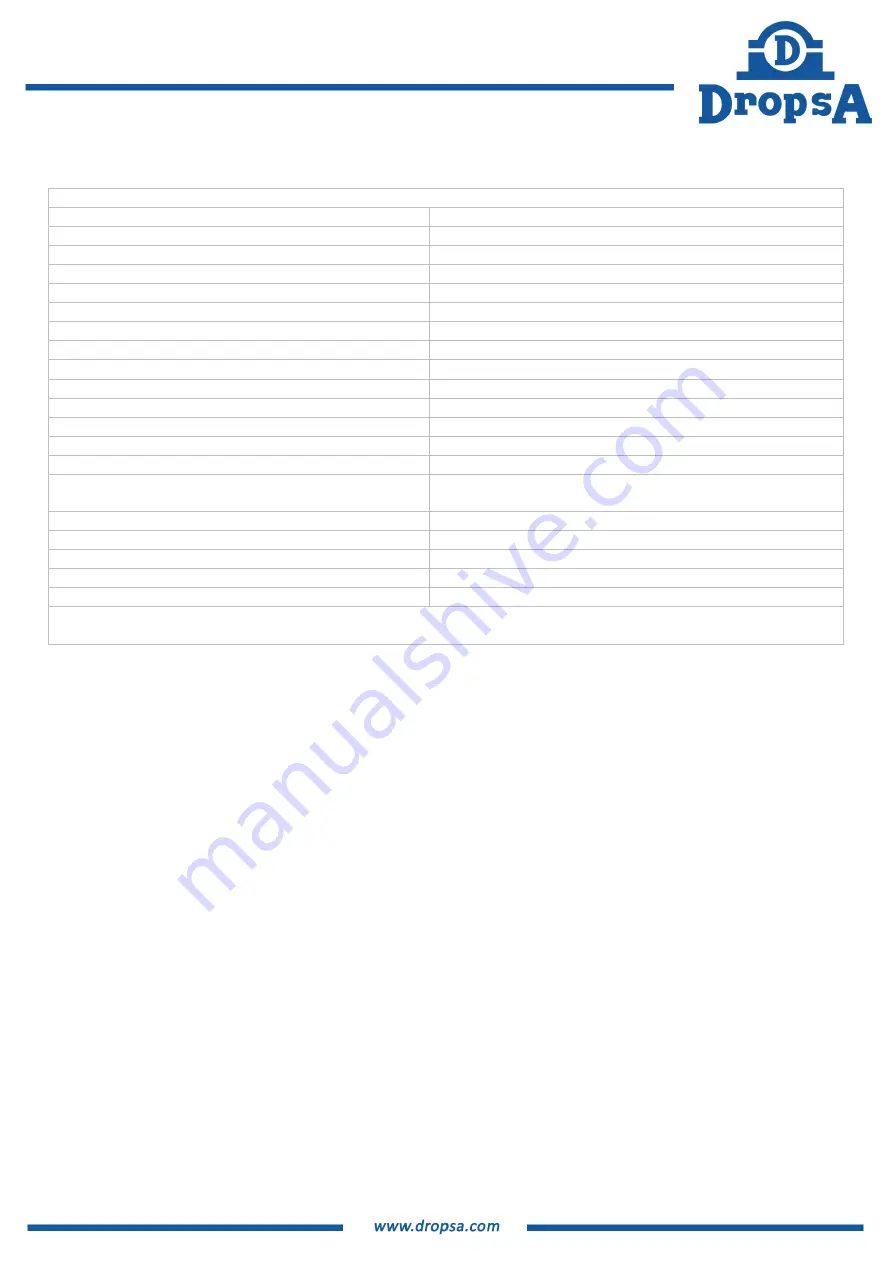
11
5. TECHNICAL CHARACTERISTICS
Technical characteristics
*LP nozzle Air Supply:
6 Bar (87 psi)
*LP nozzle air/outlet flow rate:
35000 Nl/h (W/additional air) (1236 cfh) 6 Bar
*Oil Flow rate:
220 ml/h (13.2 cu/h) 20°C
*HP nozzle Air Supply:
20 Bar (290 psi)
*HP nozzle air/outlet flow rate:
6500 Nl/h (229.5 cfh)
*Nozzle oil flow HP:
9.5 ml/h
(0.6 cu/h) 20°C
Min. working diameter LP nozzle (6 bar)
2 mm (7000 Nl/h) (247 cfh)
Minimum working diameter HP nozzle (20 bar)
0.8 mm (3500 Nl/h) (123 cfh)
Reservoir capacity:
2 litres (0.50 gallons)
Air supply hose:
Ø12mm.(0.47 in)
Usage tube:
Ø12 ÷ 16 mm (0.47 ÷ 0.6 in.)
Number of aerosol outlets:
1~3
Lubricant
DropsA
recommends
MaXtreme
OIL for the best results
Degree of protection:
IP 65
Electro-pneumatic valve power supply:
(Optional)
24VDC200mA
Operating temperature
0°C ÷ +60°C
Storage temperature
-10°C ÷ +80°C
Noise (distance 1mt)
70 dB “A”
Escape valve:
22 bar
Reservoir pressure gauge
:
0~25 Bar
All the values on the technical characteristics refer to Ø12 in/out connections
* The value is variable depending on the outlet Ø or the tool chosen for HP nozzle version