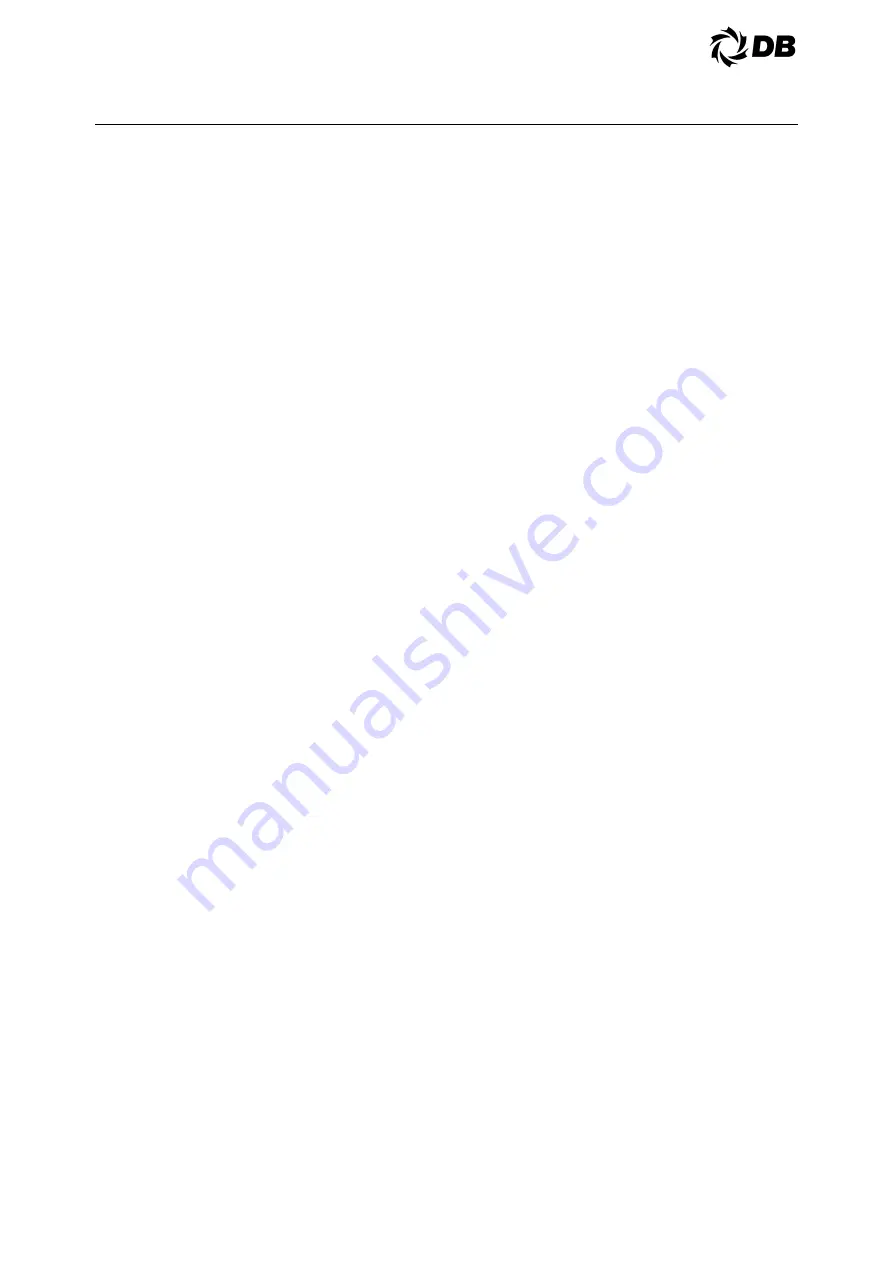
- 21 -
2.0 INSTALLATION
2.7 PIPING
CONNECTIONS
2.7.1 WATER
CONNECTIONS
CHILLED WATER PIPING
After the unit has been leveled, the
external water piping may be set up. Be
sure that the water piping is connected to
the corresponding connectors. The water-
outlet connection of the evaporator is
closest to the expansion valve (refrigerant
circuit) end.
Water flow through the evaporator must
remain constant for proper chiller
operation. Water pressure gauges are
recommended to check the water
pressure and flow rate in the system,
before and after the evaporator, and to
determine if variations occur in the
evaporator and system. When installing
pressure taps to measure the amount of
pressure drop across the water side of
the evaporator, the taps should be
located at least twenty-four (24) inches
[610mm] downstream from any
connections (flange, elbow, etc.) in the
water piping.
There are many piping and control
systems which may be used to ensure
constant water flow through the
evaporator. A typical system is shown in
Figure 2.7A. A three-way motorized
valve, which operates in response to the
discharge air temperature of the cooling
coil, is used.
Another system which is sometimes used
consists of a two-way modulating control
valve, which also responds to the
discharge air temperature of the cooling
coil, used with a spring loaded bypass
regulating valve as shown in Figure 2.7B
The bypass valve must be set to ensure
full flow of circulating chilled water when
the modulating valve is completely
closed.
Other systems are noted in the ASHRAE
Handbook and may operate equally well.
Whatever the system is selected, the
water flow must be constant.
2.7.2 WATER CONNECTIONS -
Multiple Packaged Chillers
Multiple unit package chillers have been
successfully applied to parallel and series
piping systems for years. Special
attention, however, must be given to the
particulars involved for each application
or serious operational problems can
result. The following guidelines should be
followed for multiple unit application.
It is assumed that the chilled water flow
rate is constant.
2.7.2.1 Parallel Chilled Water Flow Units
Method A: Both units operate
simultaneously, modulating with load
variations. Each packaged chiller
operating thermostat senses the return
water temperature using standard
controls (See Figure 2.7C). The set point
of each thermostats will be set to
maintain the desired unloading. In
addition to that, for each chiller package,
the suction sensing hot gas by-pass
valve provides modulating capacity
reduction from 100% to approximately
30% on single compressor models with
hot gas by-pass.
Method B: Install units the same as
Method A, but add a third thermostat in
the return water, as shown in Figure
2.7E. This thermostat will be set to cycle
off one of the units when the load drops
below 50%. When this condition is
reached, the leaving mixed water
temperature will rise, causing the return
water temperature to rise and the unit
operating will load up. The "off" unit is
sequencing to start again before full
system load temperature is reached.
This system will be as stable as Method
A, in operation, but in normal air-
conditioning applications, this is not
detrimental. The advantage of Method B
is a better part load efficiency. Also a
lead-lag control can be added.
Summary of Contents for ACDS
Page 7: ...7 2 0 INSTALLATION FIGURE 2 3 2 ACDS RIGGING ACDS 010 ACDS 020...
Page 8: ...8 2 0 INSTALLATION ACDS 030 040 050 060 070 ACDS 080 090 100 120 ACDS 135 150 165 180...
Page 9: ...9 2 0 INSTALLATION FIGURE 2 4 2B DIMENSIONAL DATA ACDS 010...
Page 10: ...10 2 0 INSTALLATION ACDS 020...
Page 11: ...11 2 0 INSTALLATION ACDS 030...
Page 12: ...12 2 0 INSTALLATION ACDS 040...
Page 13: ...13 2 0 INSTALLATION ACDS 050 060 070...
Page 15: ...15 2 0 INSTALLATION ACDS 100 120...
Page 19: ...19 2 0 INSTALLATION ACDS 030 040 050 060 070 ACDS 080 090 100 120 135 150 ACDS 165 180...
Page 22: ...22 2 0 INSTALLATION FIGURE 2 7A FIGURE 2 7B FIGURE 2 7C FIGURE 2 7D FIGURE 2 7E...
Page 25: ...25 3 0 OPERATION FIGURE 3 2 1 TYPICAL PIPING SCHEMATIC ACDS 010 020 030...
Page 26: ...26 3 0 OPERATION ACDS 040 050 060 070...
Page 27: ...27 3 0 OPERATION ACDS 080 090 100 120...
Page 28: ...28 3 0 OPERATION ACDS 135 150...
Page 29: ...29 3 0 OPERATION ACDS 165 180...
Page 54: ...54 4 0 ELECTRICAL 4 9 TYPICAL WIRING SCHEMATIC ACDS 010...
Page 55: ...55 4 0 ELECTRICAL...
Page 56: ...56 4 0 ELECTRICAL ACDS 020...
Page 57: ...57 4 0 ELECTRICAL...
Page 58: ...58 4 0 ELECTRICAL ACDS 030...
Page 59: ...59 4 0 ELECTRICAL...
Page 60: ...60 4 0 ELECTRICAL ACDS 040...
Page 61: ...61 4 0 ELECTRICAL...
Page 62: ...62 4 0 ELECTRICAL ACDS 050 060 070...
Page 63: ...63 4 0 ELECTRICAL...
Page 64: ...64 4 0 ELECTRICAL ACDS 080 90...
Page 65: ...65 4 0 ELECTRICAL...
Page 66: ...66 4 0 ELECTRICAL...
Page 67: ...67 4 0 ELECTRICAL...
Page 68: ...68 4 0 ELECTRICAL ACDS 100...
Page 69: ...69 4 0 ELECTRICAL...
Page 70: ...70 4 0 ELECTRICAL...
Page 71: ...71 4 0 ELECTRICAL...
Page 72: ...72 4 0 ELECTRICAL ACDS 120...
Page 73: ...73 4 0 ELECTRICAL...
Page 74: ...74 4 0 ELECTRICAL...
Page 75: ...75 4 0 ELECTRICAL...
Page 76: ...76 4 0 ELECTRICAL ACDS 135...
Page 77: ...77 4 0 ELECTRICAL...
Page 78: ...78 4 0 ELECTRICAL...
Page 79: ...79 4 0 ELECTRICAL...
Page 80: ...80 4 0 ELECTRICAL ACDS 150...
Page 81: ...81 4 0 ELECTRICAL...
Page 82: ...82 4 0 ELECTRICAL...
Page 83: ...83 4 0 ELECTRICAL...
Page 84: ...84 4 0 ELECTRICAL ACDS 165 180...
Page 85: ...85 4 0 ELECTRICAL...
Page 86: ...86 4 0 ELECTRICAL...
Page 87: ...87 4 0 ELECTRICAL...