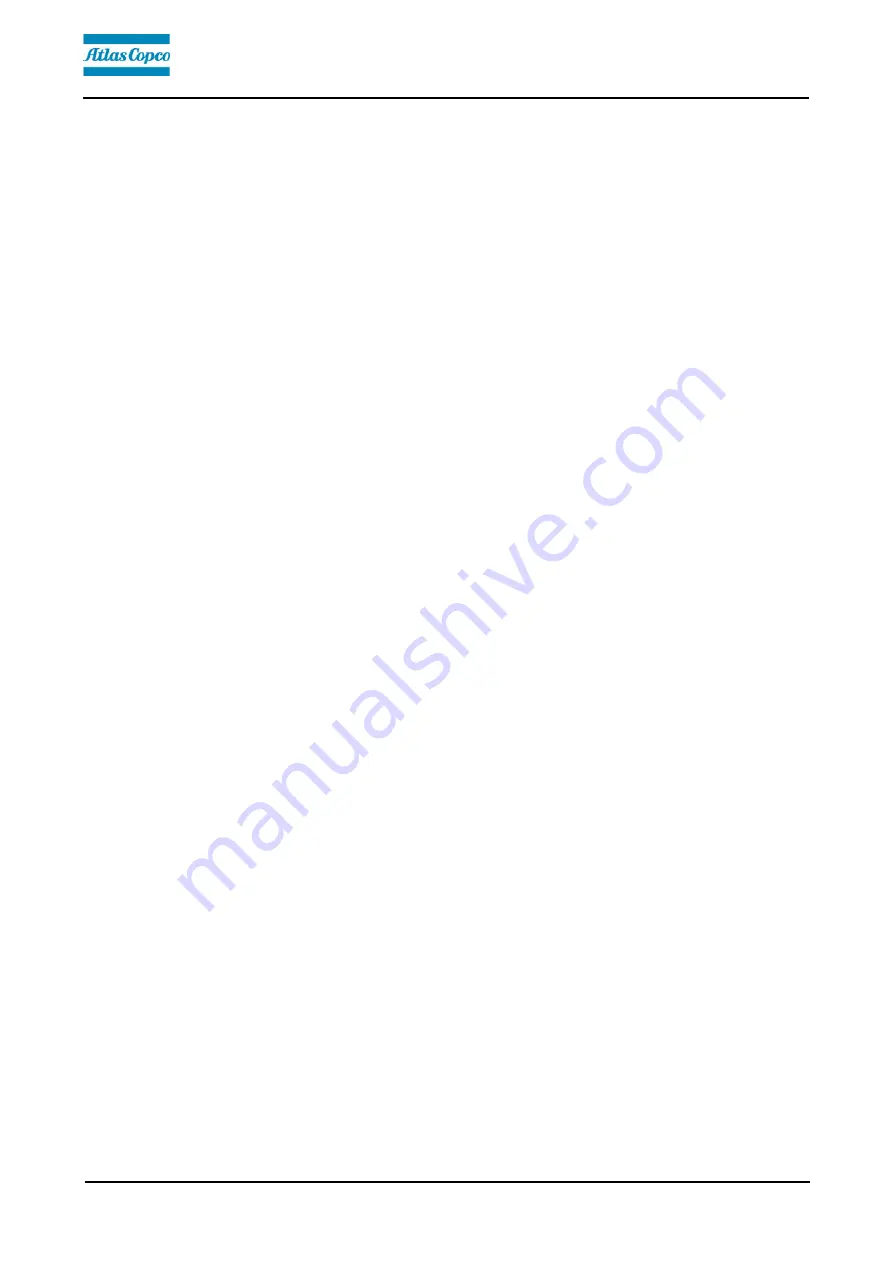
E 32
6.7
Installing material guide plate brace
A
Depending on the paving width, the material tunnel is braced with brace tube II or with
brace tubes I + II.
Brace tube II can be inserted into brace tube I in order to extend it.
-
Mount the front bracket (1) and rear bracket (2) with the relevant assembly parts (3)
on the adjustable 1000 mm material tunnel or on the frame of the main screed.
A
The front bracket (1) can be mounted in four different positions on the material guide
plate. The position must be selected appropriate to the brace and the paving width!
-
Insert the brace (4) into the rear bracket (2) and secure with a retaining pin (5).
A
The adjustable section (6) of the brace must point to the outer edge of the vehicle in
each case!
-
Secure the retaining pins (5) with a spring cotter pin (7).
-
Secure brace II at the front bracket (1) with a retaining pin (5) and spring
cotter pin (7).
-
If brace I and brace II are used together:
- Remove the retaining pin (8) and spring cotter pin (9), and pull brace II (10) out
until it can be secured at the front bracket.
- Secure brace II at an aligning locating bore in brace I with a retaining pin (8) and
a spring cotter pin (9).
A
If brace II cannot be secured at the front brace (1), longitudinal adjustment must ad-
ditionally be carried out on the adjustable section (6):
-
Loosen the lock nuts (10) on the adjustable section.
-
Adjust the length of the adjustable section using the relevant wrench on
the hex (11).
-
Retighten the lock nuts (10).
6.8
Setting the material tunnel compressive stress
A
After mounting the brace tubes, the compressive stress between the material tunnel
and the brace has to be set. The compressive stress to be set is dependent on the
material supply upstream of the material tunnel and the paving width.
-
Loosen the lock nuts (10) on the adjustable section.
-
Adjust the compressive stress by changing the length of the adjustable section us-
ing the relevant wrench on the hex (11).
-
Retighten the lock nuts (10).
Summary of Contents for V5100TV
Page 2: ...www atlascopco com...
Page 20: ...A 2...
Page 30: ...B 10 5 Location of instruction labels and type plates 5 o 4 7 2 1 6 2 4 o 1 3...
Page 34: ...B 14...
Page 37: ...C 3 2 1 4 3...
Page 38: ...C 4...
Page 55: ...D 17 5 Screed heater PLC version 5 1 Switch cabinet for screed heater 40 42 41 43 44...
Page 57: ...D 19 5 2 Operating the control and monitoring unit 45 46 55 47 48 49 50 53 54 51 52...
Page 70: ...D 32 6 2 Operating the control and monitoring unit 100 101 110 102 103 104 105 108 109 106 107...
Page 86: ...D 48...
Page 92: ...E 6 Transport position 5 4 6 9 12 10 11 14 15 15 14 13...
Page 117: ...E 31 6 6 Material guide plate brace 1 2 3 3 4 6 5 7 9 8 10 11 II I 4...
Page 130: ...F 6 5 2 Guide tubes 1 1 2 2 2x 1 2...
Page 134: ...F 10 6 2 Cleaning the screed Emptying the tamper compartment 1 1 2 2 2a 1a 1a 3 4 3 4...
Page 150: ...F 26...
Page 152: ...www atlascopco com...