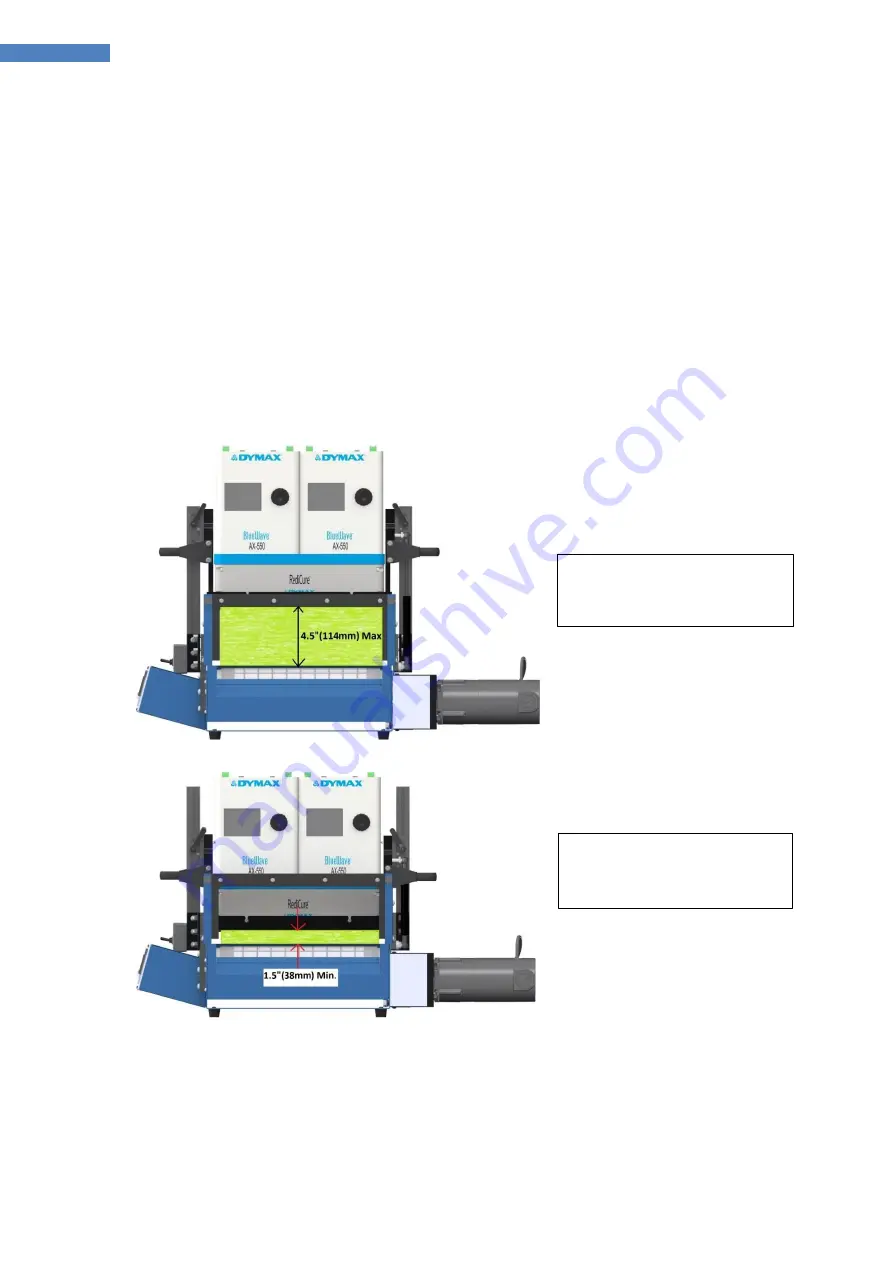
20
UVCS LED Light-Curing Conveyor Systems User Guide
Height Range and Working Distance
Height Range
The conveyor tunnel clearance height maximum
is 4.5” (114 mm) when the cradle is all the way up.
When the cradle
is all the way down the conveyor tunnel clearance is 1.5” (75
mm).
Working Distance
The distance between the glass lens on the emitter and the belt is called the working distance. Since the
emitter sits flush to the cradle the height adjustment range is also the working distance range.
Parts requiring smaller working distances than 1.5” (
75 mm) should be placed on a palette of appropriate
thickness to lift the workpiece off the belt and closer to the emitter.
Figure 30. Cradle Clearance at Minimum & Maximum Height
Cradle at maximum height
Tunnel clearance is 4.5” (114 mm)
Cradle at minimum height
Tunnel clearance is 1.5” (38 mm)