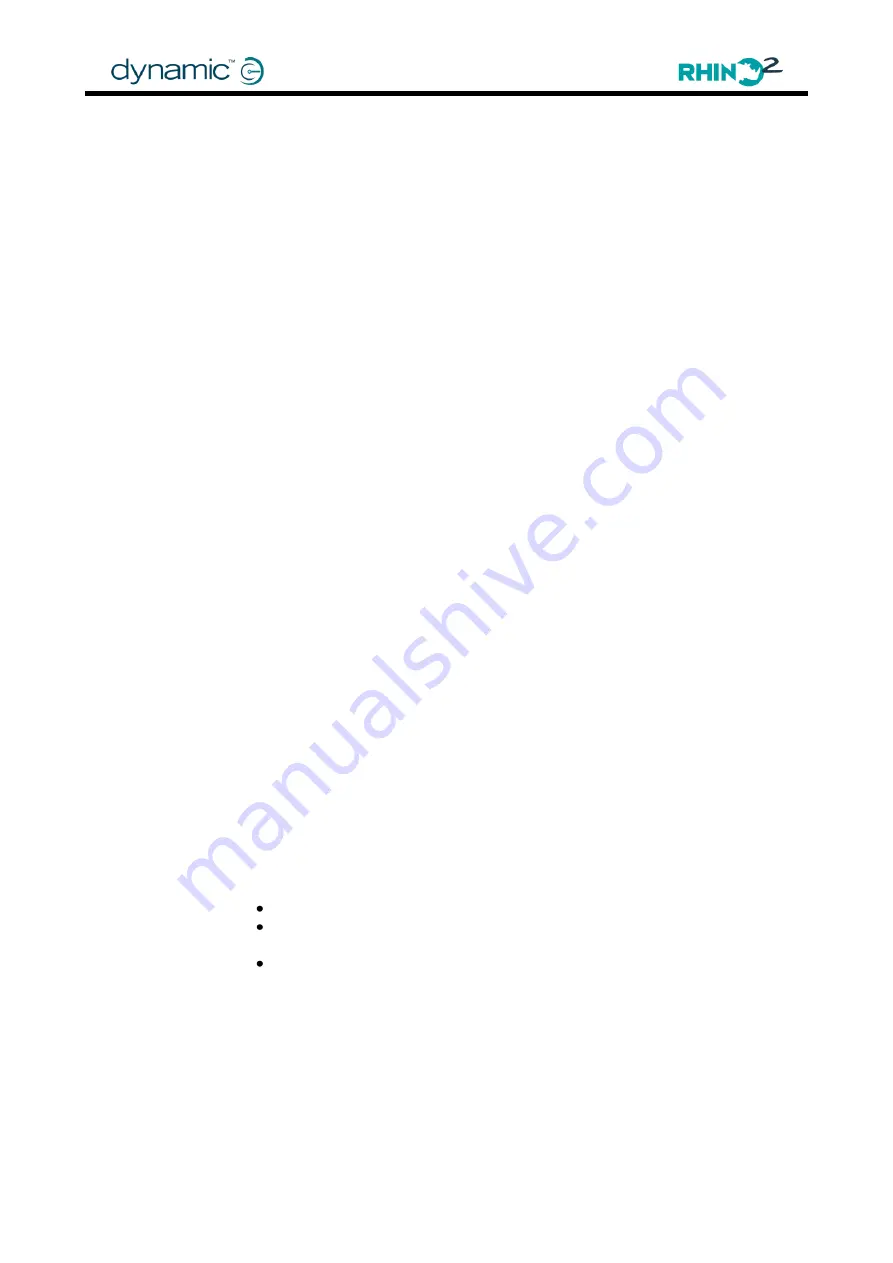
Chapter 4: Programming the Rhino2
101
Release Brake
- When this function is active, the park brake is released electrically, so
that it is possible to push the scooter. It is not possible to drive the scooter
while the park brake is released.
To prevent a rollaway situation while the park brake is released,
the scooter will stop if the speed during pushing is higher than the value
of the
parameter (4.4.3.13).
If the switch is active at power-up or is activated while driving, a park
brake fault flash code will show on the Status light, but the scooter will still
drive normally. In this case, the
Release Brake
function will be disabled
and the state of the associated input pin ignored until the power is
cycled.
Available on all input pins.
Charger Inhibit
- Stops the scooter at the programmed
inhibits drive. If
Latches
is set to 'Yes', the scooter must be turned off and on
before it is possible to drive again. If
Flashes
is set to 'Yes', the Status Light
will show a "Drive Inhibit" flash code while the drive inhibit is active. See
section 5.2 for more information on flash codes.
Note:
to make the charger inhibit pin compatible with the industry
standard where the inhibit signal must be connected to B- to activate
inhibit, set
Active
to 'Low'.
Available on pin 14 and P/I.
Profile 2
- When this function is active, the scooter switches to Profile 2 (see 4.4.3). A
typical application for Profile 2 is a user-selectable 'slow speed' mode that
can be used indoors, while Profile 1 is selected for outdoor use. Apart from
changing the maximum speed, the indoor profile can have its
acceleration and deceleration adjusted as well.
Available on all input pins.
Slow
- Limits the maximum speed of the scooter to the value that is set with
Slows To
. Has no effect on scooter acceleration or deceleration.
Slows To
is a percentage of
(4.4.3.1) or
Slows To
is set to 50%, the resulting maximum
speed will be half of 80%, which is 40%.
If
Slows To
is set to 0%, the function behaves the same as the 'Stop' state
of the
Slow/Stop
function (including latching and flashing), which is
described below. If
Slows To
is set higher than 0%, The
Slow
function does
not latch or flash.
Available on all input pins.
Slow/Stop
- This function has three states:
Normal drive
(pin not connected).
Slow
(2.2 kΩ connected to B+ if
Active
High or B- if
Active
Low).
Operates the same as the
Slow
function.
Stop
(pin connected to B+ if
Active
High or B- if
Active
Low).
Stops the scooter at the programmed
inhibits drive. If
Latches
is set to 'Yes', the scooter must be turned off and
on before it is possible to drive again. If
Flashes
is set to 'Yes', the Status
Light will show a "Drive Inhibit" flash code while the drive inhibit is active.
See section 5.2 for more information on flash codes.
Only valid
Active
settings are 'High' and 'Low', all other settings disable
the input (the input will never become active).
Available on all input pins.