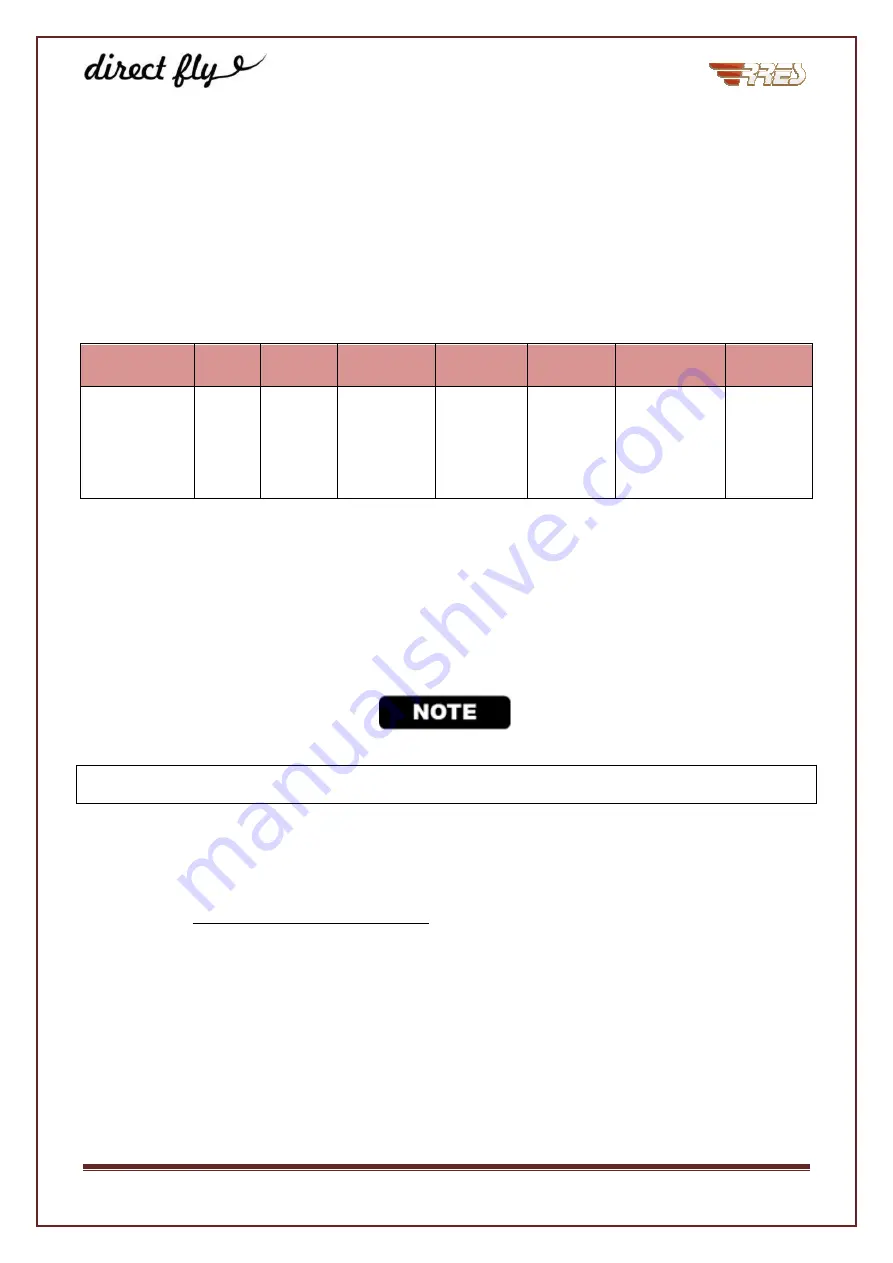
AIRCRAFT MAINTENANCE MANUAL
DFE-AMM-AR1
Rev. 1 – 07/24/2014
10-7
Application of smoothing layer
After preparation of mixture (for material recommendation see tab below) and its eventual
thickening to enhance the non curtaining capability (for vertical or lower areas) is performed its
application onto the repair area by means of a spatula. For better distribution of deposited
material on irregular surface it is possible to form it through the laid PE or PP transparent folia.
After proper application the layer is without bubbles. Deposit thicknesses given by necessary
thickness of surrounding layers (leveling) and ranges from 0.2 to 10 mm (0.0079 – 0.394 in) in
one deposit.
Recommended materials for mixture preparation for application of leveling layer
Manufacturer,
name
Type
Mixing
ration
Dwelling
Rate of
setting
Time of
setting
Temperature
Fillers
HUNTSMAN,
VANTICO,
Araldite 2011
(AW106 +
HV953U)
epoxy
A:B =
100:80
to be
processed
within
100min (for
0.1 kg
mixture)
40%
24 hours
(32hrs)
20 - 35°C
(17 - 20°C)
thickening:
Aerosil,
micro balls
Grinding
Grinding or eventually sealing the surface is made after setting the mixture and possible
tearing off the used folia. It is suitable to start grinding with grain size up to 160 and finish with
grain size of at least 400. It is carried out by dry grinding equipment with suction from the
grinding area. Al2O3 (fused corundum) can be used as grinding material. Basic material of
the part must not be diminished at grinding.
Especially in case of Carbon/Kevlar stiffener in the basic part, grinding through up to the stiffener must not
occur (complication - see note about preparatory grinding at medium damage).
Finishing
See Section 11 – Painting and Coatings..
•
Task proper accomplishment check: Visual check