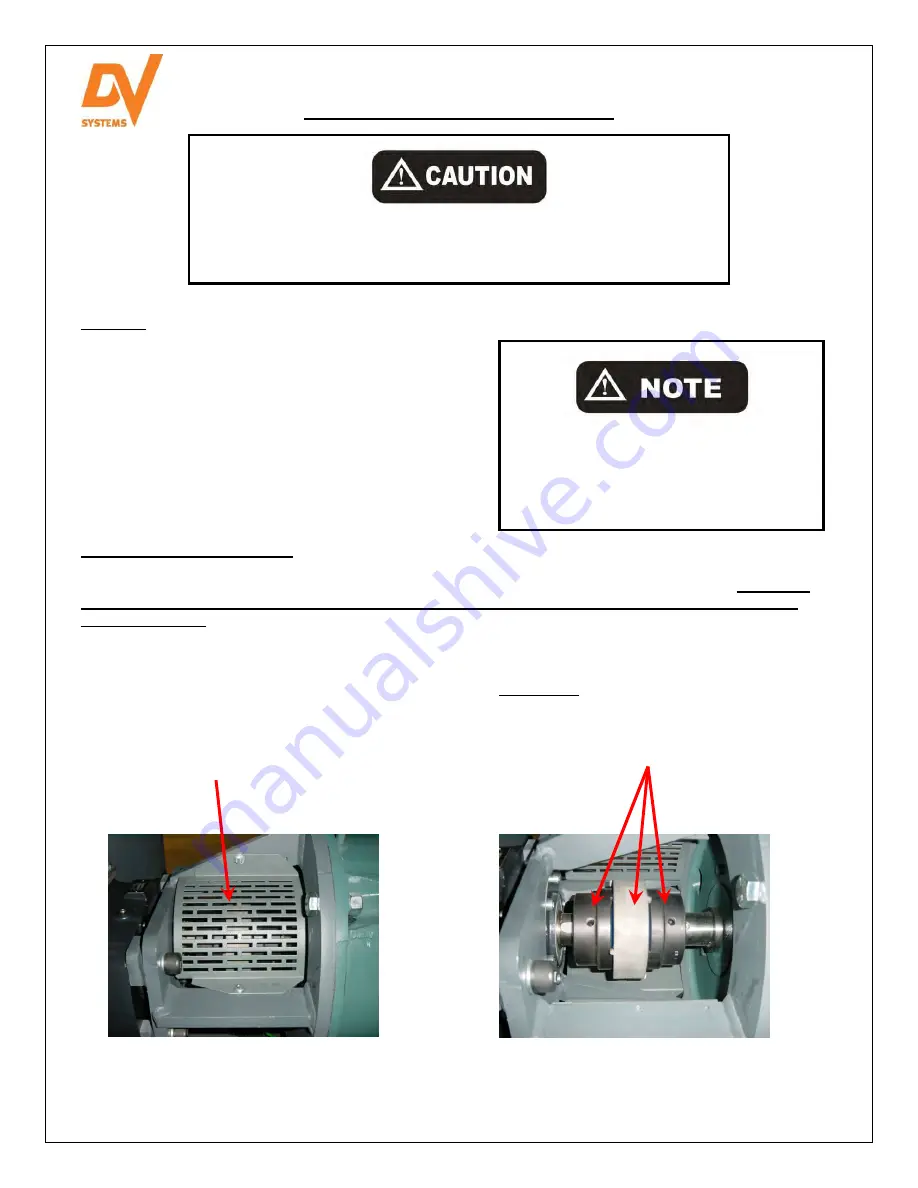
K100-C
Dec’15
- 13 -
Use of an incorrect Motor for your
particular building service will result in
premature Motor failure, and is not
covered by the DV Systems or Motor
Manufacturers Warranty.
Installation – Electrical (cont’d)
Motors.
Wiring must be done in a manner that the full Motor
nameplate v/- 10% is available at the Motor
terminals during start-up. Contact your local Distributor or
Service Centre if additional information is needed.
The Warranty that exists on the Electric Motor is that of the
original manufacturer. In the event of a Motor failure, contact
your DV Systems Distributor or Service Centre for the
location of the nearest authorized Motor Service Centre.
Motor / Air End Rotation.
It is critical that the Motor and Air End in the Rotary Screw Unit be turning in the correct manner as
the Unit is
not equipped with an ‘Anti Rotation Switch’. Irreparable damage will be done if the Unit rotates in the
reverse direction.
The correct rotation is as indicated at the Coupling area of the Unit.
Remove the Cover Plate from the Coupling area and pay close attention to the arrow indicating the
correct rotation.
To verify the correct rotation, start the Unit and turn off immediately using the Emergency Stop Button.
If the rotation is not correct, simply change two of the Motor Leads (‘T1’ and ‘T2’) at the Inverter.
Verify correct rotation again if required.
Do not attempt to operate the Unit without first checking whether there
is oil in the Oil Reservoir. Add oil as required. Serious damage may
result from use, however limited, without oil.
Cover Plate
Coupling