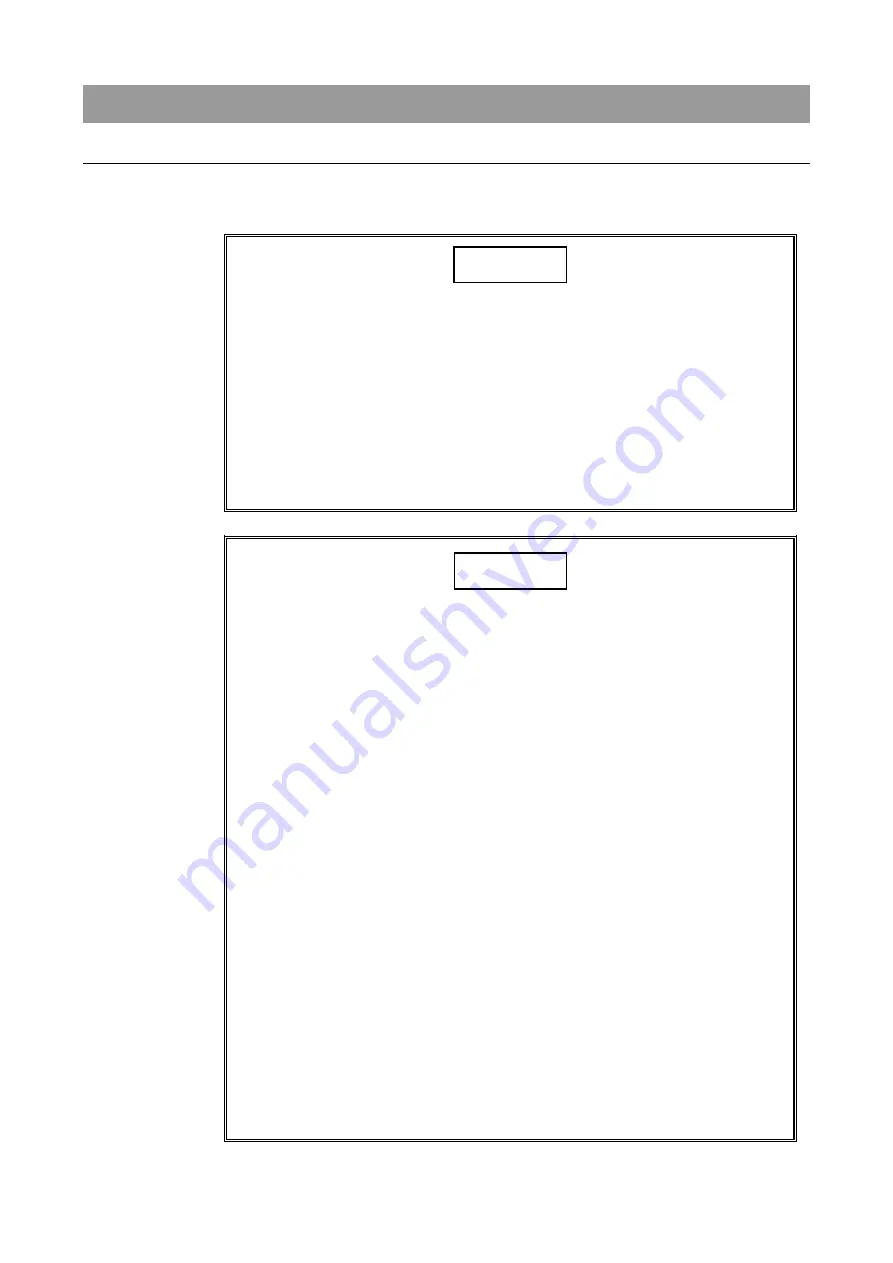
A-2
1. General Safety Precautions
General safety precautions
This section describes the general safety precautions that should be understood
before operation and observed during operation.
CAUTION
Machine installation environment
Comply with the recommended machine installation conditions
(such as room temperature, humidity or temperature of spindle
coolant water and wheel coolant water). If the machine is installed in
an environment that does not conform to the installation conditions
recommended by DISCO, rust formation may occur due to moisture
condensation or other factor, thereby adversely affecting the cutting
accuracy.
For the recommended environmental conditions, see section C-1 of
Installation Manual, [Installation Specifications and Environment].
N O T I C E
- Responsibility for instructing workers
Instruct the operators and maintenance personnel to read the
safety precautions set forth in the Maintenance Manual before
proceeding to work. Also, if the operator performs various tasks,
direct them to read the points of note concerning the safety given in
the respective manuals.
The written instructions for this machine are Installation Manual,
Operation Manual, Data Maintenance Manual, Maintenance
Manual and Technical Reference.
- Responsibility for instructing workers who don't seem to understand
the points of note
For the workers who don't seem to understand what is given in the
manuals, explain the safety items described in this chapter so that
they understand what the points mean.
- Regular inspection
The machine must be inspected on a regular basis.
If any accidents occur while an appropriate regular inspection
program is not adhered to, DISCO is not responsible for the results.
- Maintenance personnel
Maintenance must be conducted by qualified personnel who have
received the maintenance training.
- Proper installation of safety device
If the covers or other parts with safety interlocks are broken,
immediately stop the machine and repair broken parts.
Sample