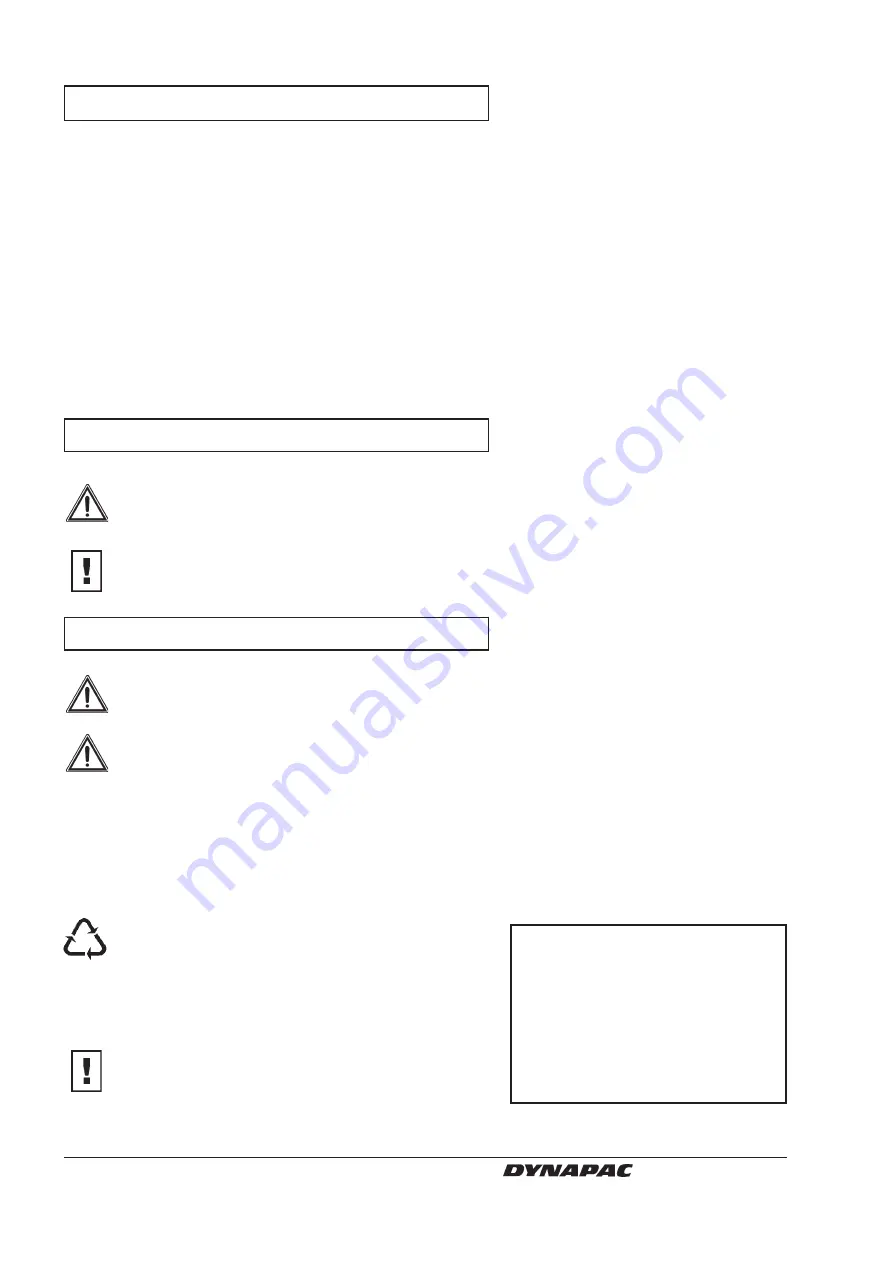
2
CP 132 M132EN3
Read through the entire manual before
starting any maintenance operations.
Ensure good ventilation (air extraction) if the
diesel engine is run indoors.
It is important that the roller is maintained correctly to
ensure proper function. It should be kept clean so that any
leakage, loose bolts and loose connections can be
discovered in time.
Make a habit of walking round the roller to check it every day
before starting the first shift – including under the machine.
This is often the easiest way of discovering any leakage.
SPARE A THOUGHT FOR THE
ENVIRONMENT! Do not let oil, fuel and other
environmentally hazardous substances contami-
nate the environment.
This manual contains instructions for periodic attention
which should normally be carried out by the roller’s driver.
There are additional instructions relating to the diesel
engine, for which the manufacturer’s instructions
are detailed in the engine manual. This is found
under a separate flap in the roller’s product binder.
CONTENTS
GENERAL
Safety instruction – Personal Safety
Special caution – Machine or component damage
WARNING SYMBOLS
WARNING
CAUTION
WARNING
WARNING
CAUTION
CALIFORNIA
Proposition 65 Warning
Diesel engine exhaust and some of its
constituents are known to the State of
California to cause cancer, birth defects,
and other reproductive harm.
Page
Lubricants and symbols ................................................... 3
Technical specifications ............................................... 4, 5
Maintenance schedule ..................................................... 6
Maintenance measures ................................................ 7, 8
Every 10 hours of operation (Daily) ............................ 9-13
Every 50 hours of operation (Weekly) ...................... 14-16
Every 250 hours of operation (Monthly) ................... 17, 18
Every 500 hours of operation (Every three months) ...... 19
Every 1000 hours of operation (Every six months) . 20, 21
Every 2000 hours of operation (Yearly) ......................... 22
Long-term parking .......................................................... 23
Special instructions ........................................................ 24
Electrical system, fuses ................................................. 25
Summary of Contents for CP 132
Page 2: ...19 ILF015WO1...