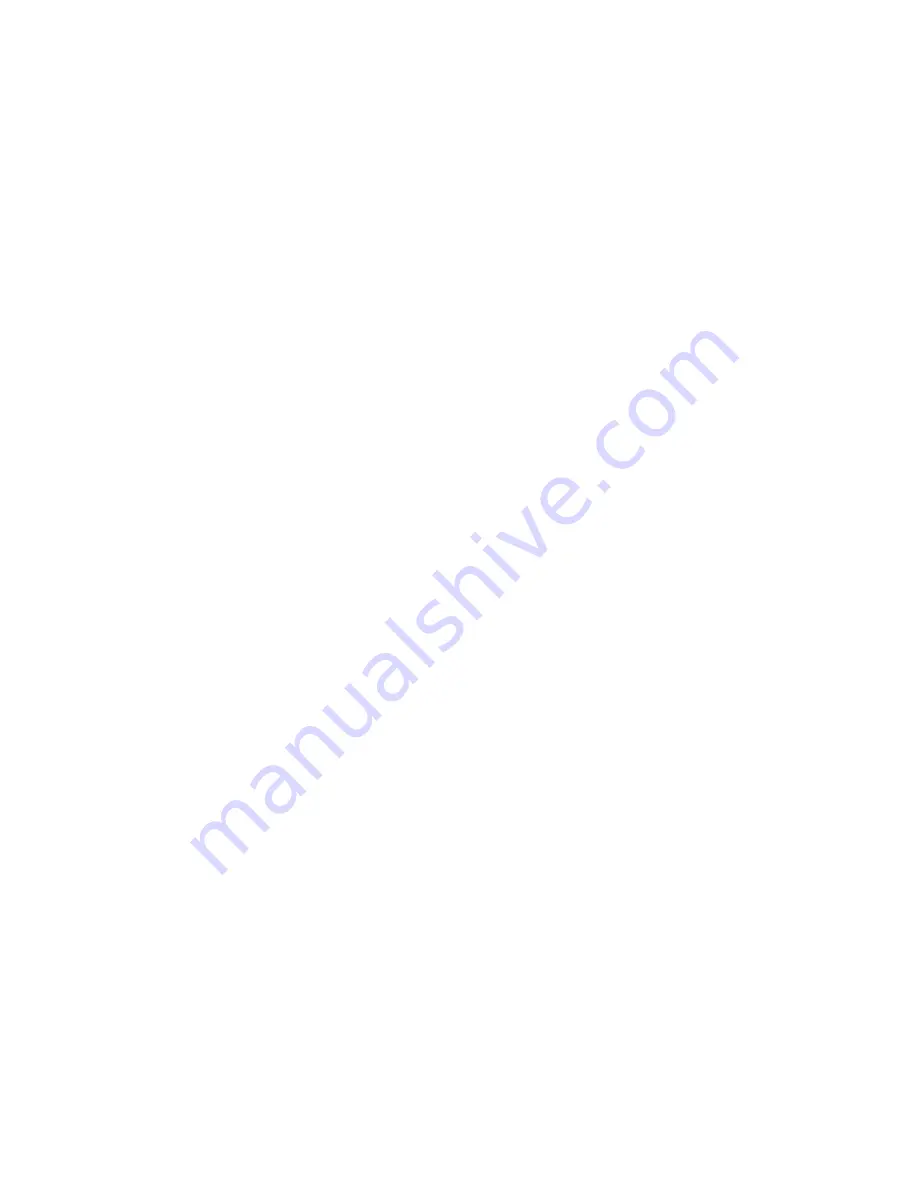
Clicking the Secondary Signal button starts the calibration procedure for the secondary input signal sen-
sor. The procedure will ask the user to:
1. Enter a low value for the measurement (e.g. 4.00 mA).
2. Set the input to that value.
3. Enter a high value for the measurement (e.g. 20.00 mA).
4. Set the input to that value.
Calibrating the secondary signal can be done most easily with a variable current source with a 250 ohm
resistor (actually used!). Changing the value of the resistor calls for re-calibration of the secondary sig-
nal, since the secondary signal sensor actually measures voltage rather than current.
Clicking a tab brings up the corresponding page to examine and modify calibration parameters and initi-
ate calibration procedures. After complete calibration from a page, click:
•
OK
button to accept changes entered, download to SVI, and exit to manual mode.
•
Cancel
button to discard changes entered and exit to manual mode.
•
Range
,
Tuning
, or
Signal Cal
. tab to continue examine and modify calibration.
91