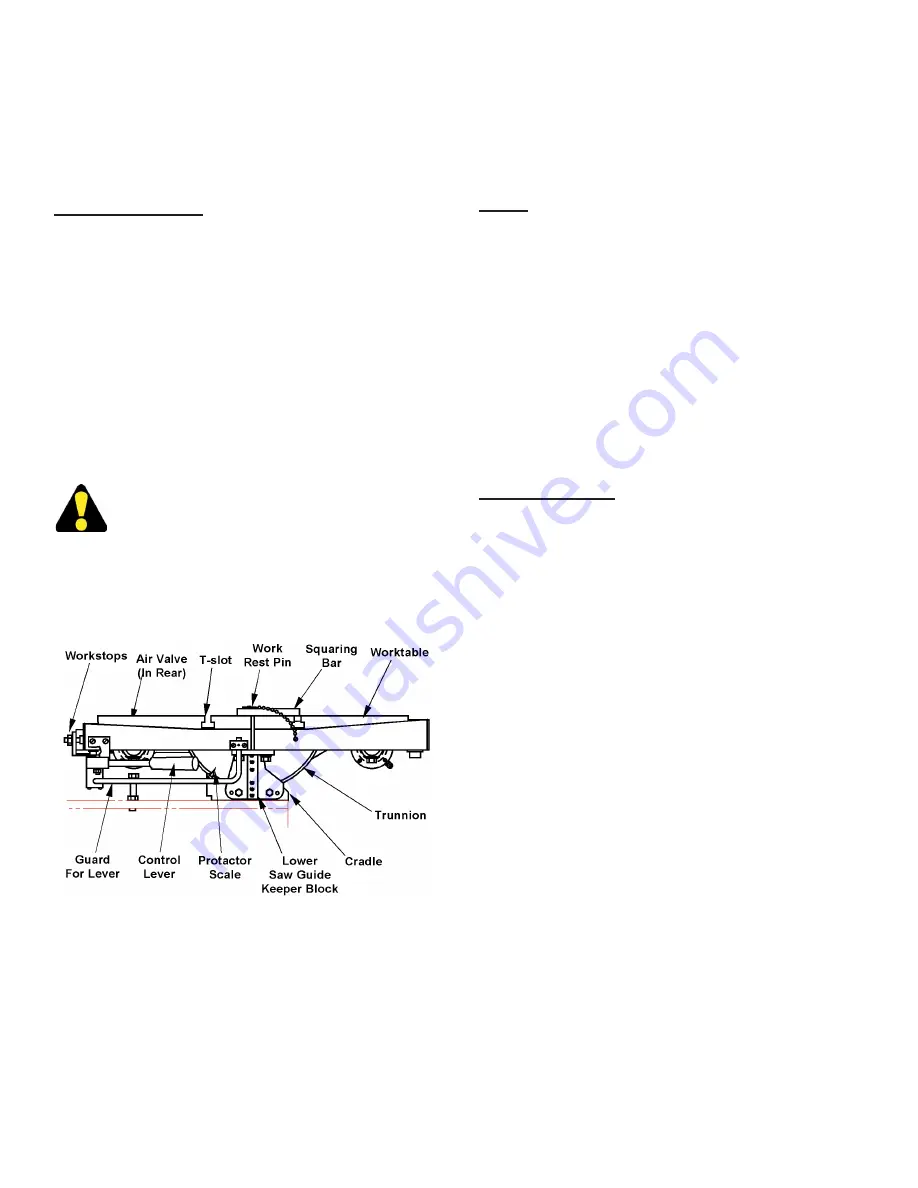
21
4.
Air power feed option can be added to assist in
moving the workpiece through the saw band.
5.
The handle must be removed for saw band
changing.
HMD Hydraulc Table
1.
This factory-installed hydraulic-powered worktable
has a 36 inch (914.4 mm) or a 60 inch (1524.0 mm)
stroke instead of the standard table. The HMD-36
table's working surface is 34 by 42 inches (863.6 by
1066.8 mm). The HMD-60 table's working surface
is 34 by 68 inches (863.6 by 1727.2 mm).
2.
Information covering installation, operation and
maintenance of the optional HMD-36 or 60 table are
provided in a seperate instruction manual included
with the machine.
AIR-POWERED WORKTABLE
Ths attachment reduces the machne's work
heght capacty by one (1) nch (25. mm).
1.
This optional worktable provides a 24 by 30-1/2 inch
(609.6 by 774.7 mm) working surface with coolant
return troughs. The worktable can be tilted up to
6° left and 45° right when using this attachment. It
has two (2) T-slots for work fixture clamping.
Air-Powered Worktable.
2.
The worktable's air-amplified feed system is lever
controlled and allows 12 inches (304.8 mm) of
worktable travel. Light hand pressure against the
lever will move the worktable in forward motion.
Release the lever and pull back the worktable
manually.
3.
The worktable has a work rest pin that acts as a
workstop when inserted into the sawing slot. Other
worktable features are:
(a)
A squaring bar that fits
into a worktable T-slot to hold stockpieces during
production sawing;
(b)
Locks that permit the loading
and positioning of heavy stock;
(c)
Special center
plates for filing and polishing operations.
Set-Up
1.
Position the workstops located on the left side of
the worktable to limit travel. The front stop controls
cut depth; the rear stop minimizes unnecessary
travel. Stops are positioned by:
(a)
Loosening
the locknuts;
(b)
Sliding the stops to the desired
position; and
(c)
Tightening the locknuts.
2.
To tilt the worktable:
(a)
Use the wrench provided
to reach through the machine frame and under
the worktable to loosen the tilt locknut;
(b)
Tilt
the worktable manually until the pointer reaches
desired angle shown on the scale;
(c)
Tighten the
tilt locknut.
Producton Sawng
1.
Place the rest pin into the worktable's sawing slot to
serve as a workstop. Then:
(a)
Place the squaring
bar in the worktable's T-slot to act as the stock
holder.
Remove the rest pn and squarng bar
for contour sawng.
2.
Place stock on the worktable and secure it at the
desired position. Then:
(a)
Use the control lever to
carefully move the table forward until the saw band
has just started cutting into the workpiece;
(b)
Push
the control lever to obtain the desired feed force
(feed force will return to zero (0) when the lever is
released).
DBW-15 BUTTWELDER
1.
Information covering blade welding, plus operation
and maintenance of the optional DBW-15 Buttwelder
(with flash grinder and blade shear) are provided in
a seperate instruction manual.
OPTIONAL SAW GUIDE BLOCKS
1.
It is possible to equip the machine with precision,
heavy-duty, high speed, insert-type saw guides or
roller saw guides.
WORKTABLE OPTIONS (Continued....)