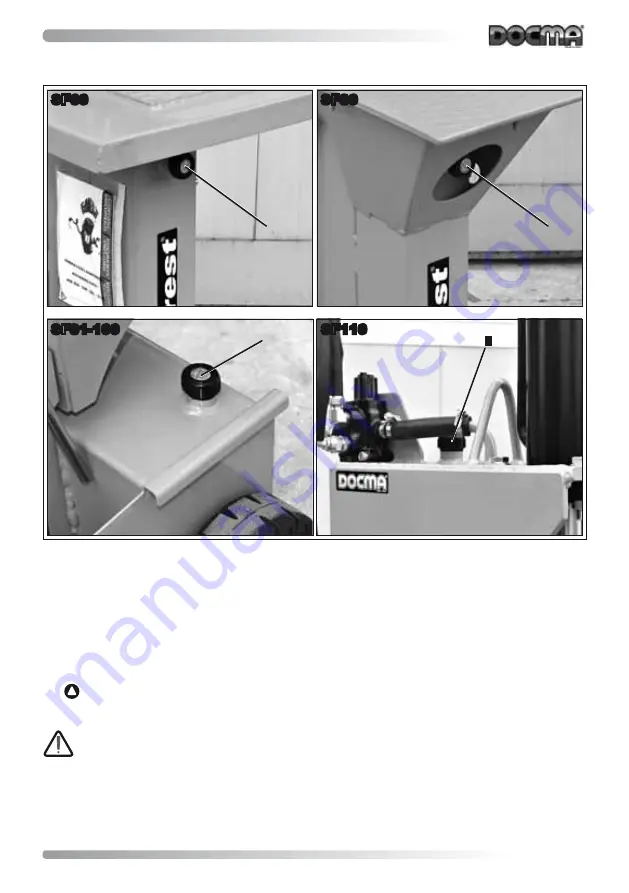
25
SF81-100
SF110
SF60
SF80
1
2
2
1
Fig. 12
Once a day check:
►
The tightness of the hydraulic couplings and hoses.
If the hydraulic hoses are damaged or visibly cracked they must be replaced.
►
The wear on the surfaces where the pads slide; if there is excessive play, have these checked or
replaced by the reseller.
►
The edge of the blade on the wedge; if this needs to be sharpened, contact the reseller.
►
Keep the motor cooling air inlet clean, using compressed air, and clean the motor casing and
the power switch.
When using compressed air, wear personal protective equipment (safety glasses,
dust mask, etc.).