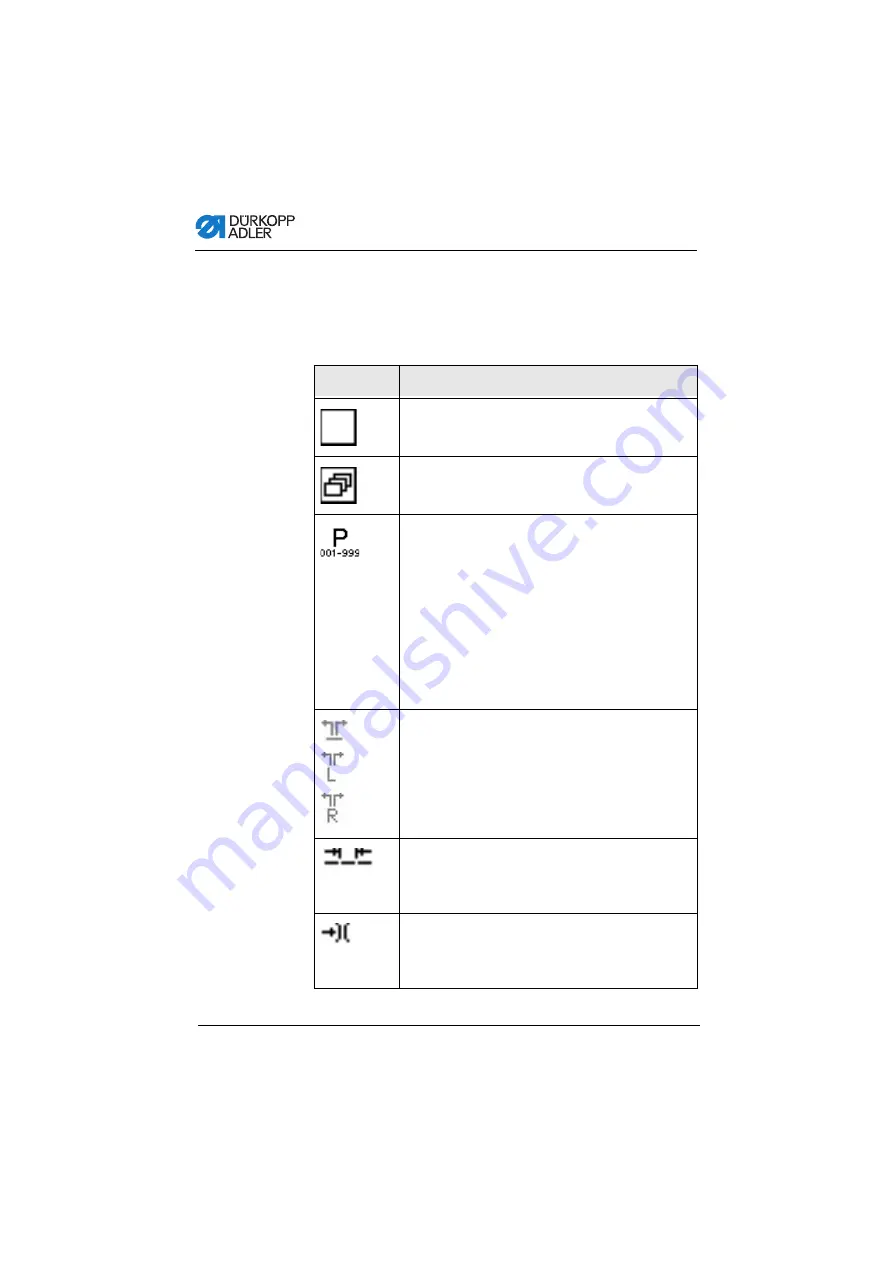
Programming
Operating Instructions 550-12-33/34 - 00.0 - 08/2017
74
5.4
Automatic mode
Automatic mode includes all seam programs from
001
–
999
.
The following table shows the individual symbols on the display
and the functions of the buttons on the control panel:
Button function and menu items on the display
Symbol
Meaning
Upper softkey
, can be assigned a softkey function
• Press the upper softkey.
Open the
softkey menu
.
• Press the lower softkey.
Seam program number
Value range: 001 – 999
Automatic mode allows for the execution of seam
programs
001
-
999
.
• Use
/
to select the parameter.
• Use
/
to change the seam program number.
OR:
• Enter the seam program number directly using one of
the numeric buttons
0
–
9
and press
OK
to confirm if
necessary.
The control switches to automatic mode, and the
corresponding seam program is active:
Right/left piece
• Use
/
to select between the right/left piece
(if programs exist for both).
Stitch length
Value range: 3.0 – 6.0 mm
• Use
/
to select the parameter.
• Use
/
to change the stitch length.
Needle thread tension
Value range: 1 – 99
• Use
/
to select the parameter.
• Use
/
to change the needle thread tension.
Summary of Contents for 550-12-33
Page 1: ...550 12 33 34 Operating Instructions...
Page 6: ...Table of Contents 4 Operating Instructions 550 12 33 34 00 0 08 2017...
Page 16: ...Safety 14 Operating Instructions 550 12 33 34 00 0 08 2017...
Page 20: ...Machine description 18 Operating Instructions 550 12 33 34 00 0 08 2017...
Page 126: ...Programming Operating Instructions 550 12 33 34 00 0 08 2017 124...
Page 140: ...Maintenance 138 Operating Instructions 550 12 33 34 00 0 08 2017...
Page 158: ...Setup 156 Operating Instructions 550 12 33 34 00 0 08 2017...
Page 160: ...Decommissioning 158 Operating Instructions 550 12 33 34 00 0 08 2017...
Page 162: ...Disposal 160 Operating Instructions 550 12 33 34 00 0 08 2017...
Page 184: ...Troubleshooting 182 Operating Instructions 550 12 33 34 00 0 08 2017...
Page 188: ...Technical data 186 Operating Instructions 550 12 33 34 00 0 08 2017...
Page 190: ...Appendix 188 Operating Instructions 550 12 33 34 00 0 08 2017 Fig 97 Wiring diagram...
Page 191: ...Appendix Operating Instructions 550 12 33 34 00 0 08 2017 189 Fig 98 Wiring diagram...
Page 192: ...Appendix 190 Operating Instructions 550 12 33 34 00 0 08 2017 Fig 99 Wiring diagram...
Page 193: ...Appendix Operating Instructions 550 12 33 34 00 0 08 2017 191 Fig 100 Wiring diagram...
Page 194: ...Appendix 192 Operating Instructions 550 12 33 34 00 0 08 2017 Fig 101 Wiring diagram...
Page 198: ...Appendix 196 Operating Instructions 550 12 33 34 00 0 08 2017...
Page 199: ......