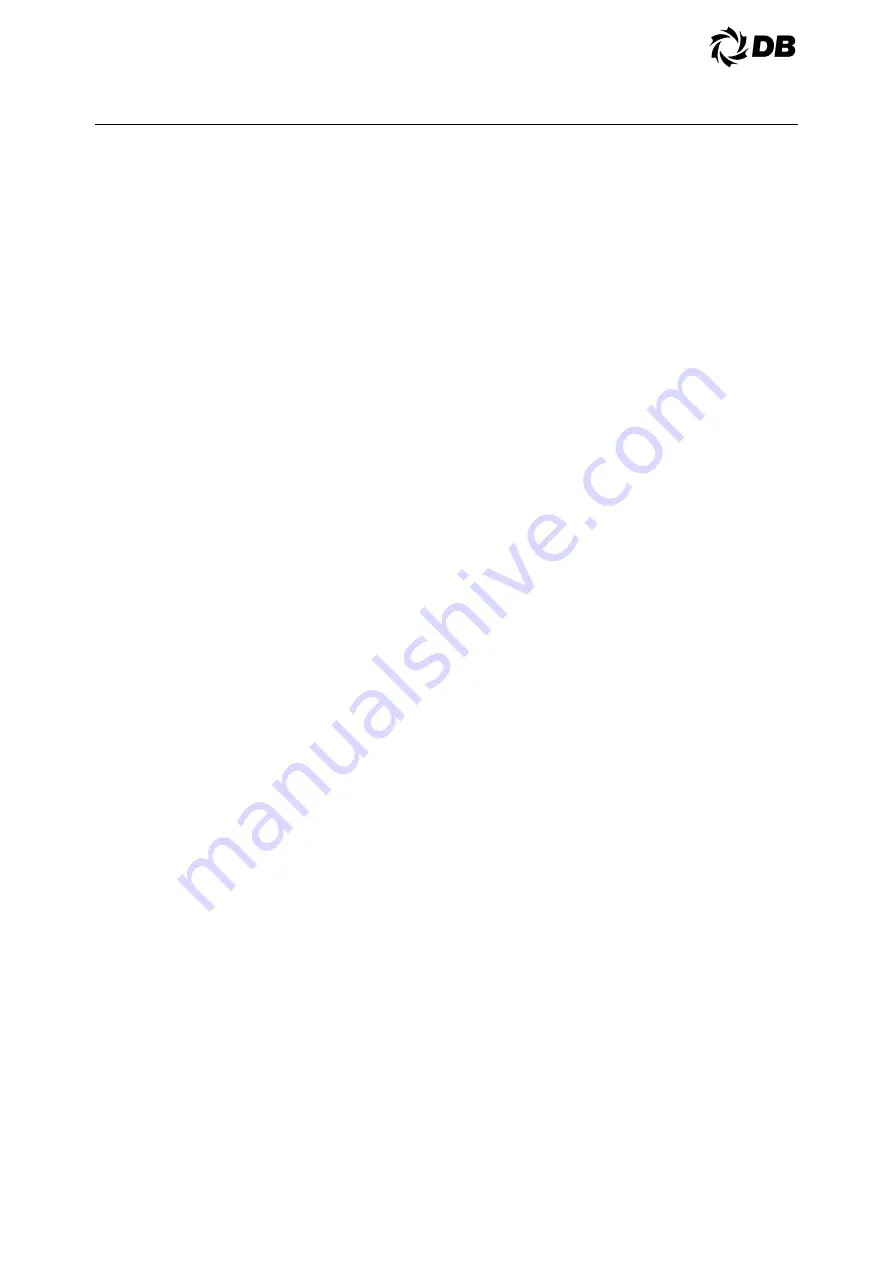
- 48 -
4.0 ELECTRICAL
ST2 OFF setpoint, plus the value in the COND
DIFF OFF setpoint for each stage number above
stage 2. Stage 2 of condenser staging will be
turned off based upon the value in the setpoint
(COND ST2 OFF). See below for an example of
condenser staging.
4.4.2 INCREASING
CONDENSER
PRESSURE
(Example of 4 stage fan cycling)
COND FAN1 ON when discharge pressure is >
230psig [15.9BAR] (COND Stage 1 ON setpoint)
COND FAN2 ON when discharge pressure is >
250psig [17.2BAR] (COND Stage 1 ON plus
1xCOND DIFF ON setpoint values)
COND FAN3 ON when discharge pressure is >
270psig [18.6BAR] (COND Stage 1 ON plus
2xCOND DIFF ON setpoint values)
COND FAN4 ON when discharge pressure is >
290psig [20.0BAR] (COND Stage 1 ON plus
3xCOND DIFF ON setpoint values)
And so on for the number of condenser fans
supplying the circuit.
4.4.3 DECREASING
CONDENSER
PRESSURE
(4 fan example "continued")
COND FAN4 OFF
when discharge pressure
is < 200psig [13.8BAR] (COND Stage 2 OFF plus
2xCOND DIFF OFF setpoint values)
COND FAN3 OFF
when discharge pressure
is < 190psig [13.1BAR] (COND Stage 2 OFF plus
1xCOND DIFF OFF setpoint values)
COND FAN2 OFF
when discharge pressure
is < 180psig [12.4BAR] (COND Stage 2 OFF
setpoint value)
COND FAN1 OFF
when discharge pressure
is < 170psig [11.7BAR] (COND Stage 1 OFF
setpoint value)
4.4.3.1 Adaptive Control Logic
The controller enhances the condenser
control logic above with a unique,
adaptive, self-learning fan control logic.
These enhancement results in a control
scheme that offers reduced fan cycling
and improved efficiency. Adaptive
Control Logic automatically adjusts the
fan cut-in offset based upon the
following criteria:
1. If the last fan turned on (including
FAN 1) is cycled off in 10 minutes
or less, then a COND ON OFFSET
value will be incremented by 5 psig
[0.3BAR]. This increases the fan 1
turn on value (COND ST1 ON plus
COND ON OFFSET) which in turn
increases all of the fan turn on
settings. This process will continue
until fan cycling ceases or the
adjusted turn on point for the last
fan stage is 320 psig [22.1BAR].
This will also be a setpoint.
2. The cut-in offset (COND ON
OFFSET) will be decreased by 5
psig [0.3BAR] if the last fan to be
turned on has not cycled off within
1 hour. The offset will continue to
decrease by 5 psig [0.3BAR] every
10 minutes unless fan cycling
begins again.
The Adaptive Control Logic will only
affect the condenser fan turn on logic, it
will not affect the fan turn off logic.
4.5 Master/Slave
Control
Sequence
The optional master/slave control sequence is
used to sequence multiple chillers in one
installation according to the building load demand.
It also controls the dedicated chilled water pump
or motorized valve.
Vision2020i Controller offers this feature with
minimized field wiring cost compare to
conventional method that involves lots of
hardware cost. It is carried out this control
function via the advanced DBLAN communication
bus to implement the network management for
multiple chillers lead/lag communication,
sequencing and monitoring.
Summary of Contents for ACDS
Page 7: ...7 2 0 INSTALLATION FIGURE 2 3 2 ACDS RIGGING ACDS 010 ACDS 020...
Page 8: ...8 2 0 INSTALLATION ACDS 030 040 050 060 070 ACDS 080 090 100 120 ACDS 135 150 165 180...
Page 9: ...9 2 0 INSTALLATION FIGURE 2 4 2B DIMENSIONAL DATA ACDS 010...
Page 10: ...10 2 0 INSTALLATION ACDS 020...
Page 11: ...11 2 0 INSTALLATION ACDS 030...
Page 12: ...12 2 0 INSTALLATION ACDS 040...
Page 13: ...13 2 0 INSTALLATION ACDS 050 060 070...
Page 15: ...15 2 0 INSTALLATION ACDS 100 120...
Page 19: ...19 2 0 INSTALLATION ACDS 030 040 050 060 070 ACDS 080 090 100 120 135 150 ACDS 165 180...
Page 22: ...22 2 0 INSTALLATION FIGURE 2 7A FIGURE 2 7B FIGURE 2 7C FIGURE 2 7D FIGURE 2 7E...
Page 25: ...25 3 0 OPERATION FIGURE 3 2 1 TYPICAL PIPING SCHEMATIC ACDS 010 020 030...
Page 26: ...26 3 0 OPERATION ACDS 040 050 060 070...
Page 27: ...27 3 0 OPERATION ACDS 080 090 100 120...
Page 28: ...28 3 0 OPERATION ACDS 135 150...
Page 29: ...29 3 0 OPERATION ACDS 165 180...
Page 54: ...54 4 0 ELECTRICAL 4 9 TYPICAL WIRING SCHEMATIC ACDS 010...
Page 55: ...55 4 0 ELECTRICAL...
Page 56: ...56 4 0 ELECTRICAL ACDS 020...
Page 57: ...57 4 0 ELECTRICAL...
Page 58: ...58 4 0 ELECTRICAL ACDS 030...
Page 59: ...59 4 0 ELECTRICAL...
Page 60: ...60 4 0 ELECTRICAL ACDS 040...
Page 61: ...61 4 0 ELECTRICAL...
Page 62: ...62 4 0 ELECTRICAL ACDS 050 060 070...
Page 63: ...63 4 0 ELECTRICAL...
Page 64: ...64 4 0 ELECTRICAL ACDS 080 90...
Page 65: ...65 4 0 ELECTRICAL...
Page 66: ...66 4 0 ELECTRICAL...
Page 67: ...67 4 0 ELECTRICAL...
Page 68: ...68 4 0 ELECTRICAL ACDS 100...
Page 69: ...69 4 0 ELECTRICAL...
Page 70: ...70 4 0 ELECTRICAL...
Page 71: ...71 4 0 ELECTRICAL...
Page 72: ...72 4 0 ELECTRICAL ACDS 120...
Page 73: ...73 4 0 ELECTRICAL...
Page 74: ...74 4 0 ELECTRICAL...
Page 75: ...75 4 0 ELECTRICAL...
Page 76: ...76 4 0 ELECTRICAL ACDS 135...
Page 77: ...77 4 0 ELECTRICAL...
Page 78: ...78 4 0 ELECTRICAL...
Page 79: ...79 4 0 ELECTRICAL...
Page 80: ...80 4 0 ELECTRICAL ACDS 150...
Page 81: ...81 4 0 ELECTRICAL...
Page 82: ...82 4 0 ELECTRICAL...
Page 83: ...83 4 0 ELECTRICAL...
Page 84: ...84 4 0 ELECTRICAL ACDS 165 180...
Page 85: ...85 4 0 ELECTRICAL...
Page 86: ...86 4 0 ELECTRICAL...
Page 87: ...87 4 0 ELECTRICAL...