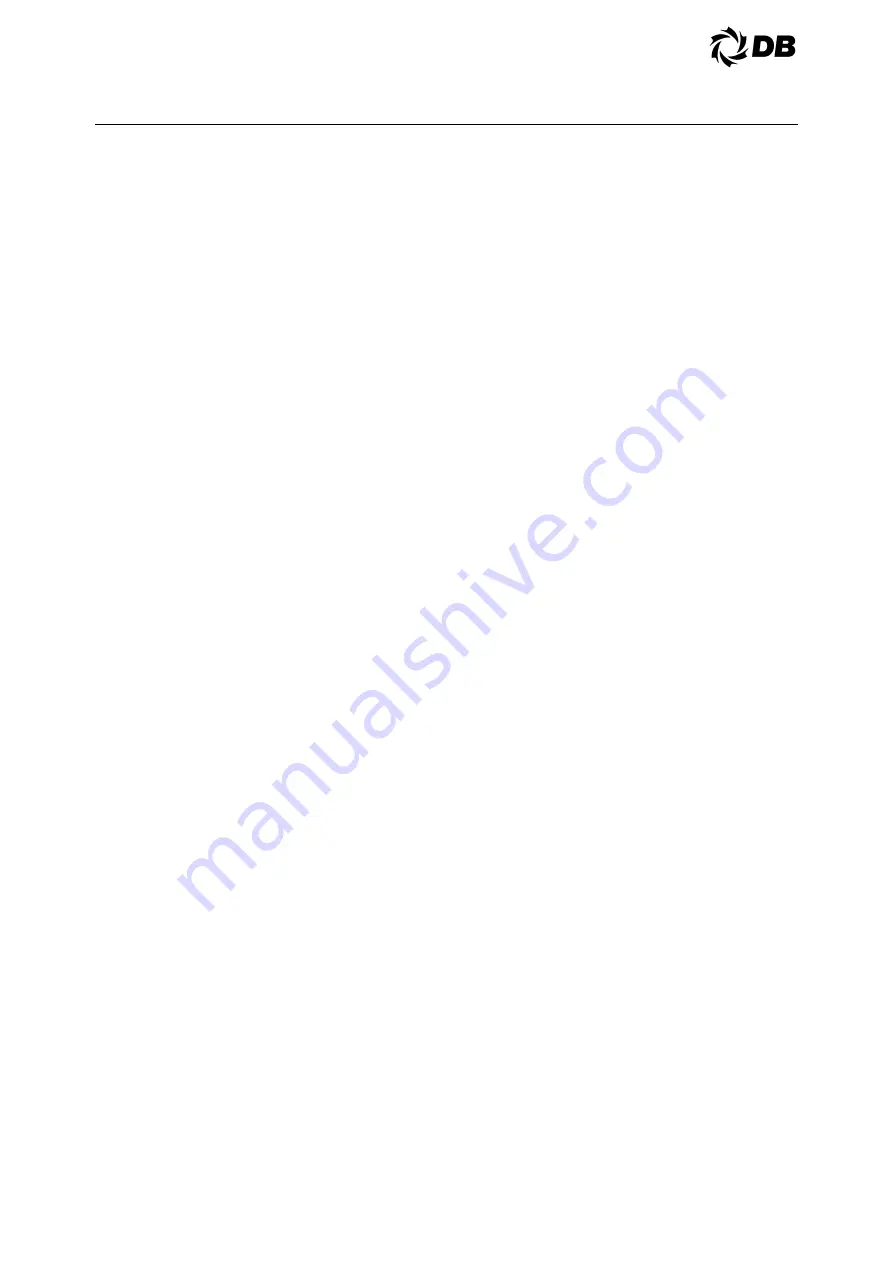
- 24 -
3.0 OPERATION
3.1 GENERAL
The unit should be started up only by a
refrigeration technician who is familiar with the
accepted operation practices for refrigeration
systems.
Use the scroll unit start-up report, to record all
temperature, pressure, electrical readings and
control settings. A copy must be forwarded to
Dunham-Bush service department, before
warranty will be honored.
3.2 UNIT
PIPING
See Figure 3.2.1 for typical unit piping
schematics.
3-3 AIR COOLED PACKAGES
START-UP
The unit is ready for start-up when the following
procedures have been completed:
1. Water piping for the evaporator is installed
and tested.
2. Electrical connections are made and properly
fused.
3. Unit has been leak tested, leaks corrected
and charge completed.
4. Compressor crankcase heater(s) has been
energized for a minimum of 24 hours.
5
.
Calibrated refrigerant gauges have been
connected to the suction and discharge ports.
6. Turn On the chilled water pump, check
direction of rotation and adjust the water flow
through the evaporator to the specified flow
rate. Bleed off all entrained air.
7. Manually energize the fan starters and check
the fan rotation. Fans should pull air through
the condenser coil and discharge vertically
upwards. Rotation can be changed on 3-
phase motors by interchanging only two wires
on the main terminal block.
8. Check all refrigerant valves to be sure they
are open.
9. Proceed to section 3.4 System Start-Up.
3.4 SYSTEM
START-UP
1. Before starting the compressor(s), check all
three phases of supply voltage, of all legs of
the motor. They must be within ±10% of the
nameplate voltage.
2. Start compressor(s), check the gauges and
note if the pressures are within the prescribed
limits.
3. Check the refrigerant sight glass to be sure it
is free of bubbles. If not, charge as specified
per section 4.8 Charging.
4. Shut the compressor down and check the
compressor crankcase sight glass for oil level.
It should be between 1/2 to 3/4 of the
complete sightglass. If not, see Section 3.5
Lubrication.
5. Restart the compressor. After an hour of
operation the expansion valve superheat
setting should be checked, it should be
between 8°F [4.4°C] and 10°F [5.6°C] at full
load design conditions. In some instances, it
will be necessary to lower the superheat
setting to ensure proper distribution. Turn the
TX valve adjustment stem clockwise to
increase the superheat setting and
counterclockwise to decrease the setting. Be
sure and allow ample time between each
adjustment for the system to rebalance.
6. The temperature of the chilled water both in
and out, should be checked to insure the unit
is operating within the desired temperatures.
3.5 LUBRICATION
3.5.1 OIL
LEVEL
A properly operated unit should run with
the compressor crankcase warm to touch.
Check oil level frequently to see that a
sufficient amount of oil remains in the
crankcase. Compressor oil level can be
checked by the sight glass. To make sure
that proper oil level is observe, operate
the compressor for 15 minutes, then stop
the compressor. Oil should appear from
1/2 to 3/4 in the sight glass with the
compressor stopped.
Summary of Contents for ACDS
Page 7: ...7 2 0 INSTALLATION FIGURE 2 3 2 ACDS RIGGING ACDS 010 ACDS 020...
Page 8: ...8 2 0 INSTALLATION ACDS 030 040 050 060 070 ACDS 080 090 100 120 ACDS 135 150 165 180...
Page 9: ...9 2 0 INSTALLATION FIGURE 2 4 2B DIMENSIONAL DATA ACDS 010...
Page 10: ...10 2 0 INSTALLATION ACDS 020...
Page 11: ...11 2 0 INSTALLATION ACDS 030...
Page 12: ...12 2 0 INSTALLATION ACDS 040...
Page 13: ...13 2 0 INSTALLATION ACDS 050 060 070...
Page 15: ...15 2 0 INSTALLATION ACDS 100 120...
Page 19: ...19 2 0 INSTALLATION ACDS 030 040 050 060 070 ACDS 080 090 100 120 135 150 ACDS 165 180...
Page 22: ...22 2 0 INSTALLATION FIGURE 2 7A FIGURE 2 7B FIGURE 2 7C FIGURE 2 7D FIGURE 2 7E...
Page 25: ...25 3 0 OPERATION FIGURE 3 2 1 TYPICAL PIPING SCHEMATIC ACDS 010 020 030...
Page 26: ...26 3 0 OPERATION ACDS 040 050 060 070...
Page 27: ...27 3 0 OPERATION ACDS 080 090 100 120...
Page 28: ...28 3 0 OPERATION ACDS 135 150...
Page 29: ...29 3 0 OPERATION ACDS 165 180...
Page 54: ...54 4 0 ELECTRICAL 4 9 TYPICAL WIRING SCHEMATIC ACDS 010...
Page 55: ...55 4 0 ELECTRICAL...
Page 56: ...56 4 0 ELECTRICAL ACDS 020...
Page 57: ...57 4 0 ELECTRICAL...
Page 58: ...58 4 0 ELECTRICAL ACDS 030...
Page 59: ...59 4 0 ELECTRICAL...
Page 60: ...60 4 0 ELECTRICAL ACDS 040...
Page 61: ...61 4 0 ELECTRICAL...
Page 62: ...62 4 0 ELECTRICAL ACDS 050 060 070...
Page 63: ...63 4 0 ELECTRICAL...
Page 64: ...64 4 0 ELECTRICAL ACDS 080 90...
Page 65: ...65 4 0 ELECTRICAL...
Page 66: ...66 4 0 ELECTRICAL...
Page 67: ...67 4 0 ELECTRICAL...
Page 68: ...68 4 0 ELECTRICAL ACDS 100...
Page 69: ...69 4 0 ELECTRICAL...
Page 70: ...70 4 0 ELECTRICAL...
Page 71: ...71 4 0 ELECTRICAL...
Page 72: ...72 4 0 ELECTRICAL ACDS 120...
Page 73: ...73 4 0 ELECTRICAL...
Page 74: ...74 4 0 ELECTRICAL...
Page 75: ...75 4 0 ELECTRICAL...
Page 76: ...76 4 0 ELECTRICAL ACDS 135...
Page 77: ...77 4 0 ELECTRICAL...
Page 78: ...78 4 0 ELECTRICAL...
Page 79: ...79 4 0 ELECTRICAL...
Page 80: ...80 4 0 ELECTRICAL ACDS 150...
Page 81: ...81 4 0 ELECTRICAL...
Page 82: ...82 4 0 ELECTRICAL...
Page 83: ...83 4 0 ELECTRICAL...
Page 84: ...84 4 0 ELECTRICAL ACDS 165 180...
Page 85: ...85 4 0 ELECTRICAL...
Page 86: ...86 4 0 ELECTRICAL...
Page 87: ...87 4 0 ELECTRICAL...