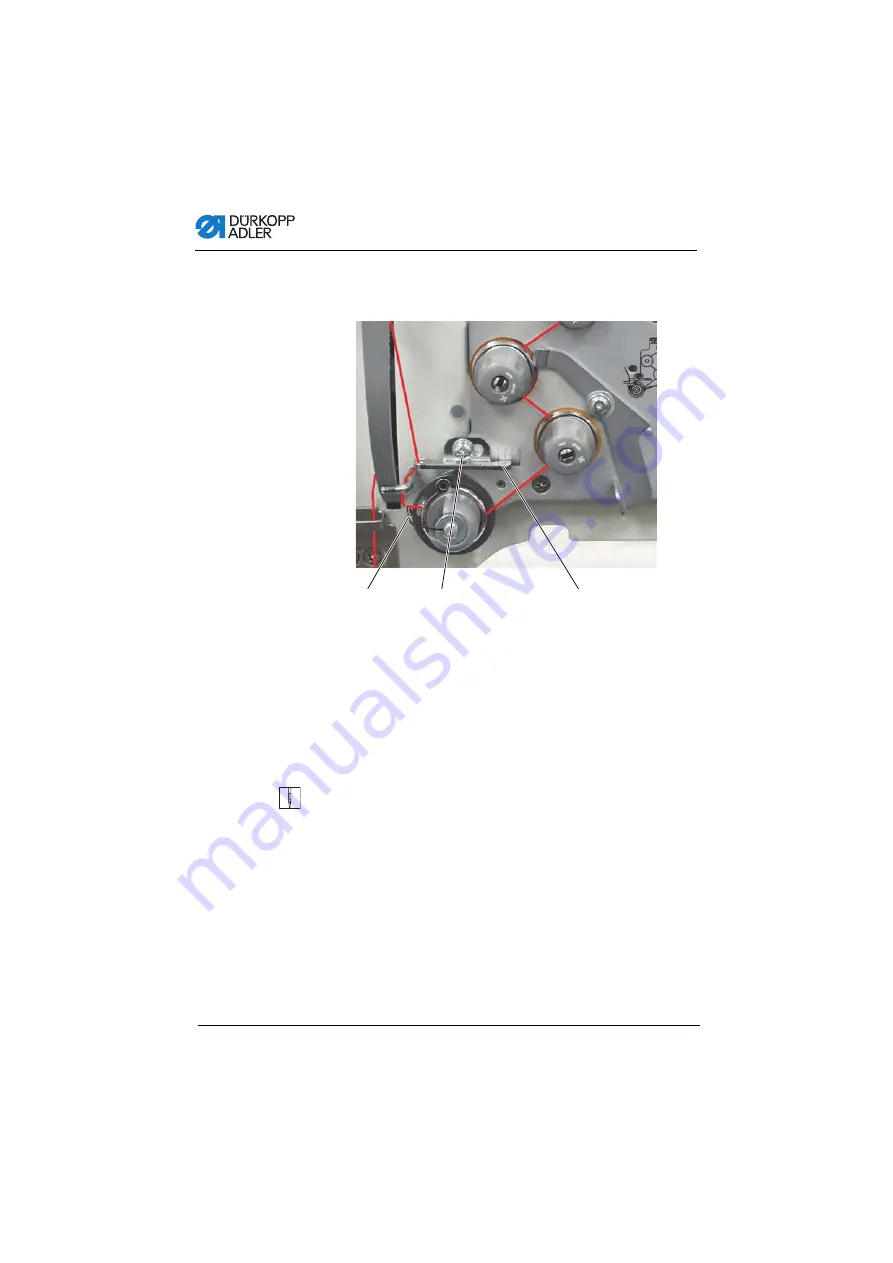
Operation
34
Operating Instructions 669 - 00.0 - 08/2019
4.7
Setting the needle thread regulator
Fig. 12: Setting the needle thread regulator
The neelde thread regulator (1) is used to control the quantity of
the needle thread required by the stitch formation.
The best sewing results can only be ensured when using a preci-
sely adjusted needle thread regulator (1).
At the properly adjusted setting, the needle thread loop must be
able to slide over the thickest section of the hook.
To set the needle thread regulator:
1. Loosen screw (2).
2. Change the position of the needle thread regulator (1).
• Thread regulator to the left:
more thread
• Thread regulator to the right:
less thread
3. Tighten screw (2).
(1) - Needle thread regulator
(2) - Screw
(3) - Thread take-up lever
①
②
③
Summary of Contents for 669 CLASSIC
Page 1: ...669 ECO CLASSIC Operating Instructions...
Page 6: ...Table of Contents 4 Operating Instructions 669 00 0 08 2019...
Page 16: ...Safety 14 Operating Instructions 669 00 0 08 2019...
Page 54: ...Operation 52 Operating Instructions 669 00 0 08 2019...
Page 108: ...Decommissioning 106 Operating Instructions 669 00 0 08 2019...
Page 110: ...Disposal 108 Operating Instructions 669 00 0 08 2019...
Page 114: ...Troubleshooting 112 Operating Instructions 669 00 0 08 2019...
Page 116: ...Technical data 114 Operating Instructions 669 00 0 08 2019...
Page 117: ......