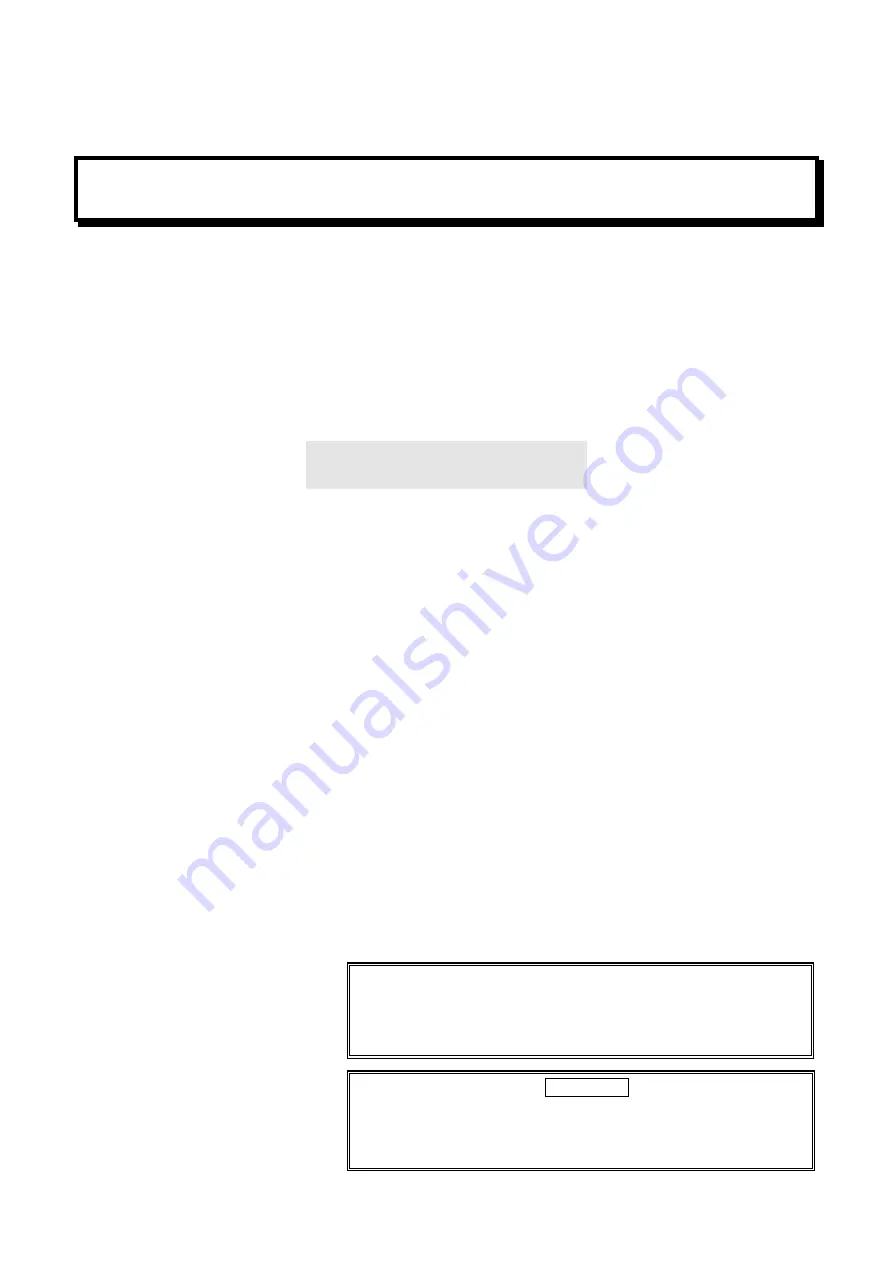
2016-06
INSTALLATION MANUAL
Automatic Surface Grinder
DAG810
Software Version: JUM0001***
Copyright of this document is owned by DISCO CORPORATION
("DISCO"). No part of this document may be copied or reproduced
in any form or by any means, without the express written permission
of DISCO. Also, this document may not be disclosed or transferred
to third parties.
UJUSNE*003F
This document is printed on recyclable Lint-Free Paper.
- The blue paper is recyclable as used paper just like plain paper.
- The cover paper and adhesive portions are non-recyclable.
(Remove the cover and adhesive portions before recycling.
Recycle the blue paper only.)
Summary of Contents for DAG810
Page 85: ......