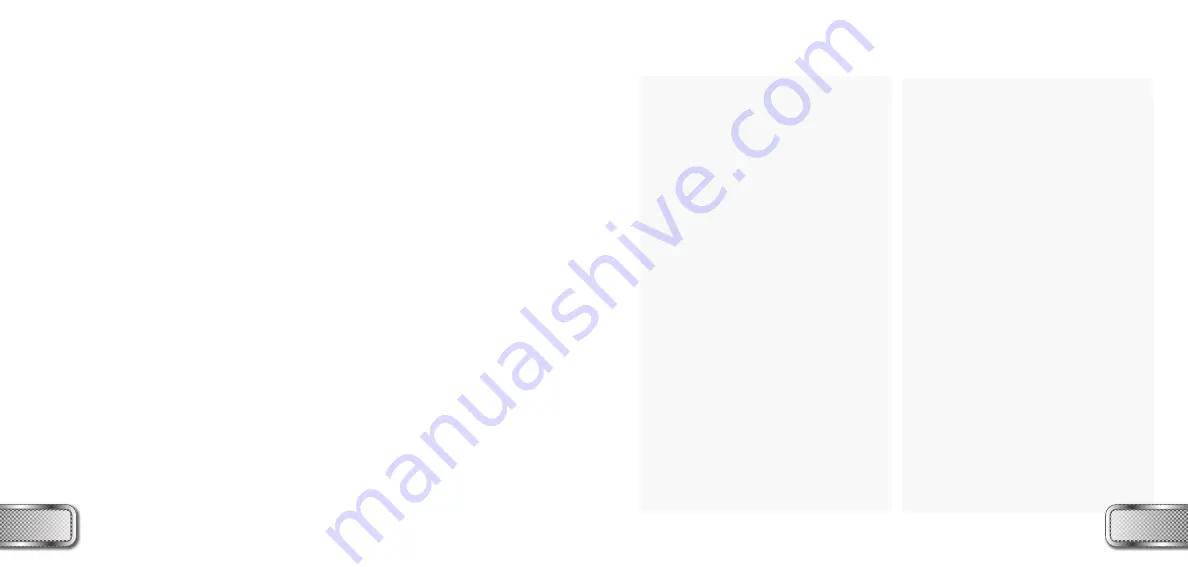
CONTACT PAD, CONTACT GRIP AND BUTTON COVER
The front rubber Contact Pad and Contact Grip are mounted to the Ultralite frame. It is not
necessary to remove the two contact pads when removing the frame from the body. The only
reason to remove the contact points is for general cleaning of built up dirt or paint.
REMOVAL OF CONTACT PADS
• Remove frame from body. Follow frame removal instructions on page 26
• Use a 3/32 Allen wrench to remove the front contact pad
• Use a 1/16 Allen wrench to remove the contact grip
BUTTON COVER REMOVAL
It may become necessary to remove the button cover if the buttons get stuck due to built up
paint or dirt.
• Unhook and open both sides of the tool-less sticky grips.
• Remove Hyper3™ regulator.
• Remove battery; use a small Phillips screwdriver. One can be found in the DYE Multi-Tool
that is included with the NT11.
• Unscrew the mounting screw found on the inside of the frame; use a Phillips screwdriver.
• To access the screw insert the screwdriver through the middle slot on the frame’s front strap.
• Once the screw is removed it may be necessary to push the button cover out from the back.
• Apply force to the lower button. This will push the cover out from the center and help
prevent binding.
• Take care not to lose the buttons as you remove the cover.
• Once removed, clean the button cover, buttons, and frame.
• When assembling the button retaining cover make sure the rounded ends of the
buttons face outward.
CONTACT PADS & BUTTON COVER
TROUBLESHOOTING GUIDE
AIR LEAKS
AIR LEAKING FROM THE BACK OF AIRPORT
•
Check the O-ring on the Air system. If needed
change the O-ring and try again. The O-ring
normally used is
015 O-ring
but some
manufacturers might use a different size. Consult
the manual of the air system you are using.
AIR LEAKING FROM THE FRONT
OF AIRPORT
•
Check that the hose connector is tight. Remove
the hose from the connector by pushing towards
the connector and pull out hose.
Use a crescent wrench to tighten the fitting.
If needed, remove and apply thread sealant to the
thread and re-tighten. If unsure, consult expert
advice.
• Check that the end of the hose is cut
straight and is not worn out. If needed cut a small
piece off the hose with a razor blade and re-insert
the hose into the fitting. Make sure the hose goes
all the way to the end.
AIR LEAKING FROM ON/OFF KNOB OR
BLEED HOLE
•
Make sure airport is in full on or off position.
• Check
005 O-ring
behind pin housing.
• See page 33 for service details.
AIR LEAKING FROM THE HYPER3™ REGULATOR
•
Locate the position of the leak.
•If the leak is coming from the bottom of the
regulator you will need to dis-assemble
the regulator and change the
010 O-ring
and
the seat
on the brass seat retainer mounted inside the
Hyper3™ regulator.
•If the leak is coming from the swivel piece where the
hose connector mounts you will need to change the
two
013 O-rings
under the swivel piece or tighten
the hose connector.
•If the leak comes from the small hole in the middle
of the regulator there are two possible O-rings
causing the problem, the
015 O-ring
on the piston
and the 007 urethane O-ring inside the body of the
regulator. These O-rings should be replaced by a
trained Tech.
• Change the 011 O-ring on the top cap of theHyper3™
and apply a small amount of lube to the O-ring.
• See page 22 for service details.
AIR LEAKING FROM THE ASA
•
Change the
011 O-ring
on the top cap of the
Hyper3™ and apply a small amount of lube to the
O-ring.
AIR LEAKING BETWEEN BODY AND FRAME
•
Inspect the two
020 O-rings
on the plunger, and
the
011 O-ring
at the front of the spacer rod. In
addition to the leak the gun may fire upon
degassing.
• If the leak begins after the NT11 is fired once change
the rear most
010 O-ring
on the spool. In addition,
inspect the spool plungers for excessive wear.
• Check the two air transfer hole plug screws.
• See page 26-27 for details.
W W W . D Y E P A I N T B A L L . C O M
W W W . D Y E P A I N T B A L L . C O M
34
35
Summary of Contents for NT11
Page 1: ... ...