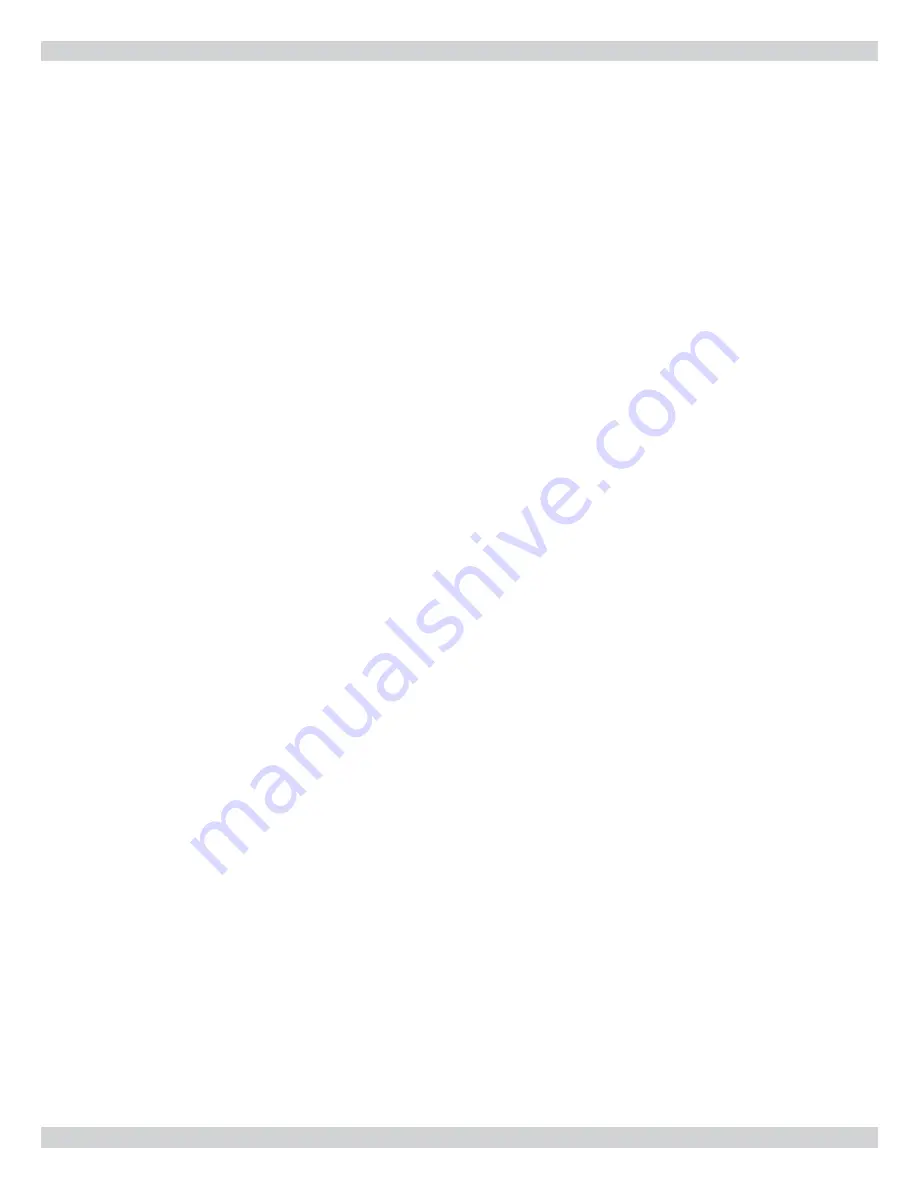
36
Casting Temperature Safety Switch
In event of lack of or loss of water in boiler, Casting
Temperature Safety Switch (300 °F setpoint) installed
on top of the aluminum boiler section shuts off boiler by
shutting off power to Integrated Boiler Control (IBC). This
fault requires manual reset of casting temperature safety
switch to restart the boiler. Verify that boiler is properly
fi
lled with water before resetting this switch.
Never run cold water into a hot empty boiler.
Differential Pressure Air Proving Switch/Blocked
Vent Safety Shutoff
Differential pressure switch monitors air
fl
ow by sensing
differential pressure measured in inches of water (” w.c.).
Pressure switch contacts close when draft inducer is
running. Closed switch indicates there is adequate air
fl
ow
for combustion. Pressure switch shuts off main burner if
differential pressure is inadequate due to blocked vent pipe,
blocked air intake, blocked boiler sections, or blocked draft
inducer. If pressure switch contacts fail to close control will
display Error Code 29.
Draft Inducer
Draft inducer (blower) provides means for pulling
combustion air into and through the mixer, burner,
fl
ue
ways of cast aluminum boiler sections and
fl
ue adapter
before being discharged through vent piping to outdoors.
See applicable sections for proper sizing and installation of
combustion air and vent piping in this manual.
Circulator Pump
Every forced hot water system requires at least one
circulating pump.
Circulating pump imparts the necessary energy to move
water through closed loop supply and return piping
systems, terminal heating equipment (i.e.
fi
nned tube
radiators, etc.) and back through boiler for reheating.
To provide required hot water
fl
ow rates, circulator pump
must be properly sized to overcome frictional losses
(usually measured in feet of water, also referred to as
“pump head loss”) of supply and return piping systems and
boiler.
The circulator pump is furnished for single zone or zone
valve controlled heating system and should be located on
downstream (i.e., pumping away) side of expansion tank.
For pump controlled system (where there is a circulator for
each zone) circulator provided with boiler can work for one
zone. For more details on piping and circulators, see “Near
Boiler Piping” on page 11 .
Drain Valve
Manual drain valve provides means of draining water in
heating system, including boiler and hot water supply and
return piping systems installed above drain valve. This
drain valve is installed in ¾” tapping at bottom of front
boiler section. Any piping installed below elevation of
this drain valve will require additional drain valves to be
installed at low points in piping systems in order to drain
entire system.
A.S.M.E. Rated Pressure Relief Valve
Each boiler must have a properly sized and installed
American Society of Mechanical Engineers rated pressure
relief valve. Water expands as it is heated by burner/
boiler sections. If there is no place for water to expand
its volume, (i.e. a properly sized and properly functioning
expansion tank) pressure on inside of boiler and heating
system will increase. Furnished relief valve automatically
opens at 30 psig pressure to relieve strain on boiler and
heating system from increasing pressure. Pressure relief
valve discharge must be piped with piping same size as
valve discharge opening to open drain, tub or sink, or
other suitable drainage point not subject to freezing, in
accordance with A.S.M.E. speci
fi
cations and requirements
of local jurisdiction.
External Condensate Pump (Optional)
For installations where there is no
fl
oor drain or other
appropriate drainage receptacle available to receive
condensate from the boiler, an external
fl
oat activated
condensate pump with integral sump is required. This unit
can be installed to pump the condensate to a remote tie in
point to a sanitary sewer system. For this application, the
boiler must be installed so that proper pitch of piping to the
external condensate reservoir (sump) can be accomplished.
Use wood frame or blocks to raise boiler as required for
proper installation.
CONTROLS AND ACCESSORIES
Summary of Contents for Q90-100
Page 2: ...2 DIMENSIONS 2 Figure 1 Boiler Dimensions...
Page 12: ...12 NEAR BOILER PIPING Figure 2 Single Zone Boiler Piping...
Page 14: ...14 Figure 4 Two Zone Boiler Piping With Circulators NEAR BOILER PIPING...
Page 19: ...19 Figure 9 Diaphragm Type Expansion Tank Piping NEAR BOILER PIPING...
Page 20: ...20 Figure 10 Conventional Closed Type Expansion Tank Piping NEAR BOILER PIPING...
Page 24: ...24 Figure 12 Roof Vent Intake Terminations COMBUSTION AIR AND VENT PIPE VENT AIR INTAKE...
Page 32: ...32 Figure 21 Ladder Wiring Diagram ELECTRICAL WIRING...
Page 34: ...34 Figure 23 Ladder Diagram for Figure 22 ELECTRICAL WIRING...
Page 40: ...40 S9381A INTEGRATED BOILER CONTROL OPERATION AND ADJUSTMENTS Table 9 State Code Definitions...
Page 41: ...41 S9381A INTEGRATED BOILER CONTROL OPERATION AND ADJUSTMENTS Figure 26 Sequence of Operation...
Page 48: ...48 TROUBLESHOOTING Table 10 Error Codes...
Page 55: ...NOTES...
Page 56: ...DUNKIRK BOILERS 2201 Dwyer Avenue Utica NY 13501 web site www ecrinternational com...