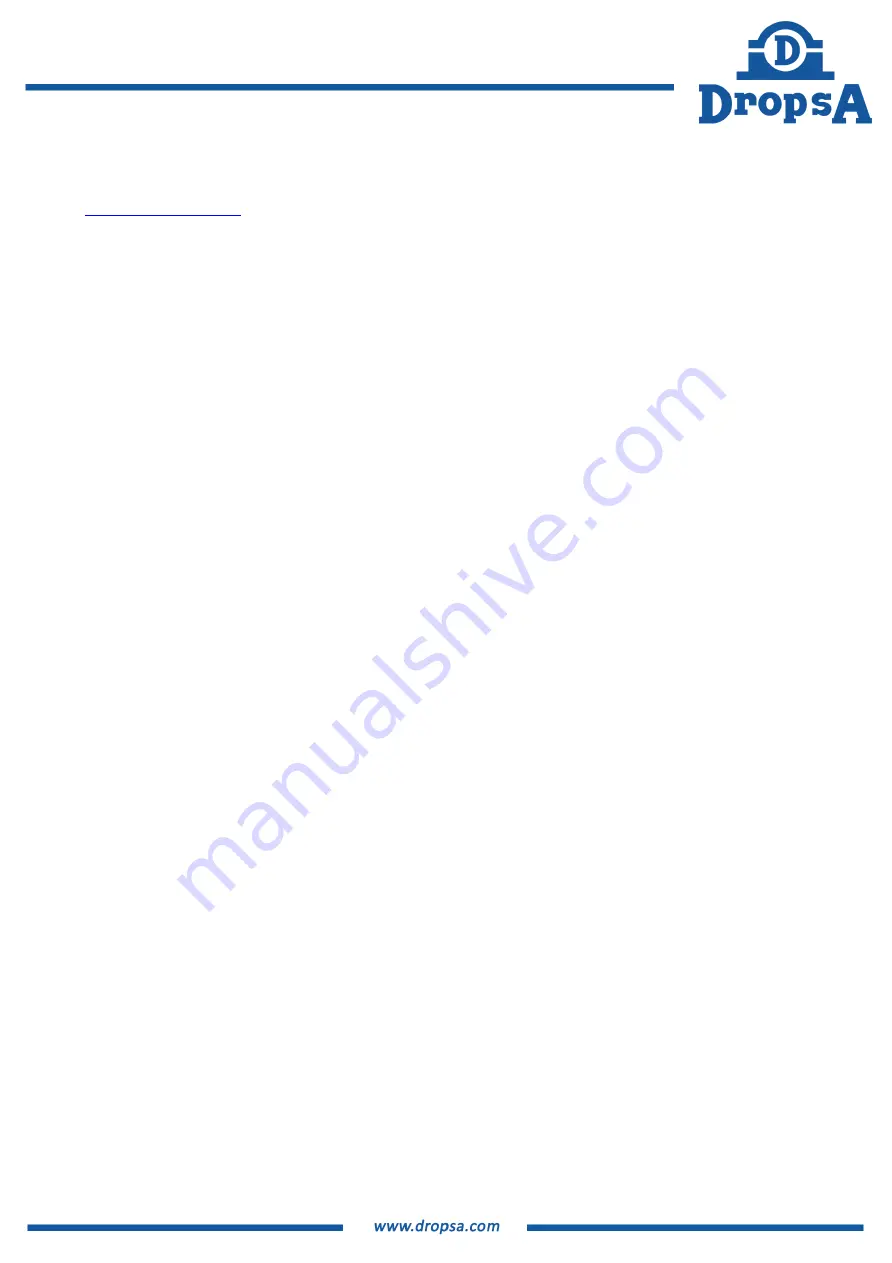
3
INTRODUCTION
This Operation and Maintenance Manual refers to the
MaXtreme
product for dry machining processes.
You can obtain the latest version by requesting it from the Technical Sales Department, or by consulting our website
This operation and maintenance manual contains important information for the health and safety protection of the
personnel who intends to use this equipment. This manual must be read carefully and kept so that it is always
available to the operators who want to consult it.
1. GENERAL DESCRIPTION
MaXtreme
is designed for near-dry machining, a technology recently designed to replace traditional cooling systems
and immersion in pure or emulsified oil in machining environments for chip removal, where a controlled flow of
compressed air transports minimal amounts of cutting oil in "aerosol" format to the cutting surface. This technology
ensures lubrication of the cutting surface and enables high-performance machining while offering longer tool life and
reduced cycle times. Removing coolant from the process also provides important environmental benefits and reduces
the high cost of the waste product.
The aerosol is transported to the cutting surface from the outside (via nozzles positioned around the tool) or from the
inside, also known as "through the tool".
Internal lubrication is the most difficult to achieve due to the coalescence of oil particles inside the tool.
MaXtreme
solves this by generating ultra-thin particles that can pass through the rotating tool without hindrance caused by
centrifugal force.
MaXtreme
combines years of research and development in aerodynamic and fluid-dynamic effects to produce oil
particles in an ultra-fine aerosol (diameter below the micron) that allow high-performance machining.
The double vortex solution is a revolutionary system that allows minimal lubrication and superior internal or external
near-dry lubrication.
In fact, for some applications, the second nozzle optimised for higher pressures is designed to increase the aerosol
flow directly on tools with minimum passage sections, thus offering better chip outflow and constant tool cooling.
This option can operate in a hybrid configuration with the primary nozzle delivering constant and rich aerosol even at
low flow rates, reducing the 'dead zone' at extremely low flow rates.
In addition to the Machinery Directive 2006/42/EC and, due to the increase in pressure performance up to 20 bar,
MaXtreme
is certified according to PED Directive 2014/68/EU, according to which the circuit identifies the following
characteristics:
- PED RISK CATEGORY = I
- PED module: Module A
- Maximum allowable pressure: 22 Barg
- Test pressure: 36 Barg
- Permissible temperature: min 0 °C – max +60 °C
- Fluid group: Group 2
1.2 SELF-ADAPTING AND HYBRID FEATURE
The self-adaptive and hybrid functions mean that no adjustments between tool changes or complex programming
configurations are necessary. The system is mounted and adapts automatically.
How it works:
the aerosol is produced using a new vortex generator that has an improved operational envelope.
A special conical exhaust nozzle design combined with a controlled surface finish fragments the oil particles by
decelerating them at a controlled speed to create an aerosol with particles smaller than a micron. When the flow
rates become very high (typically for very large utensils), an air pressure increase valve opens to integrate the airflow
for the removal of chips and heat and therefore the density is reduced of the aerosol not required for this type of
processing operation.