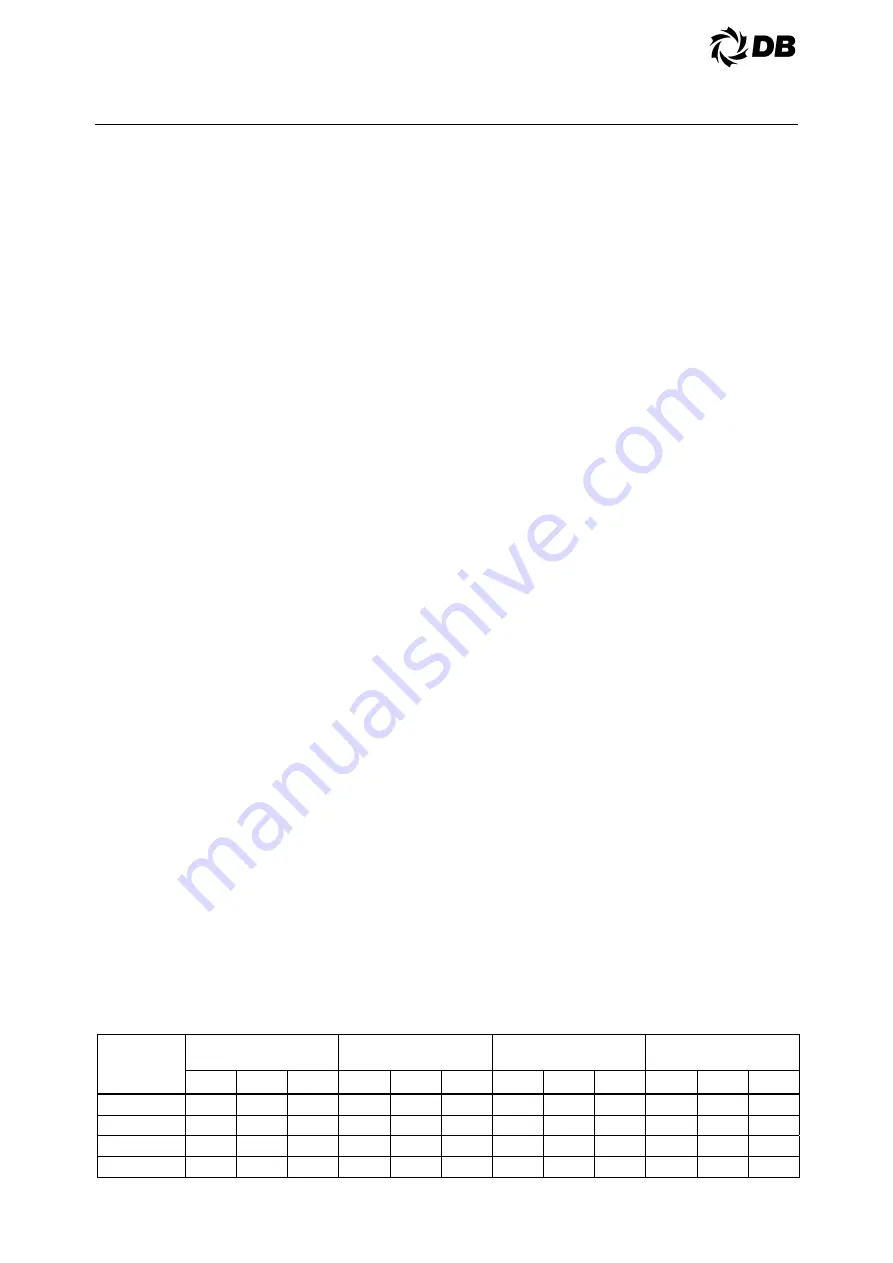
- 45 -
4.0 ELECTRICAL
4.3.6.3 Anti-Recycle Timer
The compressor motor requires an anti-
recycle time delay which prevents
restart for 15 minutes after a start. The
purpose of this feature is to avoid
frequent starts which tend to elevate
the motor winding temperature and
impose undue wear on contactors. The
controller will not restart the
compressor motor until the 15 minutes
have elapsed.
4.3.6.4 Load Control
The controller controls the leaving
water temperature within a narrow
deadband by pulsing load and/ or
unload solenoids on the compressor.
The load and unload solenoids position
the slide valve within the compressor to
control its capacity. The controller
determines a desired level of loading
and varies pulse duration depending on
difference between load target and
actual load. The load target is varied
based on rate of approach to desired
temperature preventing significant
temperature oscillations. The status of
the compressor can be observed by
displaying the compressor control point.
4.3.6.5 Ramp Control
Another feature of the controller is ramp
control, which is the ability to vary load
time of the machine from start. Often
when the machine is started, the water
in the chilled water circuit is warm, and
the unit will go to full load quickly. With
ramp control, the user can program the
computer so that it loads at a
predetermined rate. This is a valuable
tool, since it can help reduce power
consumption and demand charges.
Two variables are used to define the
ramp profile: Ramp rate and start point.
Ramp rate defines the length of time
the unit takes to load from start point to
full load. Start point is the percent of full
load at which the ramp begins. The
ramp rate A setpoint can be set
anywhere from 0.1 to 1.0, smaller
values producing slower loading rates.
The ramp start B setpoint can be set
anywhere between 0 and 50%. The
compressor will load quickly to this
value and then follow the ramp slope
from there. See Table 4.3.6.5 for ramp
rates at various settings.
4.3.6.6 Staging Control
On multiple-compressor machines,
when the controller determines that a
compressor is fully loaded and
temperature is not being maintained,
another compressor is added. When
unloading, a compressor is taken off
line when the computer determines that
the remaining compressors can control
water temperature.
4.3.6.7 Pumpdown
Control
This feature is to stored refrigerant in
condenser when compressor is
stopped. Pumpdown control will take
place when temperature set point is
achieved before compressor is being
cycled off or unit enable input is off.
The compressor will stop when suction
pressure is lower than pumpdown
setpoint, 65PSI [4.5BAR] (for R22) or
15 seconds (setpoint) delay timer is
elapsed.
TABLE 4.3.6.5 Ramp Rates for Several Setpoints (In Minutes)
Ramp
Rate
Setpoint
1 Comp.
Start Point Setpoint
2 Comp.
Start Point Setpoint
3 Comp
Start Point Setpoint
4 Comp
Start Point Setpoint
30% 50% 75% 30% 50% 75% 30% 50% 75% 30% 50% 75%
0.1
12.0 9.0 4.5 22.0 18.5 14.0 29.0 25.5 21.0 33.0 29.0 25.0
0.2
6.0 5.0 2.0 11.5 10.0 8.0 16.0 14.0 12.0 18.0 16.0 14.0
0.3
4.0 3.0 1.5 8.0 7.0 5.5 11.0 10.0 9.0 13.0 12.0 11.0
0.4
3.0 2.5 1.0 6.5 5.5 4.5 9.0 8.0 7.0 11.0 10.0 9.0
Summary of Contents for ACDS
Page 7: ...7 2 0 INSTALLATION FIGURE 2 3 2 ACDS RIGGING ACDS 010 ACDS 020...
Page 8: ...8 2 0 INSTALLATION ACDS 030 040 050 060 070 ACDS 080 090 100 120 ACDS 135 150 165 180...
Page 9: ...9 2 0 INSTALLATION FIGURE 2 4 2B DIMENSIONAL DATA ACDS 010...
Page 10: ...10 2 0 INSTALLATION ACDS 020...
Page 11: ...11 2 0 INSTALLATION ACDS 030...
Page 12: ...12 2 0 INSTALLATION ACDS 040...
Page 13: ...13 2 0 INSTALLATION ACDS 050 060 070...
Page 15: ...15 2 0 INSTALLATION ACDS 100 120...
Page 19: ...19 2 0 INSTALLATION ACDS 030 040 050 060 070 ACDS 080 090 100 120 135 150 ACDS 165 180...
Page 22: ...22 2 0 INSTALLATION FIGURE 2 7A FIGURE 2 7B FIGURE 2 7C FIGURE 2 7D FIGURE 2 7E...
Page 25: ...25 3 0 OPERATION FIGURE 3 2 1 TYPICAL PIPING SCHEMATIC ACDS 010 020 030...
Page 26: ...26 3 0 OPERATION ACDS 040 050 060 070...
Page 27: ...27 3 0 OPERATION ACDS 080 090 100 120...
Page 28: ...28 3 0 OPERATION ACDS 135 150...
Page 29: ...29 3 0 OPERATION ACDS 165 180...
Page 54: ...54 4 0 ELECTRICAL 4 9 TYPICAL WIRING SCHEMATIC ACDS 010...
Page 55: ...55 4 0 ELECTRICAL...
Page 56: ...56 4 0 ELECTRICAL ACDS 020...
Page 57: ...57 4 0 ELECTRICAL...
Page 58: ...58 4 0 ELECTRICAL ACDS 030...
Page 59: ...59 4 0 ELECTRICAL...
Page 60: ...60 4 0 ELECTRICAL ACDS 040...
Page 61: ...61 4 0 ELECTRICAL...
Page 62: ...62 4 0 ELECTRICAL ACDS 050 060 070...
Page 63: ...63 4 0 ELECTRICAL...
Page 64: ...64 4 0 ELECTRICAL ACDS 080 90...
Page 65: ...65 4 0 ELECTRICAL...
Page 66: ...66 4 0 ELECTRICAL...
Page 67: ...67 4 0 ELECTRICAL...
Page 68: ...68 4 0 ELECTRICAL ACDS 100...
Page 69: ...69 4 0 ELECTRICAL...
Page 70: ...70 4 0 ELECTRICAL...
Page 71: ...71 4 0 ELECTRICAL...
Page 72: ...72 4 0 ELECTRICAL ACDS 120...
Page 73: ...73 4 0 ELECTRICAL...
Page 74: ...74 4 0 ELECTRICAL...
Page 75: ...75 4 0 ELECTRICAL...
Page 76: ...76 4 0 ELECTRICAL ACDS 135...
Page 77: ...77 4 0 ELECTRICAL...
Page 78: ...78 4 0 ELECTRICAL...
Page 79: ...79 4 0 ELECTRICAL...
Page 80: ...80 4 0 ELECTRICAL ACDS 150...
Page 81: ...81 4 0 ELECTRICAL...
Page 82: ...82 4 0 ELECTRICAL...
Page 83: ...83 4 0 ELECTRICAL...
Page 84: ...84 4 0 ELECTRICAL ACDS 165 180...
Page 85: ...85 4 0 ELECTRICAL...
Page 86: ...86 4 0 ELECTRICAL...
Page 87: ...87 4 0 ELECTRICAL...