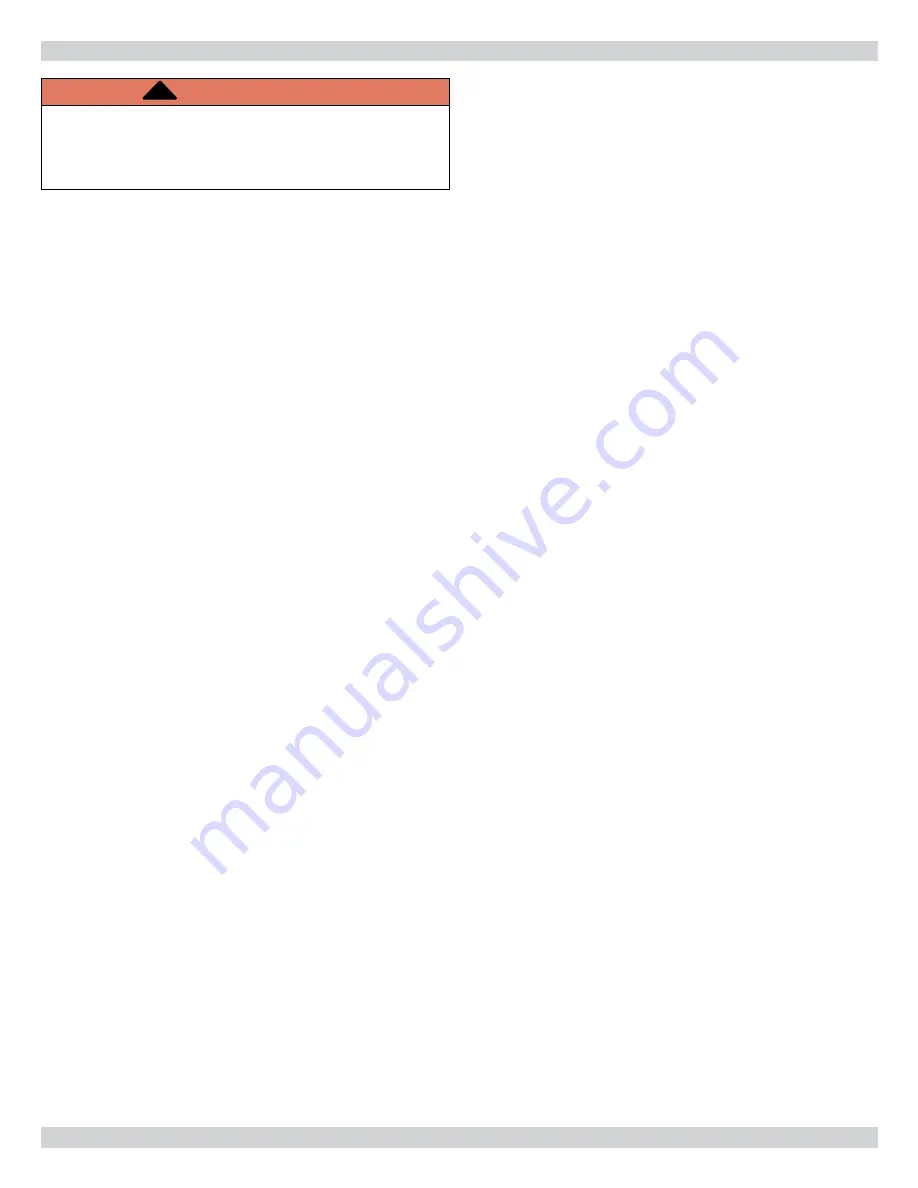
47
Important
1.
In reset from lockout condition, all electrical meter
readings at the gas control valve (24 vac) must be
taken within trial for ignition period.
2.
If any component does not function properly, make
sure it is correctly installed and wired before replacing
it.
3.
Static electricity discharge can damage integrated
boiler control (IBC). Touch metal surface to discharge
static electricity before touching IBC.
4.
IBC cannot be repaired. If it malfunctions it must be
replaced.
5.
Only trained service technicians should service IBC
systems. Following troubleshooting, check out system
following sequence of operation for a normal light off
sequence.
6.
All controls are factory tested in the assembly process
and a defective control is generally the least likely
cause. If you suspect you have a defective control,
read through this section before you replace it.
7.
It is extremely unlikely that the two consecutive
controls are defective. If it seems to be happening,
chances are that either there is nothing wrong with the
control or it is being damaged by some other problem
(an electrical short burning out a transformer, for
example).
Initial Service Checks
1.
Before troubleshooting:
A. Make sure that circuit breaker is on or fuse is ok at
electrical panel.
B. Make sure that service switch is on.
C. Make sure that gas is on at the gas meter, at all
appropriate manual shutoff valves and at the gas
control valve.
D. Make sure that the thermostat is calling for heat.
E. Check that wire connectors at the integrated boiler
control and at the originating control are securely
plugged in or connected.
F. Check that hoses are securely connected and are
not plugged or damaged.
TROUBLESHOOTING
2.
Troubleshooting tools:
A. Voltmeter to check 120 vac and 24 vac
B. Continuity tester.
C. Inclined manometer or pressure gauge with
0-3.0” Range (0.01” Scale) for measuring suction
pressures at pressure switch.
D. U-tube manometer or differential pressure gauge
with 0-14” range (0.1” Scale) for measuring inlet
and manifold gas pressures.
3.
IBC Error Codes.
A. IBC uses advanced diagnostic capability to assist in
troubleshooting error conditions. Table 10, Page 48
shows error codes that may arise during fault
condition.
B. State Conditions shown in
Table 9, Page 40
provide
suggestions for servicing these potential errors.
WARNING
Fire, explosion or shock hazard. Do not attempt to
modify the physical or electrical characteristics of
this boiler in any way. Failure to comply could result
in death or serious injury.
!
Summary of Contents for Q90-100
Page 2: ...2 DIMENSIONS 2 Figure 1 Boiler Dimensions...
Page 12: ...12 NEAR BOILER PIPING Figure 2 Single Zone Boiler Piping...
Page 14: ...14 Figure 4 Two Zone Boiler Piping With Circulators NEAR BOILER PIPING...
Page 19: ...19 Figure 9 Diaphragm Type Expansion Tank Piping NEAR BOILER PIPING...
Page 20: ...20 Figure 10 Conventional Closed Type Expansion Tank Piping NEAR BOILER PIPING...
Page 24: ...24 Figure 12 Roof Vent Intake Terminations COMBUSTION AIR AND VENT PIPE VENT AIR INTAKE...
Page 32: ...32 Figure 21 Ladder Wiring Diagram ELECTRICAL WIRING...
Page 34: ...34 Figure 23 Ladder Diagram for Figure 22 ELECTRICAL WIRING...
Page 40: ...40 S9381A INTEGRATED BOILER CONTROL OPERATION AND ADJUSTMENTS Table 9 State Code Definitions...
Page 41: ...41 S9381A INTEGRATED BOILER CONTROL OPERATION AND ADJUSTMENTS Figure 26 Sequence of Operation...
Page 48: ...48 TROUBLESHOOTING Table 10 Error Codes...
Page 55: ...NOTES...
Page 56: ...DUNKIRK BOILERS 2201 Dwyer Avenue Utica NY 13501 web site www ecrinternational com...