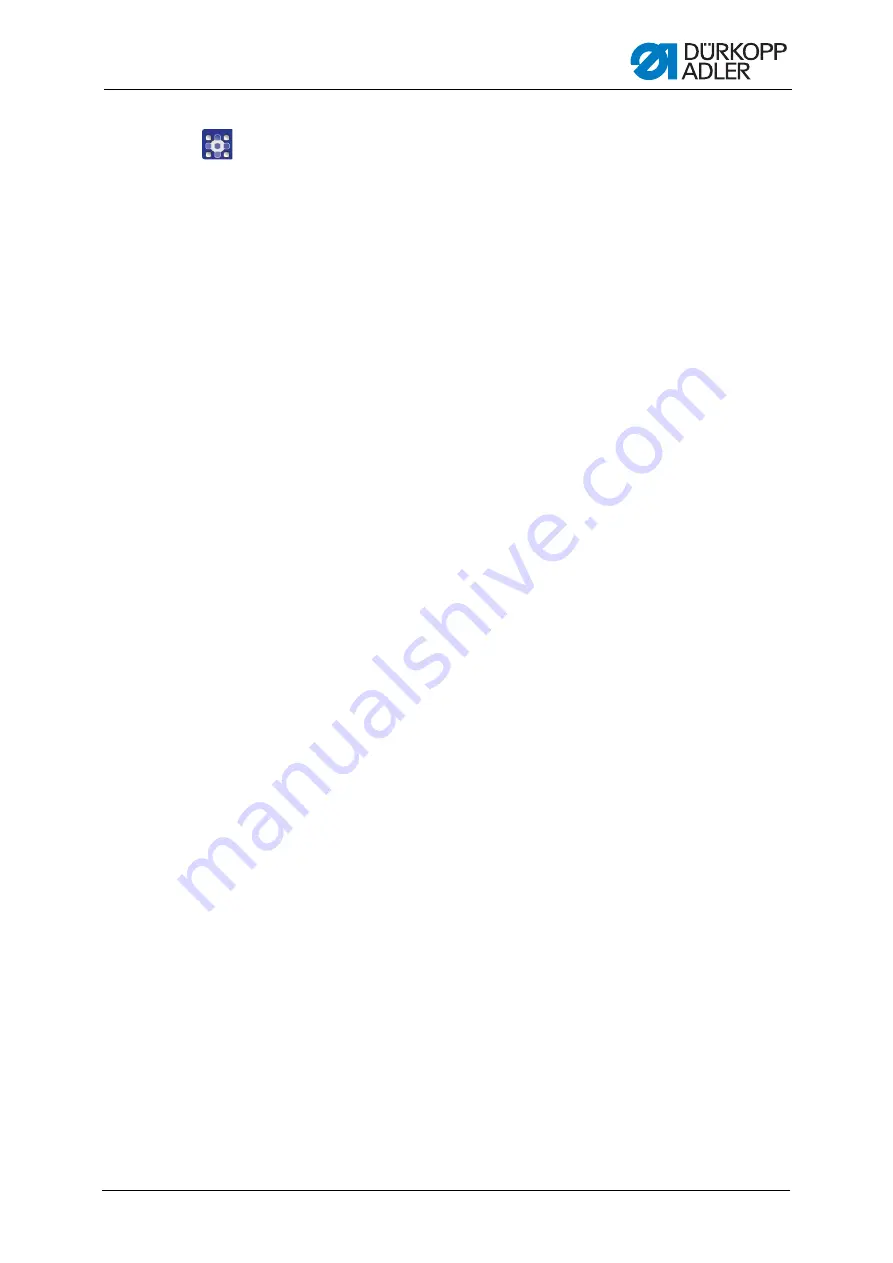
Creating programs with DA-CAD 5000
Service Instructions 911-211 - 02.0 - 10/2016
144
To transfer a program to the machine:
1.
Insert the USB key and copy the desired file to the DAC(
2.
Open the copied program (
3.
Adjust the program parameters (especially the sewing foot
height) (
4.
Perform a contour test to check the clamp motion (
Sewing with the program can begin after successful testing/adjustment.
Summary of Contents for 911-211
Page 1: ...Service Instructions 911 211...
Page 6: ...Table of Contents 5 Service Instructions 911 211 02 0 10 2016...
Page 10: ...About these instructions 9 Service Instructions 911 211 02 0 10 2016...
Page 90: ...Sewing unit 89 Service Instructions 911 211 02 0 10 2016...
Page 146: ...Creating programs with DA CAD 5000 145 Service Instructions 911 211 02 0 10 2016...
Page 158: ...Decommissioning 157 Service Instructions 911 211 02 0 10 2016...
Page 160: ...Disposal 159 Service Instructions 911 211 02 0 10 2016...
Page 170: ...Technical data 169 Service Instructions 911 211 02 0 10 2016...
Page 195: ...Appendix Service Instructions 911 211 02 0 10 2016 194...
Page 197: ...Appendix Service Instructions 911 211 02 0 10 2016 196 13 3 Pneumatic diagram...
Page 199: ......