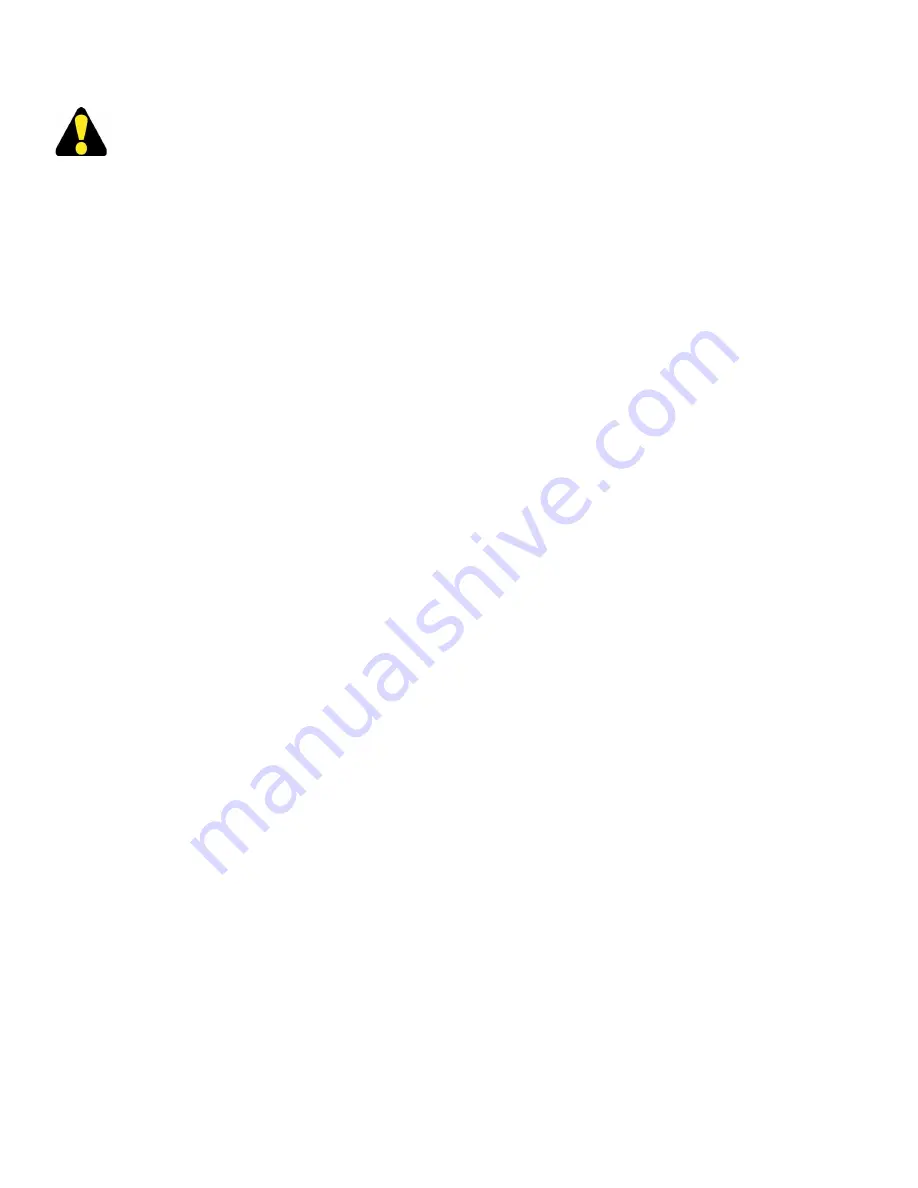
16
TROUBLE SHOOTING
Repar and adjustment procedures should be
made by experenced mantenance personnel,
or by a DoALL servce representatve.
Reference to the machne's electrcal
schematc wll be helpful.
MACHINE WON'T START
1.
Make sure the disconnect switch is in the "ON"
position.
2.
Make sure the bandwheel doors are closed.
3.
Circuit breakers may have tripped.
4.
Make sure the
Emergency Stop
pushbutton is reset
(turn the button head
clockwse
).
5.
Check the overload reset on the drive motor starter.
Starting and stopping the machine a number of
times in quick succession, or an overload, will trip
the starter overload switch. Locate and correct the
trouble, then push the overload reset switch.
6.
Check the transformer for faulty operation.
MACHINE VIBRATION
1.
Check for unbalanced bandwheels.
2.
Check for worn or unbalanced band drive belts.
3.
Check for an incorrectly shimmed machine base.
SAW BAND VIBRATION
1.
Incorrect band speed or feed force is being used.
2.
Choice of blade pitch is incorrect.
3.
Stock is not being clamped firmly to the worktable
and/or optional vise jaws.
4.
Check for worn or improperly adjusted saw guide
inserts.
5.
Check for a worn saw guide back-up bearing.
6.
Check for a loose post. Adjust the two (2) spring
plungers if necessary.
7.
Check for a poor weld in the saw band.
8.
Check for an incorrect saw band tension setting.
SAW BAND IS CUTTING INACCURATELY
1.
Check for worn blade teeth. Inserts that are too
wide for the blade will damage the teeth set.
2.
Check for scale on the stock.
3.
The saw band may be too wide if a radius is being
cut.
4.
Check for incorrect saw band, post or insert
alignment.
5.
Incorrect band speed or feed force is being used.
6.
Coolant (if supplied) is not being applied evenly to
both sides of the saw band.
7.
Check for an incorrect saw band tension setting.
8.
The upper saw guide is not located close enough
to the stock.
9.
Check for worn or loosely-adjusted saw guide
inserts.
EXCESSIVE INSERT AND BLADE WEAR
1.
Inserts or roller saw guide are adjusted too tightly
on the saw band.
2.
High band speed is causing friction (using roller
saw guides may be adviseable). Increase coolant
(if supplied) volume to better lubricate the saw
band.
3.
The back-up bearing may need replacement.
4.
Check for incorrect saw band tension setting.
PREMATURE BLADE TEETH DULLING
1.
The saw band is not being "broken" in on the first few
cuts. Reduce the feeding pressure when making
these cuts.
2.
Band speed is too high (this causes abrasion).
3.
Saw band pitch is too coarse.
4.
Coolant (if supplied) is not properly covering the
saw band.
5.
The cutting rate is too high.